The Fritsch Pulverisette 6 is a highly sophisticated planetary ball mill designed for advanced applications in materials research, mineralogy, chemistry, and other scientific disciplines that require precise and reproducible particle size reduction. This equipment is particularly useful for the preparation of colloidal dispersions, the fine grinding of mineral samples, and the production of nanostructured materials. Below is an overview of the features and capabilities of the Fritsch Pulverisette 6, often referred to as the “Advanced Planetary Ball Milling System.”
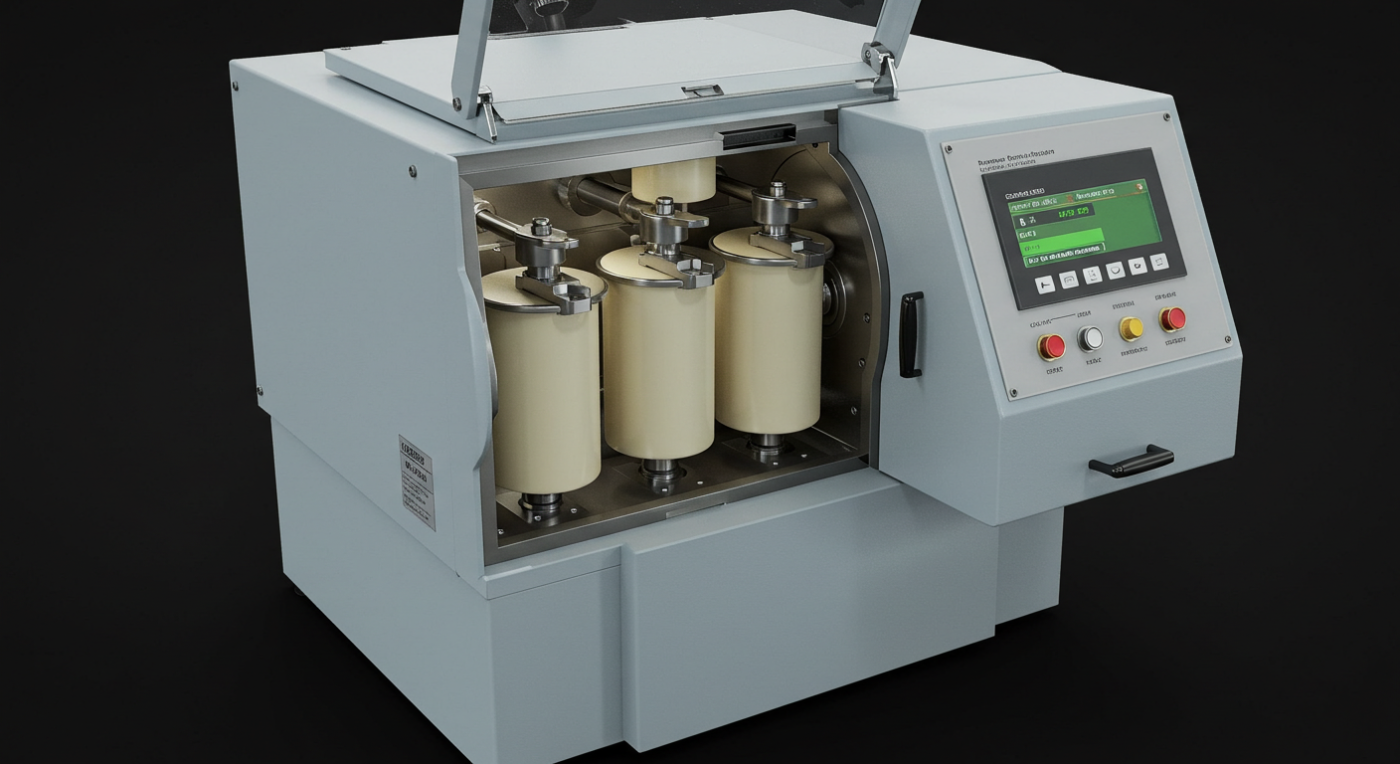
Key Features of the Fritsch Pulverisette 6:
- Planetary Milling Principle:
- The Fritsch Pulverisette 6 operates on the principle of planetary ball milling, where the grinding jars are mounted on a rotating disc (planetary basket) that rotates around its own axis while also rotating around the center axis of the mill.
- This motion ensures high impact and friction, which is essential for achieving fine particle sizes.
- High Efficiency and Speed:
- The mill is capable of achieving particle sizes down to 1 µm with high efficiency.
- The speed of the planetary disc can be adjusted from 100 to 400 rpm, allowing for a wide range of applications.
- Robust Construction:
- The mill is built with high-quality materials to ensure durability and long service life.
- It features a sturdy frame and a vibration-damping base to minimize external vibrations and ensure a stable operation.
- Grinding Jar Options:
- The mill is available with various grinding jar materials and sizes, including stainless steel, agate, zirconia, and tungsten carbide, to accommodate different types of samples and grinding conditions.
- Temperature Control:
- Some models come with an integrated cooling system to maintain a constant temperature during grinding, which is important for heat-sensitive materials.
- Electronic Control and Monitoring:
- The mill is equipped with a microprocessor control unit that allows for easy programming of the grinding process parameters, such as time, speed, and temperature.
- It also features real-time monitoring and can be equipped with a photoelectric particle size sensor for continuous measurement of the particle size distribution.
- Safety Features:
- The mill has safety interlocks to prevent operation in the event of an emergency, such as an overheating situation.
- It is also equipped with a ventilation system to safely exhaust dust and fumes.
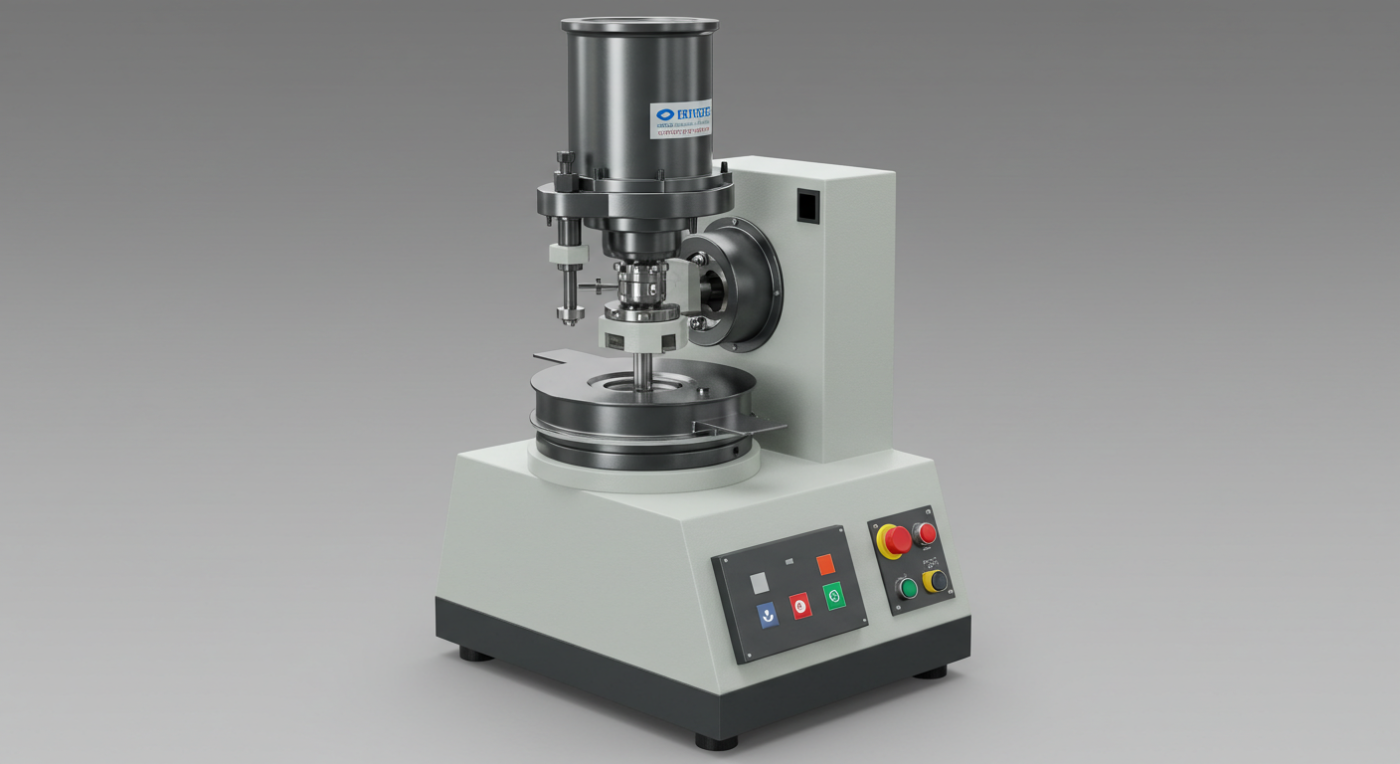
アプリケーション
- Material Preparation:
- The Pulverisette 6 is ideal for the preparation of a wide range of materials, including metals, ceramics, minerals, and polymers.
- Colloidal Dispersions:
- It is particularly useful for the preparation of colloidal dispersions and emulsions with a narrow particle size distribution.
- Nanotechnology:
- The mill is often used in the production of nanostructured materials, where the ability to achieve extremely fine particle sizes is crucial.
- Analytical Chemistry:
- It is also employed in analytical chemistry for the homogenization of samples before analysis.
Usage Steps:
- Loading the Sample:
- Load the grinding jars with the sample and the appropriate grinding media, ensuring that the jars are balanced.
- Programming the Mill:
- Set the desired parameters for speed, time, and temperature on the control unit.
- Starting the Mill:
- Start the mill and monitor the process. Adjust parameters as necessary to achieve the desired particle size.
- Post-Processing:
- After the grinding process is complete, the sample can be collected and analyzed or used in further processing.
The Fritsch Pulverisette 6 represents the cutting edge of planetary ball milling technology, offering researchers and scientists a powerful tool for a wide range of advanced applications in materials science and related fields.
The PM200 is an advanced planetary ball mill that represents cutting-edge technology in the field of material processing. This type of mill is designed for high-efficiency, precise, and reproducible grinding of various materials, including ceramics, metals, minerals, and other brittle or fibrous materials. Here’s an overview of the features and capabilities of the PM200:
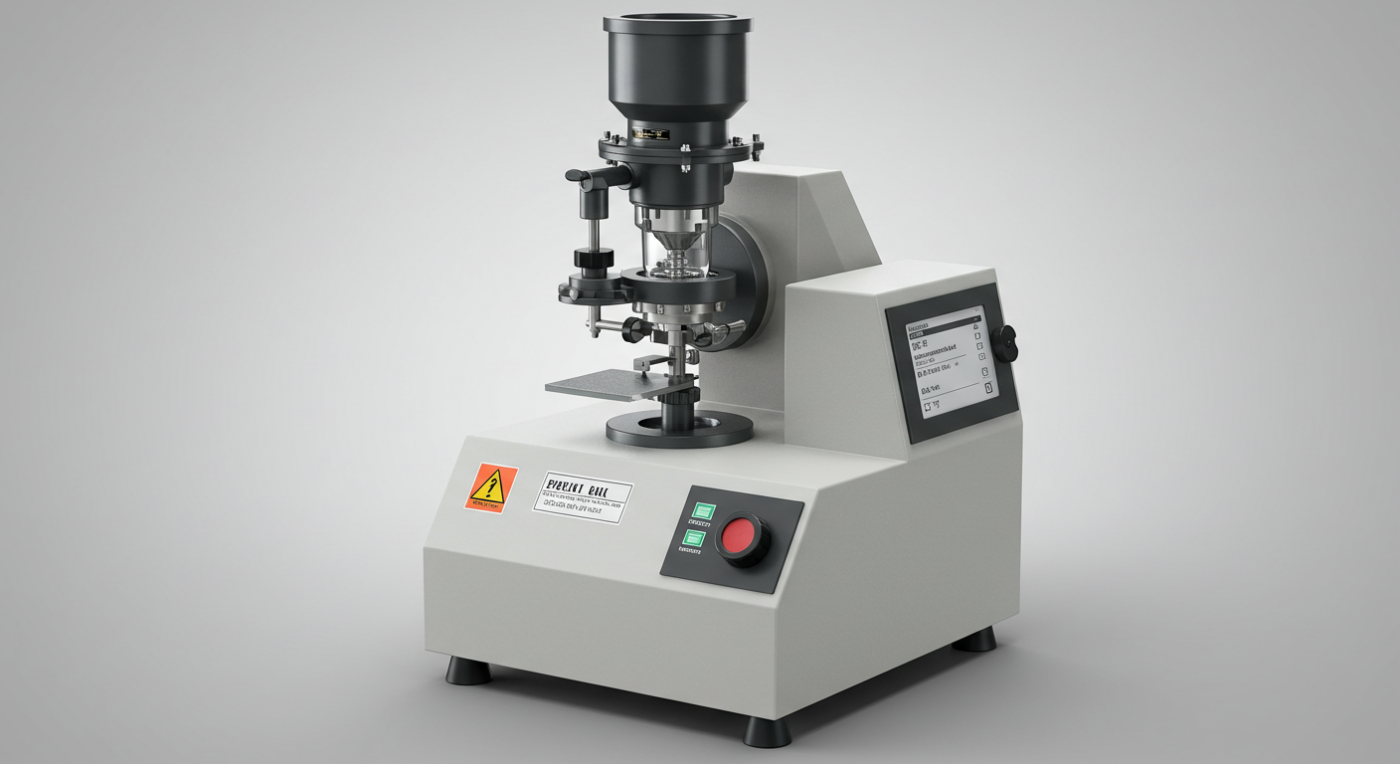
Features of the PM200 Planetary Ball Mill
- Planetary Design: The mill employs a unique planetary motion system, which ensures thorough and efficient grinding of the sample. The grinding balls move in a highly dynamic orbit around the center of the mill, which results in high energy input and rapid material size reduction.
- High Grinding Efficiency: The PM200 is capable of achieving ultra-fine particle sizes, typically in the range of 0.1 to 10 micrometers, depending on the material being ground and the specific operational parameters.
- Wide Range of Applications: This mill is suitable for a wide range of applications, including:
- Material synthesis and development
- Phase analysis
- Battery material processing
- Semiconductor material processing
- Nanomaterial production
- Multiple Grinding Modes: The PM200 offers various grinding modes, such as dry grinding, wet grinding, and cryogenic grinding, allowing researchers to choose the best method for their specific application.
- Automatic Control System: The mill is equipped with an advanced control system that allows for easy operation and adjustment of grinding parameters, including speed, time, and temperature.
- Safety Features: Safety is a top priority in the design of the PM200, with features such as over-temperature protection, emergency stop, and dust collection systems to ensure safe operation.
- High-Quality Materials: The mill is constructed from high-quality materials that are resistant to wear and corrosion, ensuring long-lasting performance and minimal maintenance requirements.
Key Specifications of the PM200
- Max. Sample Capacity: Typically, 50 to 500 ml, depending on the specific model.
- Grinding Balls Material: Hard alloy steel, tungsten carbide, or other materials depending on the application.
- Grinding Speed: Up to 180 rpm for the main shaft, providing high energy input for efficient grinding.
- Control System: Fully automated with touch screen interface for ease of operation.
- Temperature Control: Optional, for cryogenic grinding applications.
- Size: Compact and portable, designed for laboratory use.
Benefits of Using the PM200
- Consistency: The PM200 ensures consistent particle size distribution, which is crucial for reproducible research results.
- Flexibility: The ability to grind a wide range of materials and adjust grinding parameters makes it a versatile tool for various research and industrial applications.
- Efficiency: The high grinding efficiency allows for shorter processing times, which can be particularly beneficial in high-throughput material processing.
The PM200 planetary ball mill is an excellent example of advanced material processing technology, offering researchers and industrial users a powerful tool for achieving their material processing goals. Its combination of efficiency, flexibility, and safety make it a valuable asset in any laboratory or production environment.
Advanced Planetary Ball Milling (APBM) is a highly efficient technique used in materials science for achieving fine particle size reduction and homogenization of materials. The method is particularly useful for the synthesis of nanomaterials, catalyst preparation, and the creation of composite materials. Below is an overview of the methodology for advanced planetary ball milling:
1. Equipment and Materials
- Planetary Ball Mill: This is the main piece of equipment, which consists of a cylindrical jar containing balls (media) and a hollow shaft that rotates in a manner that causes the balls to be thrown against the walls of the jar and each other.
- Balls (Media): These are typically made of materials such as steel, tungsten carbide, or ceramic, depending on the application and the material being milled.
- Jar: Made of materials such as steel, zirconia, or alumina, which must be inert or resistant to the material being milled.
- Material to be Milled: This can be a powder, a compact, or a mixture of materials.
2. Operation Principles
The operation of a planetary ball mill is based on the centrifugal force created by the rotation of the hollow shaft. As the shaft rotates, the balls are lifted and then allowed to fall back into the jar, thereby impacting the material being milled.
3. Advanced Planetary Ball Milling Methodology
a. Selection of Parameters
- Jar Material: The choice of jar material is crucial to prevent contamination and to ensure the jar withstands the chemical and mechanical stresses of the process.
- Ball Material: The choice of ball material depends on the hardness and density of the material to be milled. Harder balls can produce smaller particle sizes but may wear out faster.
- Ball to Powder Ratio: This ratio affects the efficiency of the milling process. A higher ratio can lead to smaller particle sizes but may also result in higher energy consumption.
- Milling Time: The duration of the milling process can vary widely depending on the desired particle size and the material properties. Generally, longer milling times lead to finer particles but can also result in excessive wear or heat generation.
- スピード: The rotational speed of the mill can be adjusted to control the impact force and the degree of material breakdown. Higher speeds can increase the efficiency of the milling process.
b. Preparation of the Mill
- Charging the Mill: The material to be milled is loaded into the jar along with the balls. It’s important to avoid overloading the mill to prevent excessive wear and reduced performance.
- Sealing the Mill: The jar is securely sealed to prevent material loss and to maintain the integrity of the atmosphere within the mill.
- Cooling System: If necessary, a cooling system can be implemented to dissipate heat generated during the milling process.
c. Milling Process
- Initial Milling: Start the mill at a low speed to prevent the balls from jumping out of the jar. Gradually increase the speed to the desired setting.
- Continuous Monitoring: Throughout the process, monitor the temperature and vibration levels of the mill to ensure that it operates within safe parameters.
- Prolonged Milling: Continue the milling process for the duration specified by the protocol. During this time, the balls will impact the material, causing it to break down into smaller particles.
d. Post-Milling
- Stopping the Mill: Once the desired particle size is achieved, stop the mill and allow it to cool down.
- Emptying the Mill: Carefully remove the jar and pour out the milled material. It’s important to handle the material with care to avoid contamination.
4. Optimization and Control
- Optimization Studies: Perform optimization studies to determine the optimal conditions for achieving the desired particle size and material properties.
- Controlled Atmosphere: In some cases, a controlled atmosphere may be necessary to prevent oxidation or other chemical reactions during the milling process.
5. Safety Considerations
- Handling of Hazardous Materials: When working with hazardous materials, appropriate safety measures must be taken, including the use of personal protective equipment (PPE) and proper ventilation.
- Preventing Overheating: Ensure that the mill does not overheat, which can lead to material degradation or a fire.
Advanced Planetary Ball Milling is a powerful tool in materials science, and by carefully controlling the parameters and conditions, researchers can achieve the desired material properties for a wide range of applications.
Advanced planetary ball mill equipment represents the cutting edge of technology in the field of particle size reduction and material processing. These mills are designed for high-intensity mixing, grinding, and blending of materials under controlled conditions. They are widely used in the pharmaceutical, ceramics, chemical, mineral, and food industries. Here’s an overview of the key features and components of such advanced planetary ball mill equipment:
Key Features:
- Planetary Motion: The ball mill features a unique design that allows the balls to rotate around the jar in a planetary motion. This multi-directional movement increases the grinding efficiency significantly compared to traditional ball mills.
- High Intensity Grinding: The high-speed rotation of the jar and the balls ensures intense grinding, which can break down materials to very fine particle sizes.
- Precise Particle Size Distribution: Advanced planetary ball mills can achieve narrow particle size distributions, making them suitable for applications that require precise control over the particle size.
- Versatility: These mills can handle a wide range of materials, from soft to hard, dry to wet, and can be used for both dry and wet grinding processes.
- Easy Operation and Maintenance: Modern planetary ball mills are equipped with user-friendly control panels and are designed for easy operation and maintenance.
- Safety Features: Safety is a priority, with features like emergency stop buttons, safety guards, and explosion-proof motors in certain models.
Components:
- Jars: The jars are the containers where the material and grinding balls are placed. They are typically made of high-quality materials such as stainless steel, alumina, or Teflon.
- Grinding Balls: The balls are the grinding media, and their composition can vary depending on the application. Materials like steel, ceramic, or tungsten carbide are commonly used.
- Drive System: The motor and gears provide the necessary energy to rotate the jars. High-quality, reliable motors are essential for the consistent performance of the mill.
- Control Panel: This includes the user interface, where the operator can set the speed, time, and other parameters. Some advanced models may also have automated controls and data logging capabilities.
- Ventilation System: To prevent the build-up of dust and fumes, most advanced planetary ball mills are equipped with a ventilation system.
- Feeding and Discharging Systems: These systems are designed to allow easy loading and unloading of materials. They can include funnels, chutes, and other accessories to facilitate the process.
- Temperature Control: In certain applications, especially those involving heat-sensitive materials, temperature control is essential. This is achieved through insulation and cooling systems.
Advanced Technologies:
- Variable Speed Control: Some advanced models allow the operator to adjust the speed of the jar, which can be crucial for different materials and processes.
- Programmable Logic Controllers (PLCs): These are used for automated control of the mill’s operation, ensuring consistent and repeatable results.
- Rheological Control: For certain applications, controlling the viscosity of the material can be as important as the particle size. Advanced planetary ball mills can be equipped with systems to control the rheology of the material.
- Sensor Integration: Modern ball mills often include various sensors to monitor the process, such as temperature, pressure, and rotational speed, which can be used to optimize the grinding process.
Advanced planetary ball mill equipment is a significant investment for any lab or manufacturing facility that requires high-quality, precise material processing. The sophistication of these systems allows for the development of novel materials, improved product quality, and enhanced research capabilities.