In the world of materials science, nanotechnology, and various industrial processes, the ability to reduce particle size is crucial. Powder milling, therefore, plays a vital role in many applications. Two prominent technologies used for this purpose are the planetary ball mill and the roller jar mill. This article will delve into the intricacies of these two milling methods, examining their mechanisms, advantages, and the key factors that influence their selection for specific powder milling applications. We aim to provide a comprehensive guide that illuminates the nuances of these important pieces of equipment.
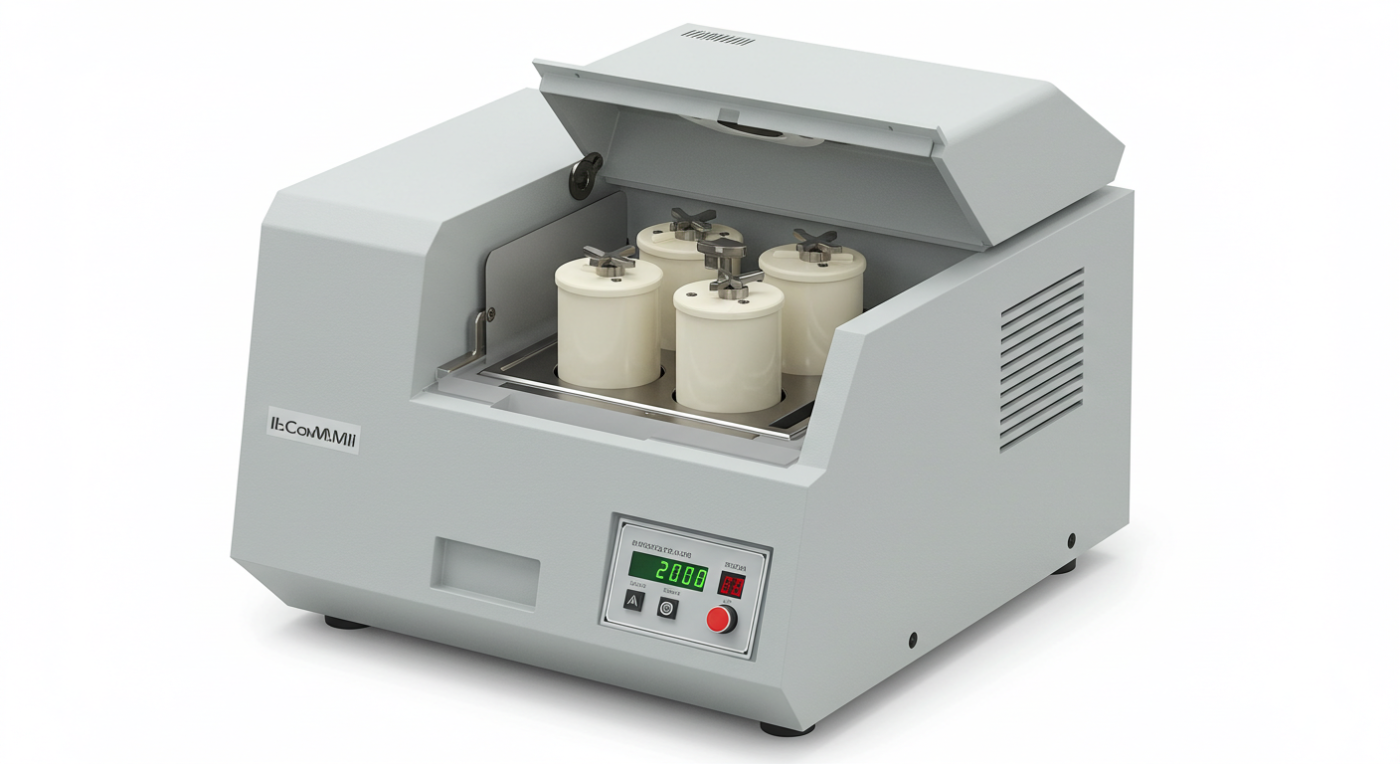
Understanding Planetary Ball Mills
A planetary ball mill is a high-energy milling device that employs centrifugal force to reduce particle size. The mill consists of a rotating support disc on which milling jars are placed. These jars rotate around their own axes while the support disc is rotating around a central axis, creating a planetary motion. This dual rotation leads to extremely high-energy impacts within the milling jar, which effectively grinds and disperses materials.
The intense grinding action of a planetary ball mill makes it suitable for applications requiring fine and ultrafine particle size reduction, such as in nanomaterial synthesis, ceramic processing, and pharmaceutical research. The high-energy impacts also facilitate mechanochemical reactions.
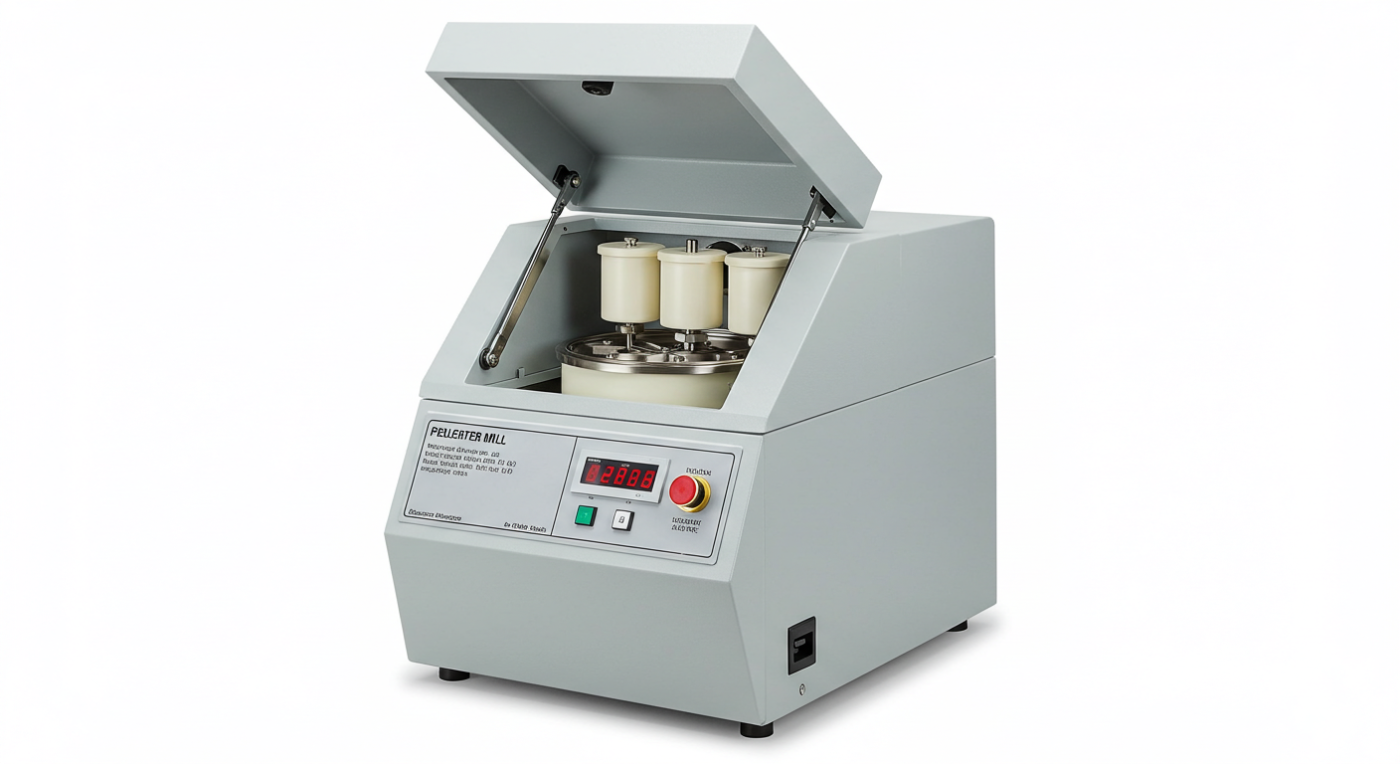
Understanding Roller Jar Mills
In contrast to the intense action of the planetary mill, a roller jar mill, also known as a jar rolling mill, utilizes a simpler mechanism. This mill consists of a set of rotating rollers on which one or more jars are placed. As the rollers rotate, the milling jar turns, causing the grinding media and materials inside to tumble and grind.
The grinding action in a roller jar mill is less intense compared to a planetary ball mill, making it more suitable for applications where gentler milling is required. This is particularly helpful where particle size reduction isn’t the only goal, as this method prevents excessive heat and damage to materials. This can be helpful in applications such as sample preparation, mixing, and grinding of certain materials.
Planetary Ball Mill vs. Roller Jar Mill: Key Differences
While both are used for powder milling, planetary ball mills and roller jar mills differ significantly in several key aspects. Understanding these differences is essential for choosing the right mill for specific applications. Here’s a comparison:
Comparison Table: Planetary Ball Mill vs. Roller Jar Mill
Feature | Planetary Ball Mill | Roller Jar Mill |
---|---|---|
Grinding Mechanism | High-energy impact from dual rotation (planetary motion) | Gentle tumbling action from jar rotation |
Energy Input | High energy, capable of ultrafine particle size reduction | Low energy, suitable for gentle milling |
Particle Size Reduction | Effective for achieving very small particle sizes, including nanoparticles | Primarily used for mixing and general size reduction, though not to the nano level |
Milling Time | Shorter milling times, due to the intense action | Longer milling times, due to the gentle action |
Suitable Materials | Hard, brittle materials, also suitable for mechano-chemical synthesis | Soft, sensitive materials, also for mixing and blending |
Heat Generation | Higher heat generation during operation, often requiring cooling | Lower heat generation, making it suitable for heat-sensitive materials |
Cost | Generally higher purchase price | Generally lower purchase price |
Applications | Nanomaterial synthesis, fine particle size reduction, mechano-chemistry | Mixing, grinding of sensitive materials, sample preparation |
The table above clearly highlights the significant differences between these two methods of milling, helping you to choose the correct mill for your specific application.
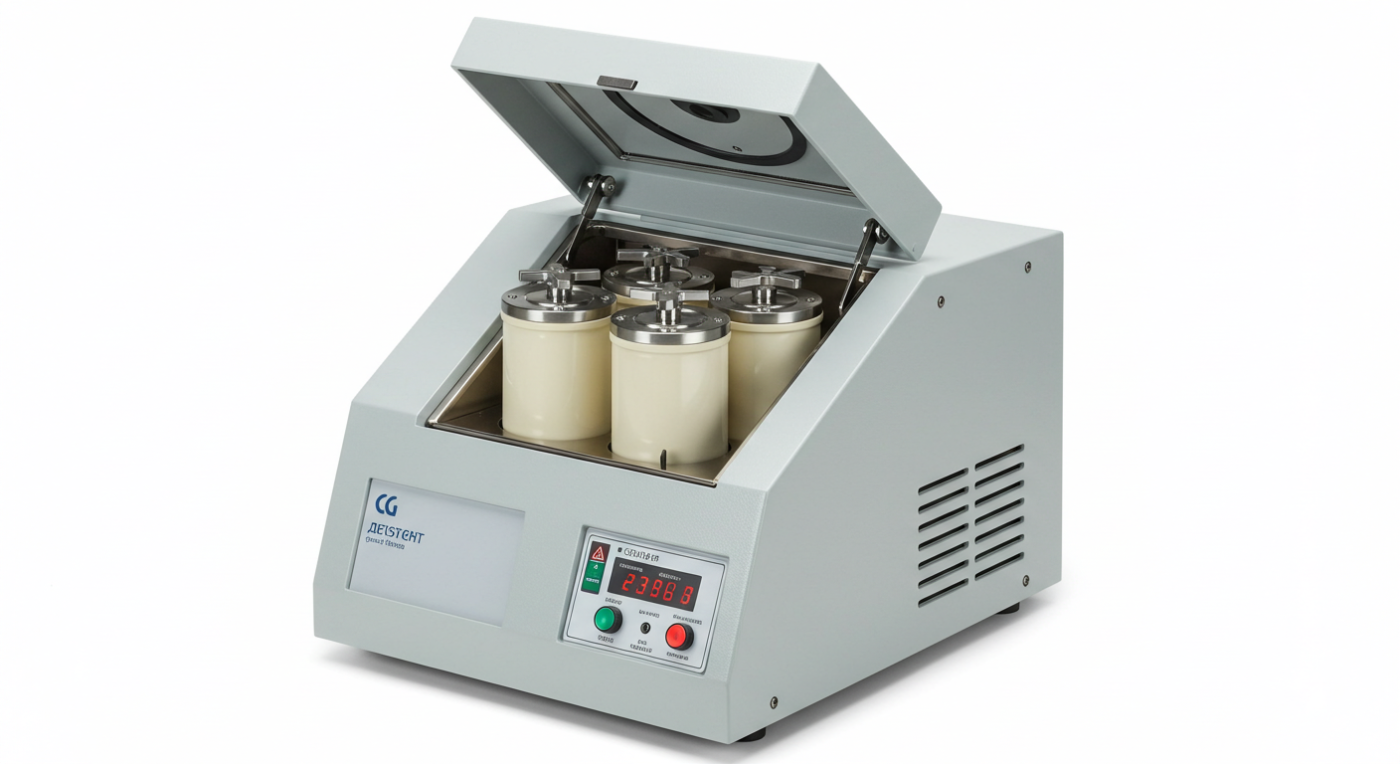
Key Factors in Choosing Milling Media
The choice of milling media is just as important as the type of mill used. The size, shape, material, and density of the milling media directly affect the milling process and the final product. Here are key considerations:
Factors to Consider When Choosing Milling Media:
- Material Compatibility: Choose media materials that are compatible with the materials being milled to prevent contamination and unwanted reactions.
- Size and Shape: Select media with appropriate size and shape for the materials being milled, as they affect the milling efficiency and particle size reduction.
- Density: High-density media leads to more effective grinding due to increased impact forces.
- Hardness: The media should have a hardness equal to or greater than the materials being milled to ensure effective size reduction.
- Wear Resistance: The media should be wear-resistant to prevent contamination and to reduce media replacement costs.
Common materials for milling media include steel, zirconia, alumina, and silicon nitride. Each has specific properties that make them suitable for different applications and material types. The materials, when paired with the proper mill will have a significant impact on the overall process.
The Versatility of Planetary Ball Mills
The planetary ball mill is an exceptionally versatile piece of equipment with wide-ranging applications across various scientific and industrial sectors. Its high-energy grinding action enables it to perform a multitude of tasks with great efficiency.
Key Applications of Planetary Ball Mills:
- Nanomaterial Synthesis: Producing nanoparticles and nanostructured materials for advanced applications.
- Ceramic Processing: Fine grinding and mixing of ceramic materials, enhancing their properties.
- Pharmaceutical Research: Reducing the size of pharmaceutical powders and creating drug delivery systems.
- Mechanical Alloying: Creating new alloys by mixing powders under high-energy conditions.
- Mechano-chemical Reactions: Inducing chemical reactions by mechanical means, often at room temperature.
- Mineral Processing: Fine grinding of ores and minerals for various industrial applications.
Specific Applications of Roller Jar Mills
Roller jar mills, while not as versatile as planetary ball mills in terms of particle size reduction, offer a number of advantages in specific applications:
Specific Applications for Roller Jar Mills:
- Sample Preparation: Grinding and mixing samples for laboratory analysis.
- Mixing and Blending: Creating homogenous mixtures of powders, liquids, or both.
- Gentle Milling of Sensitive Materials: Reducing particle size of sensitive materials without causing excessive heat or damage.
- Homogenization of Materials: Ensuring uniform distribution of particle sizes and components.
- Grinding of Minerals: Suitable for low-impact grinding of ores and minerals.
- Grinding of Ceramics: Effective for smaller batch sizes of brittle ceramics.
The Square Planetary Ball Mill: Enhanced Efficiency
The square planetary ball mill is a variation that aims to enhance the performance and efficiency of the milling process. Unlike traditional cylindrical jar designs, the square jar configuration provides more efficient grinding by optimizing the trajectory of the milling media.
Advantages of Square Planetary Ball Mills:
- Improved Grinding Efficiency: Optimized impact angles due to the square design allow for faster and more effective grinding.
- Enhanced Mixing: The shape of the jars facilitates better mixing and dispersion of the materials.
- Reduced Milling Time: The enhanced milling results in shorter processing times.
- Better Homogenization: The design promotes improved homogeneity within the milling jar.
- Less Media Adhesion: Square jars also result in less media adhesion, so they can easily be cleaned.
Determining Particle Size Reduction Capabilities
When it comes to reducing particle size, the planetary ball mill is more effective for achieving ultrafine particle sizes, including nanoparticles. The high-energy impacts and shear forces produced by this mill allows for significant reductions in particle size in a shorter amount of time. In contrast, the roller jar mill is not as effective for producing ultrafine particles, it’s primary strength is in mixing and homogenization.
The effectiveness of any mill depends on various factors, including the materials being milled, the milling media, and the milling time. A planetary ball mill can typically achieve particle sizes down to the nanometer range (below 100nm), while a roller jar mill is generally used to get particles down to the micron range (1 to 1000μm).
To accurately compare the two methods, you must factor in your specific requirements and the materials involved in your processes. Choosing the correct equipment is essential for achieving your objectives.
Operational Considerations for Planetary and Roller Jar Mills
Operating a planetary ball mill or a roller jar mill efficiently requires attention to a variety of operational considerations. Proper handling and maintenance are essential to achieve optimal results and prevent equipment issues.
Operational Considerations for Planetary Ball Mills:
- Cooling Requirements: High-energy impacts can result in significant heat generation. This usually means that cooling systems are required to maintain the proper temperature and prevent material degradation.
- Jar Loading: Proper loading and sealing of the milling jars will prevent leaks and ensure optimum milling efficiency.
- Speed Selection: The milling speed must be carefully controlled to avoid overheating and optimize grinding results.
- Preventative Maintenance: Regular maintenance schedules are needed to ensure long-term performance and prevent premature wear.
Operational Considerations for Roller Jar Mill
Understanding these operational considerations will ensure the correct milling results and long term performance of both of these milling methods.
Cost Considerations When Choosing a Mill
The cost of the milling equipment is an important factor to consider when making your choice. A planetary ball mill generally has a higher initial cost than a roller jar mill due to its more complex design and high-energy performance. However, the long term costs are impacted by the volume and throughput you are hoping to achieve.
When assessing the overall cost, you must not only consider the purchase price, but also the operational costs (including energy and consumable media), and maintenance expenses. You must also factor in the production capabilities and requirements of the materials you intend to process. This will help you to choose a method that not only fits your budget but is also efficient for the overall needs of the application.
Conclusion
Choosing the right powder milling technology is crucial for achieving the desired results in various scientific and industrial applications. The planetary ball mill, with its high-energy impacts, is well-suited for applications requiring ultrafine particle size reduction, nanomaterial synthesis, and mechanochemical reactions. Conversely, the roller jar mill provides a gentler milling action and is more suited for applications such as sample preparation, mixing, and grinding of heat-sensitive materials.
The proper choice of milling media is also essential in achieving optimal results. Material compatibility, density, shape, and hardness are important factors that can affect overall performance. With the increasing demand for advanced materials, the versatility and efficiency of both planetary ball mills and roller jar mills will ensure their importance in modern industrial and scientific applications.
By carefully considering the requirements of your specific application and understanding the capabilities of both planetary ball mills and roller jar mills, you can select the most suitable equipment for your powder milling needs, resulting in improved performance, enhanced processes, and better final products. The importance of choosing the right milling equipment should not be under-estimated and making an informed decision will greatly improve overall results.