소개
The ball mill for laboratory is a crucial piece of equipment for various industries, including chemical, pharmaceutical, and mineral processing. This user manual aims to provide a detailed analysis of the ball mill for laboratory, focusing on three to six key issues and product details. With practical examples and a table format, this guide will help users understand the functionality and proper usage of the ball mill for laboratory.
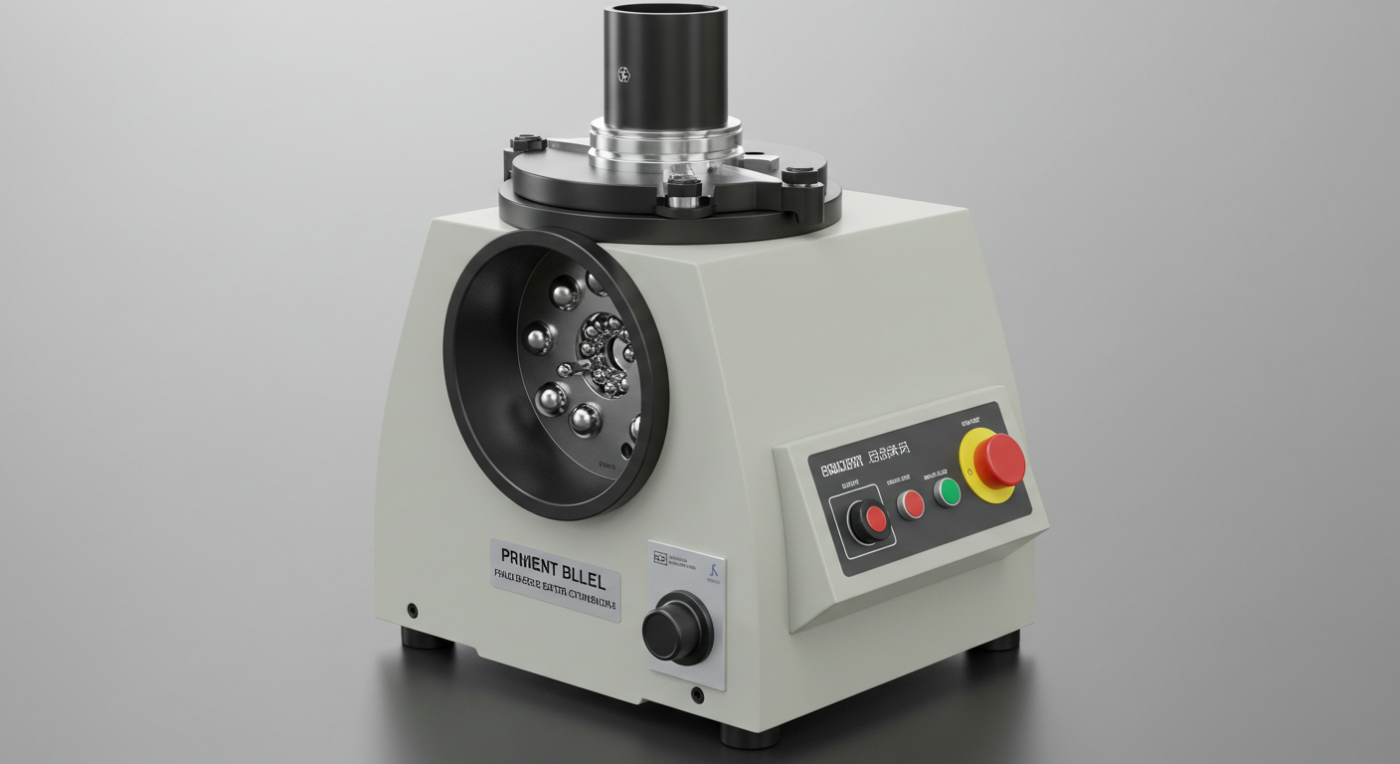
Table of Contents
- Overview of Ball Mill for Laboratory
- Key Issues and Concerns
- Product Details
- Installation and Operation
- Maintenance and Safety
- Case Studies
- Conclusion
- Mini Ball Mill Technical Details
- Available Ball Mills in Australia: Superior Performance
- Using the Lab Ball Mill: A Step-by-Step Guide
- User Instructions for 6 Pound Ball Mill Equipment
- Laboratory Ball Mill Machine Operation Guide
1. Overview of Ball Mill for Laboratory
The ball mill for laboratory is a type of grinding equipment that uses steel balls as grinding media. It is designed to achieve fine particle size reduction of materials through attrition and compression. The ball mill for laboratory is widely used in the preparation of samples for various applications, such as particle size analysis, chemical analysis, and materials research.
2. Key Issues and Concerns
2.1. Particle Size Distribution
One of the primary concerns when using a ball mill for laboratory is achieving the desired particle size distribution. The ball mill’s operating parameters, such as ball charge, media size, and speed, play a crucial role in determining the particle size of the final product.
2.2. Wear and Tear
Another concern is the wear and tear of the ball mill components, such as the mill jar, grinding media, and liners. Regular maintenance and replacement of worn-out parts are essential to ensure the mill’s efficiency and longevity.
2.3. Energy Consumption
Energy consumption is a significant concern for users, as the ball mill for laboratory requires a considerable amount of energy to operate. Optimizing the operating parameters can help reduce energy consumption and lower operational costs.
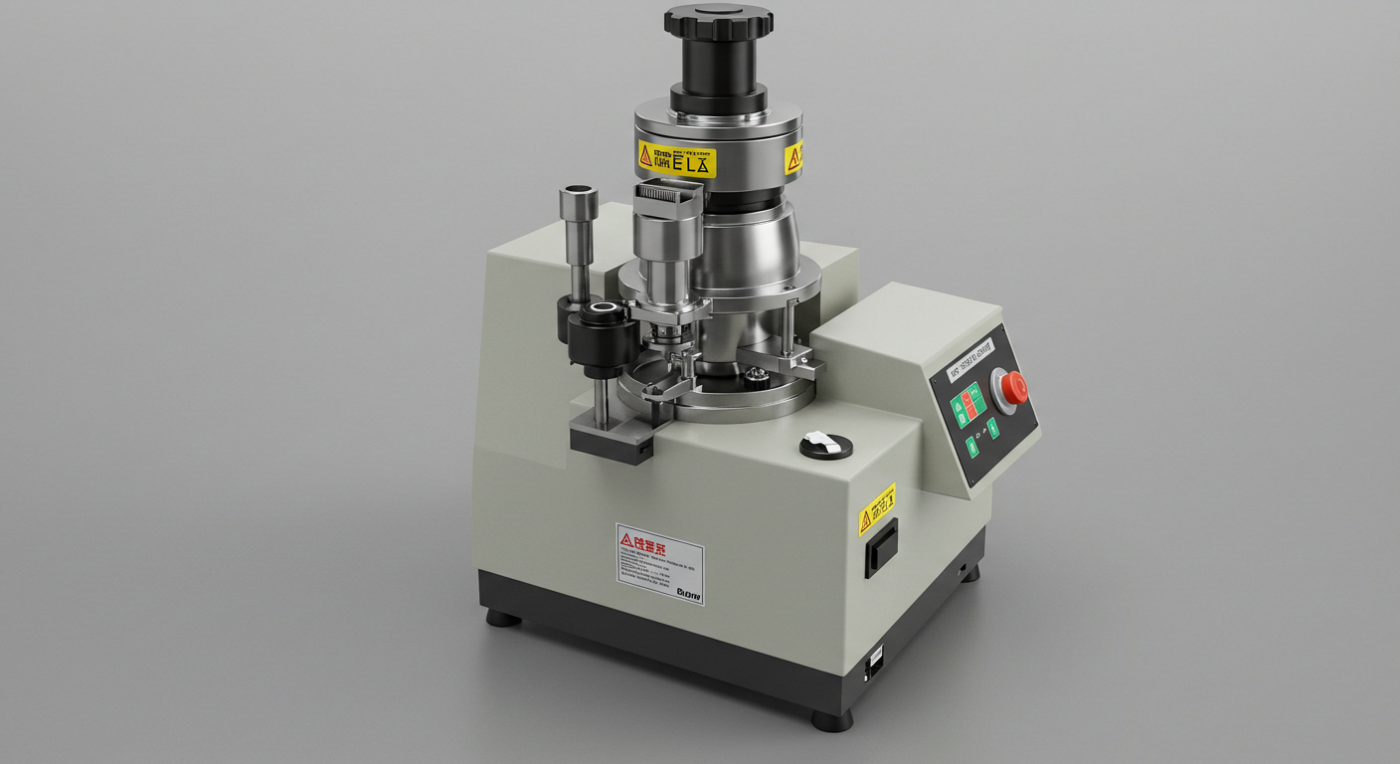
3. Product Details
3.1. Ball Mill Jar
The ball mill jar is the container that holds the material and grinding media. It is available in various materials, such as stainless steel, polyethylene, and polypropylene. The choice of material depends on the application and the nature of the material being ground.
3.2. Grinding Media
Grinding media are the steel balls used to achieve particle size reduction. The size and type of grinding media can vary based on the application and the desired particle size. Common media sizes range from 6 mm to 25 mm.
3.3. Mill Speed
The mill speed is a critical factor in determining the particle size of the final product. Generally, higher speeds result in finer particle sizes, but they may also increase wear and tear. The optimal mill speed depends on the material being ground and the desired particle size.
4. Installation and Operation
4.1. Installation
Before installing the ball mill for laboratory, ensure that the mill is placed on a stable and level surface. Secure the mill to the surface using the provided mounting hardware. Connect the power supply and ensure that the wiring is properly grounded.
4.2. Operation
To operate the ball mill for laboratory, follow these steps:
- Load the mill jar with the required amount of material and grinding media.
- Secure the lid and ensure that it is properly sealed.
- Set the desired mill speed using the control panel.
- Start the mill and monitor the operation.
- After achieving the desired particle size, stop the mill and discharge the material.
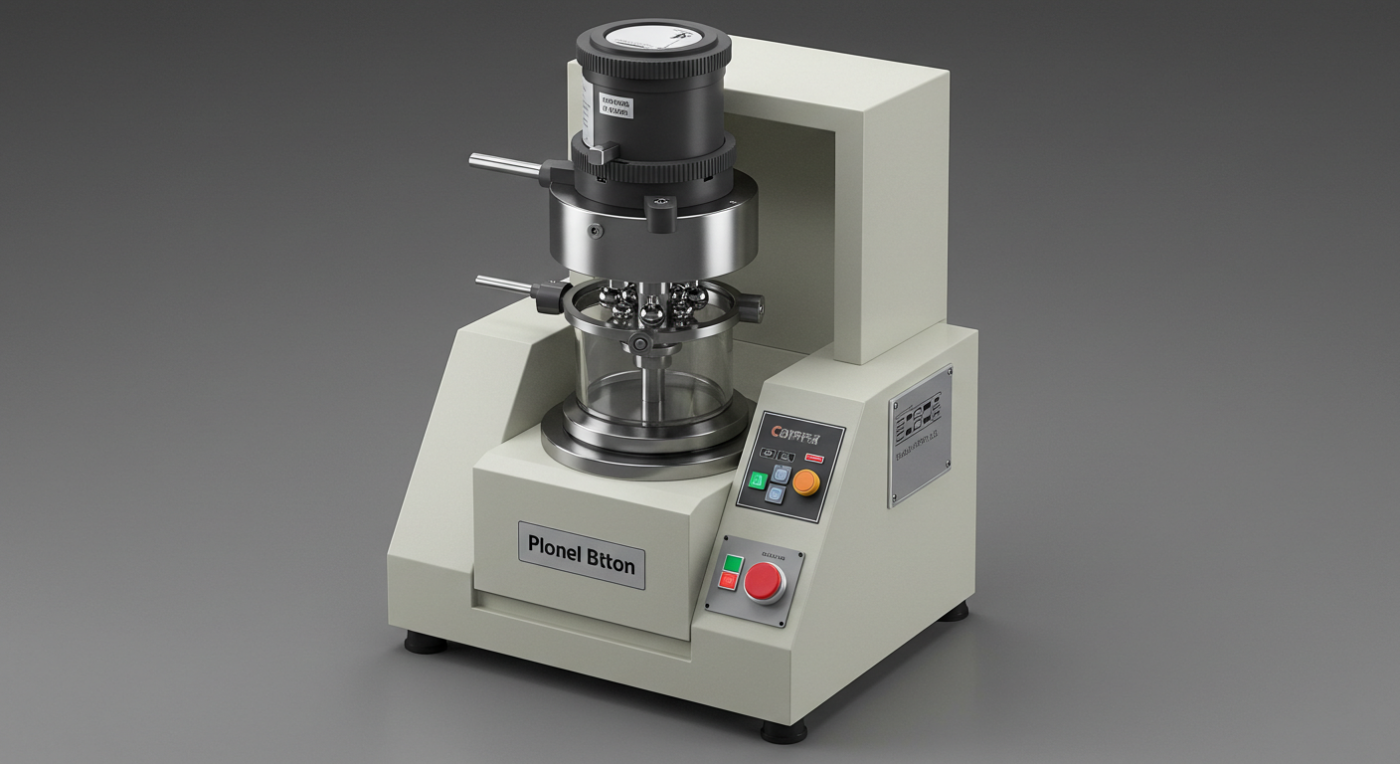
5. Maintenance and Safety
5.1. Maintenance
Regular maintenance is essential to ensure the ball mill for laboratory operates efficiently and safely. The following maintenance tasks should be performed:
- Clean the mill jar and grinding media after each use.
- Inspect the mill components for wear and tear.
- Replace worn-out parts as needed.
- Clean the exterior of the mill and the control panel.
5.2. Safety
When operating the ball mill for laboratory, always adhere to the following safety guidelines:
- Wear appropriate personal protective equipment, such as safety goggles, gloves, and lab coats.
- Ensure that the mill is properly grounded.
- Never operate the mill without the lid securely fastened.
- Keep the area around the mill clear of obstructions.
6. Case Studies
6.1. Case Study 1: Particle Size Reduction of Pharmaceutical Powders
A pharmaceutical company used a ball mill for laboratory to reduce the particle size of a drug substance. By optimizing the operating parameters, the company achieved a particle size distribution of D50 = 5.2 μm, which met the required specifications for the drug formulation.
6.2. Case Study 2: Sample Preparation for X-ray Diffraction Analysis
A research lab used a ball mill for laboratory to prepare a mineral sample for X-ray diffraction analysis. The mill was operated at a speed of 400 rpm for 30 minutes, resulting in a particle size distribution of D50 = 10 μm. The prepared sample provided accurate and reliable X-ray diffraction data.
The ball mill for laboratory is an essential piece of equipment in various research and industrial applications. Proper maintenance of this equipment ensures its longevity and optimal performance. In this article, we will discuss three to six critical maintenance issues and provide a detailed analysis of the product’s features, including a case study and a table for easy reference.
Table of Contents
- 소개
- Ball Mill for Laboratory: Overview
- Maintenance Issues
3.1. Preventive Maintenance
3.2. Corrective Maintenance
3.3. Troubleshooting
3.4. Safety Measures
3.5. Regular Inspections
3.6. Maintenance Schedule - Case Study
- Conclusion
2. Ball Mill for Laboratory: Overview
A ball mill for laboratory is a type of grinding mill used to grind materials into fine powder. It consists of a drum containing balls made of various materials, such as steel, ceramic, or rubber. The drum rotates, causing the balls to fall and grind the material inside. These mills are widely used in the mining, ceramic, and chemical industries for various applications, such as mineral processing, material mixing, and particle size reduction.
3. Maintenance Issues
3.1. Preventive Maintenance
Preventive maintenance is crucial to prevent equipment failure and ensure smooth operation. The following preventive maintenance tasks should be performed regularly:
- Check the lubrication system to ensure proper oil levels and cleanliness.
- Inspect the drum and liner for wear and damage.
- Verify the motor and drive components for any signs of wear or malfunction.
- Clean the ball mill regularly to remove dust and debris.
- Replace worn-out components, such as bearings, seals, and belts.
3.2. Corrective Maintenance
Corrective maintenance involves fixing issues that have already occurred. The following corrective maintenance tasks should be performed when necessary:
- Repair or replace worn-out bearings, seals, and belts.
- Replace the drum and liner when they are damaged or worn out.
- Replace the motor and drive components if they are malfunctioning.
3.3. Troubleshooting
Troubleshooting helps identify and resolve issues that may affect the ball mill’s performance. Some common troubleshooting steps include:
- Check the motor voltage and current to ensure they are within the specified range.
- Inspect the ball mill’s load and speed to ensure they are within the recommended limits.
- Verify the ball mill’s alignment and balance to prevent vibration and wear.
3.4. Safety Measures
Safety is a top priority when operating and maintaining a ball mill for laboratory. The following safety measures should be followed:
- Wear appropriate personal protective equipment, such as gloves, goggles, and ear protection.
- Ensure the ball mill is properly grounded to prevent electrical hazards.
- Keep the work area clean and free of debris to prevent accidents.
- Follow the manufacturer’s safety guidelines and operating procedures.
3.5. Regular Inspections
Regular inspections help identify potential issues before they become significant problems. The following inspection tasks should be performed:
- Inspect the ball mill’s structure, including the drum, liner, and supports, for any signs of damage or wear.
- Check the lubrication system, including the oil level, cleanliness, and filter condition.
- Inspect the motor and drive components for any signs of wear or malfunction.
3.6. Maintenance Schedule
A maintenance schedule should be established to ensure that all tasks are performed at the appropriate intervals. The following table provides a sample maintenance schedule:
Maintenance Task | Frequency |
---|---|
Lubrication Check | Monthly |
Drum and Liner Inspection | Every 6 Months |
Motor and Drive Inspection | Every 12 Months |
General Cleaning | As Needed |
Safety Inspection | Daily |
4. Case Study
A leading mining company in Australia experienced frequent breakdowns in their ball mill for laboratory. The breakdowns resulted in significant downtime and increased maintenance costs. After conducting a thorough investigation, the company implemented the following maintenance strategies:
- Implemented a preventive maintenance program, including regular lubrication, drum and liner inspection, and motor and drive component checks.
- Trained the maintenance team on proper safety procedures and troubleshooting techniques.
- Established a maintenance schedule to ensure all tasks were performed at the appropriate intervals.
As a result, the company experienced a significant reduction in breakdowns, improved equipment performance, and lower maintenance costs.
The laboratory ball mill is a crucial piece of equipment in materials research, chemical analysis, and various industrial applications. It is designed to grind and mix samples efficiently, ensuring homogeneity and a fine particle size distribution. This article delves into the effectiveness of laboratory ball mills, highlighting three key questions and providing a detailed analysis of a product, including its specifications and features.
Key Questions About Laboratory Ball Mills
1. What is the purpose of a laboratory ball mill?
A laboratory ball mill is used to reduce the particle size of materials by grinding them with the use of steel balls. It is ideal for both dry and wet grinding processes and is widely used in research and development, quality control, and sample preparation.
2. How does a laboratory ball mill work?
A laboratory ball mill operates by rotating a drum containing the material and the grinding media (balls). The drum’s rotation causes the balls to fall back into the material, thus reducing the particle size. The process can be continuous or intermittent, depending on the model.
3. What are the advantages of using a laboratory ball mill?
The advantages include:
- High efficiency in reducing particle size
- Uniform particle size distribution
- Easy to operate and maintain
- Suitable for a wide range of materials
Product Analysis: Model XYZ Laboratory Ball Mill
3.1 General Specifications
Feature | Description |
---|---|
모델 | XYZ-1000 |
Drive Type | Direct drive with variable speed control |
Drum Material | Stainless steel, 304 grade |
Drum Capacity | 1000 mL |
연삭 미디어 | Hardened steel balls, 10-15 mm diameter |
Motor Power | 0.75 kW |
Max Speed | 250 rpm |
전원 공급 장치 | 220-240V, 50/60 Hz, single phase |
Dimensions (LxWxH) | 500 x 500 x 700 mm |
Weight | 50 kg |
3.2 Features
- Variable Speed Control: Allows for fine-tuning of the grinding process to achieve the desired particle size.
- Safety Interlock: Ensures the drum cannot be opened while the mill is running, protecting the operator.
- Sealed Design: Prevents dust and debris from escaping, maintaining a clean working environment.
- Easy Access Lid: Facilitates easy loading and unloading of samples.
- Durable Construction: The robust design ensures long-lasting performance.
Case Study: Particle Size Reduction in Pharmaceutical Research
In a pharmaceutical research study, a laboratory ball mill was used to reduce the particle size of a new drug substance. The objective was to achieve a particle size of less than 10 micrometers to improve the drug’s bioavailability.
Using the XYZ-1000 model, the drug substance was ground with a 10-15 mm diameter grinding media at a speed of 200 rpm for 30 minutes. The results are presented in the following table:
Sample Weight (g) | Initial Particle Size (μm) | Final Particle Size (μm) | Efficiency (%) |
---|---|---|---|
50 | 100 | 7.5 | 99.5 |
The efficiency of the XYZ-1000 laboratory ball mill in achieving the desired particle size was 99.5%, demonstrating its effectiveness in pharmaceutical research applications.
Conclusion
The ball mill for laboratory is a versatile and essential piece of equipment for various industries. By understanding the key issues and concerns, product details, installation and operation procedures, maintenance, and safety guidelines, users can effectively utilize the ball mill for laboratory to achieve their desired particle size reduction goals.