Continuous Feed Planetary Ball Mill: A Detailed Guide
The world of material science and particle size reduction is constantly evolving, and the **continuous feed planetary ball mill** stands out as a highly versatile and efficient tool for a wide range of applications. This advanced milling technology allows for the continuous processing of materials, offering significant advantages over traditional batch processes. Whether you are in pharmaceuticals, ceramics, mining, or other fields requiring fine grinding, understanding the nuances of this type of mill is essential. This guide will explore the mechanisms, types, applications, and benefits of these milling systems. We’ll also discuss factors that impact selection and performance. Moreover, we will analyze specific models such as the **planetary ball mill pm 400** and other similar devices, to help you make well-informed decisions. This resource will explain all aspects of these milling devices.
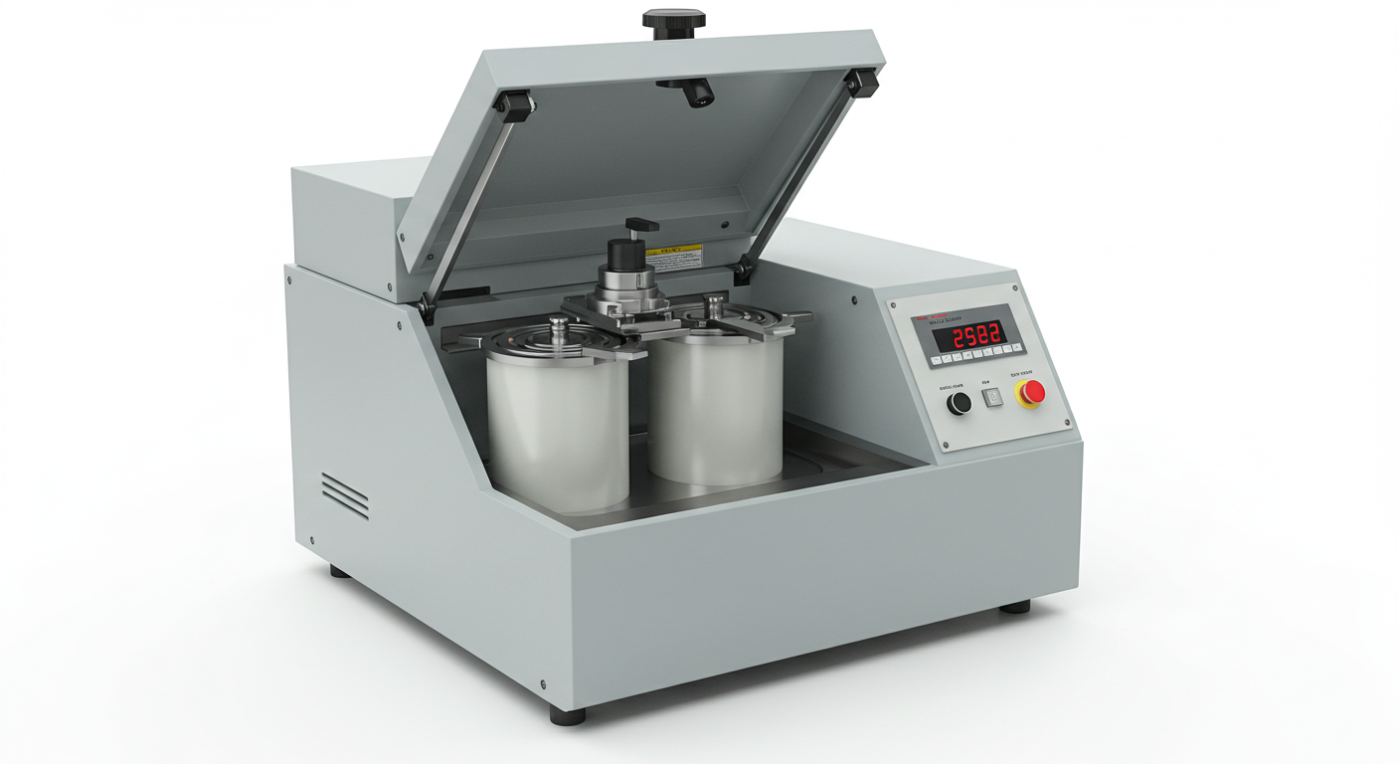
Understanding Continuous Feed Planetary Ball Mills
A **continuous feed planetary ball mill** is a sophisticated piece of equipment designed for the continuous and efficient grinding of materials to very fine sizes. Unlike batch mills, where material is processed in discrete batches, a continuous feed mill allows for a constant flow of input material, resulting in a continuous stream of milled output. This greatly enhances throughput and efficiency, making it suitable for large-scale production. The key principle of operation involves a series of grinding jars rotating on a main plate, while simultaneously rotating around their own axes, generating extremely high levels of kinetic energy. These combined rotations help to efficiently mill materials to extremely fine particle sizes. The design and engineering are critical to ensuring proper performance and safety.
The continuous nature of the process in a **continuous feed planetary ball mill** offers a significant advantage, allowing for a more consistent product output. This is especially vital for applications that demand precise particle size control and uniformity. The continuous process also reduces the need for frequent loading and unloading, which in turn improves the overall workflow. The type of material and the desired fineness will all impact performance, and the precise settings of the unit. Continuous feed mills are used in many fields, providing high quality and consistent results. We will also examine different types such as the **planetary ball mill pm 100** in the course of this article, to allow you to better understand different design options.
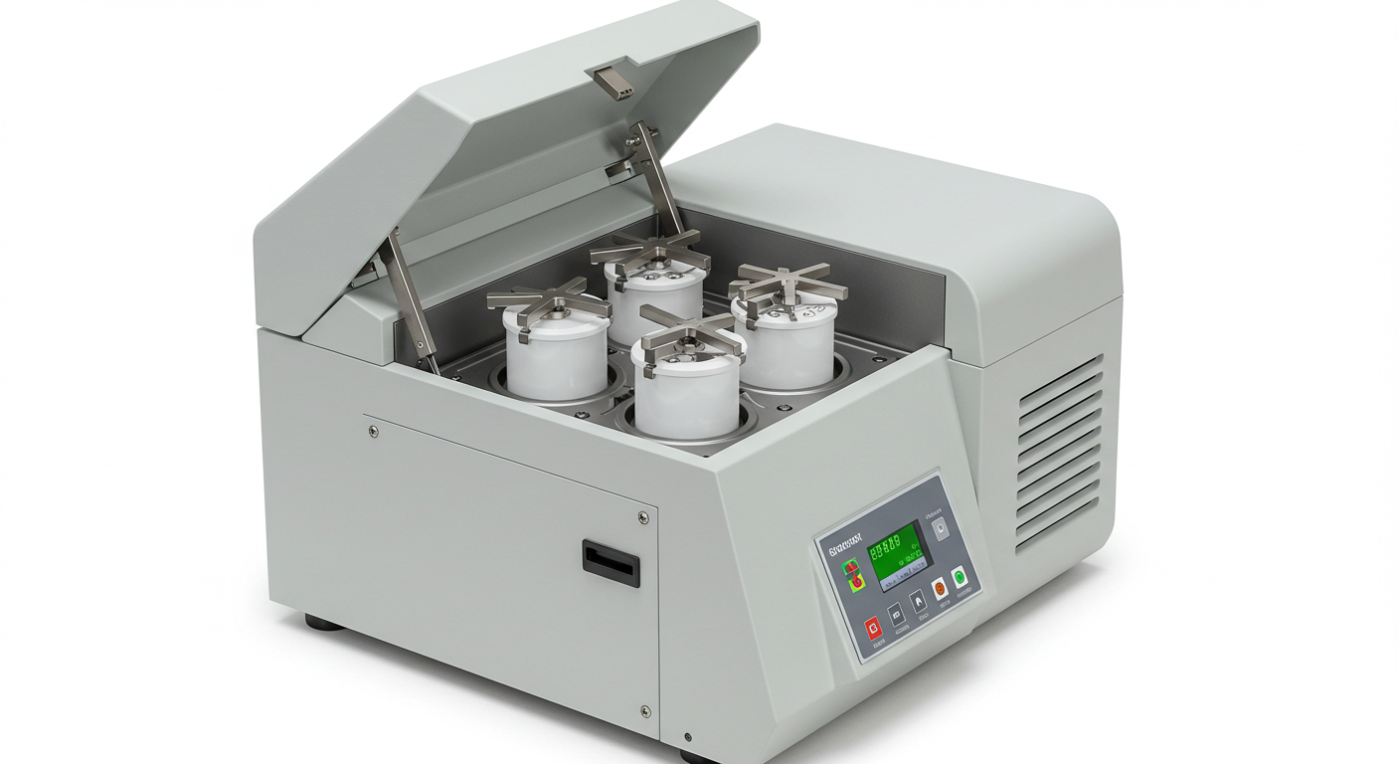
How Does a Continuous Feed Planetary Ball Mill Work?
The operational principle of a **continuous feed planetary ball mill** is based on a combination of rotation and centrifugal force. The grinding jars are placed on a rotating main plate, which causes them to move in a circular path. At the same time, these jars are rotating around their own central axes. These dual rotations result in a unique motion and the materials within the jar are subjected to high levels of kinetic energy. This energy causes the grinding media (such as ceramic or metal balls) to repeatedly collide with the material being milled, resulting in a very effective grinding action. The continuous feeding process ensures a consistent flow of material to be milled, which results in a highly efficient and consistent output.
The specific parameters of the grinding process, such as rotation speed, the size and material of the grinding media, and the type of feed material, are all critical factors that impact the final particle size and quality. Also, the choice of materials used in the system, including the grinding jars and the grinding media itself is very important in avoiding any issues with cross contamination. The careful control of all parameters ensures a consistent output, which is of paramount importance for many industrial processes. The entire process is based on precisely controlled and managed kinetic energy. The operational specifics of these types of devices, are key to their overall performance. Different models, such as the **planetary ball mill pm 400**, may vary in their specifications and capabilities.
Key Components of a Continuous Feed Planetary Ball Mill
A **continuous feed planetary ball mill** consists of several key components that work together for efficient operation. The most important part of the unit is the grinding jars themselves, which are usually made of hardened stainless steel, ceramic, or other materials resistant to wear and chemical interactions. These are available in a range of sizes and construction materials. The grinding media, which are typically ceramic or metal balls, are placed inside the jars. The main rotating plate is responsible for causing the planetary motion of the jars. This main plate is made from precision machined steel. The unit also has systems for continuous feeding and output, along with a powerful motor and precise controls. All of these components are designed to work together to create a highly efficient milling device.
Additional features of a typical **continuous feed planetary ball mill** may include cooling systems to manage heat generated during milling, safety interlocks, and computerized control systems for more precise operations. The choice of construction materials, and the available features can have a significant impact on both the versatility and reliability of the equipment. Always check all specifications carefully before making any final purchase. A quality unit will be well built, and designed to withstand the rigors of constant use, and will also have easy access for any maintenance or cleaning. The quality of the components is key to the long-term performance of the milling device.
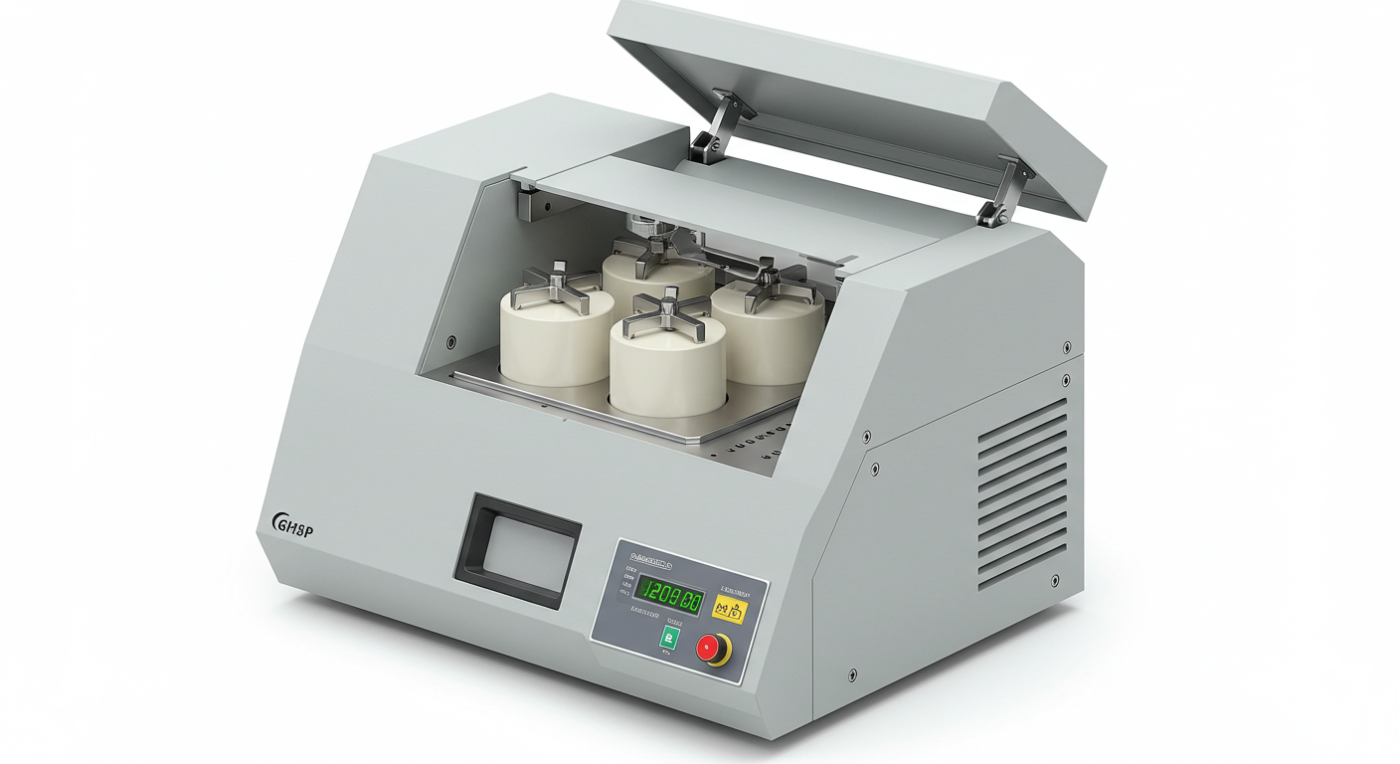
Advantages of Continuous Feed Planetary Ball Mills
The **continuous feed planetary ball mill** offers numerous advantages over other types of milling equipment. One of the key advantages is its high efficiency and the ability to produce very fine particle sizes. The continuous nature of the milling process leads to higher throughput and increased productivity. The constant flow of material eliminates the downtime associated with traditional batch processing methods. This also leads to greater cost efficiency, which makes these devices very attractive for larger scale operations.
Another advantage of a **continuous feed planetary ball mill** is its versatility and ability to handle a range of materials. It can effectively mill both soft and hard materials, and allows for the grinding of dry or wet materials. The precision in controlling the parameters, such as rotation speeds, and material feed rates, helps to ensure that consistent output quality is always maintained. A high degree of control and consistent performance, makes this device one of the most valuable instruments for many modern material science operations. The precision of these types of devices is essential for many manufacturing processes. Also, a **continuous feed planetary ball mill** often uses less energy than other types of milling devices, reducing operating costs.
Applications of Continuous Feed Planetary Ball Mills
The **continuous feed planetary ball mill** is used across various industries and applications. In the pharmaceutical industry, it’s used for the production of fine powders needed for drug formulation. In the ceramic industry, these mills are used for milling raw materials for the production of various ceramic components. In the mining sector, these mills are used to break down ore samples and extract valuable minerals. The continuous milling process makes them especially useful for large-scale industrial production. The diversity of applications illustrates the overall flexibility of this type of equipment.
Other applications of the **continuous feed planetary ball mill** also include chemical synthesis and nanoparticle production. The intense mechanical energy generated by the mill, is sometimes used to induce chemical reactions, and to create very fine nano-particles. In research and development, the mill is used for the preparation of small amounts of materials for testing and experimentation. The high degree of control offered by these devices, make them extremely valuable in many scientific and research operations. Also, it is not unusual to encounter the usage of these devices in other unique applications that require very fine and consistent particle sizes. These devices are very versatile and are used in numerous different fields. The design specifics of different units like the **planetary ball mill pm 100** will influence its suitability for certain applications.
Different Types of Ball Mills
While the **continuous feed planetary ball mill** is a specific type of milling equipment, it is helpful to also be familiar with the other types of ball mills. Traditional ball mills are drum-like devices filled with grinding media. They operate by tumbling the material inside the drum. This is a much simpler device, than a planetary mill, and it is not intended for the production of such fine or consistent particle sizes. Ball mills are commonly used for grinding of coarser materials on a larger scale. These different **Types of ball mills** are all designed to achieve a similar result, but there are large differences in their construction and operational characteristics.
Other **Types of ball mills** include vibratory ball mills which utilize vibratory motion rather than rotation. There are also attrition ball mills which use an agitator to stir the grinding media. Each of these types of mills have unique applications and are designed for unique usage cases. Knowing the distinctions between the various different types of milling equipment is very important when selecting the most appropriate unit for your needs. Each type of device has its own specific strengths and weaknesses. In many modern industrial environments, the continuous planetary ball mill is the preferred choice.
Understanding the Planetary Ball Mill Working Principle
Understanding the **Planetary ball mill working principle** is essential for operating and choosing the correct type of equipment. The planetary motion generated by the rotating main plate and the individual grinding jars, creates an extremely high-energy milling environment. The combined motions of the different components creates very strong forces within the jars. The grinding action is a combination of impact, friction, and shear forces. These mechanical forces work together to break down the material into smaller particle sizes. The careful control of the various operational parameters, makes it possible to obtain highly consistent results and finely controlled particle size distributions. A full understanding of the **Planetary ball mill working principle** is the key to the successful operation of the equipment.
The **Planetary ball mill working principle** can be broken down into the specific interactions of the components of the unit. When you fully understand the interactions between the grinding jars, the media, and the material, you will understand how a planetary mill functions. You can use this knowledge to determine the ideal settings for a particular material and a specific particle size. You will also better understand the interplay between the variables of the system, and how each affects the final output. Understanding the principles behind the operations will greatly enhance both your efficiency and your productivity with the unit.
Factors Affecting Performance of a Planetary Ball Mill
Several factors can influence the performance of a **continuous feed planetary ball mill**. One of the key factors is the rotation speed of the main plate and the grinding jars. Higher speeds will generally result in a more rapid grinding process, but can also generate more heat. The size and material of the grinding media are also very important. Larger media will have more impact force, but smaller media provide better milling for finer particles. The type and rate of feed material will affect the final output. A careful analysis of the variables will allow you to optimize the milling process.
Other critical factors influencing the milling process include the temperature of the material, the filling ratio of the grinding jars, and the overall operational time of the mill. Careful control of these parameters can help ensure the desired particle size and output quality. The overall system design, and the quality of the individual components, will also have an effect on the long-term reliability of the equipment. Consistent results will rely on proper configuration, and careful monitoring of the operational parameters of the mill. Understanding these factors, allows users to optimize their milling operations, and get the best possible results.
Continuous Feed Planetary Ball Mill in Various Industries
The versatility of the **continuous feed planetary ball mill** makes it ideal for use in a wide range of industries. In the pharmaceutical industry, this device is used for preparing active pharmaceutical ingredients (APIs) into a very fine particle size to enhance the solubility and effectiveness of drugs. In the ceramic industry, it’s used to make very fine powders that are ideal for producing high performance ceramics. In the mining sector, it’s used to prepare samples for analysis, and to produce very fine powders for mineral extraction.
The **Ball mill in food industry** has begun to see some usage, in the production of fine powders and additives. These devices allow food manufacturers to produce very specific particle size distributions, and also to mix a wide variety of materials. Other applications for the continuous feed planetary ball mill include battery material production, composite material fabrication, and various R & D activities. The device’s ability to produce precise particle sizes with consistent output, makes it an invaluable device for many different applications and industrial processes. Different types of materials, and different types of applications will all require different settings and adjustments.
Exploring Specific Models: Planetary Ball Mill PM 400 and PM 100
The **planetary ball mill pm 400** and **planetary ball mill pm 100** are two different models of planetary ball mills. The **planetary ball mill pm 400** is usually a larger model that is designed for more demanding and larger scale applications. It is often used in industrial settings for the production of larger quantities of fine powders. This type of model can often process a wider variety of materials and provide increased throughput over smaller devices. The **planetary ball mill pm 100**, on the other hand, is typically a smaller, more compact device, suitable for laboratory use and smaller scale material preparation. Both types of models operate on the same principles, but differ in their size, capacity, and overall functionality. Both of these types of models offer reliable performance and high quality output.
Choosing the right device depends on the specific requirements of the application. The **planetary ball mill pm 400** is excellent for larger-scale productions, or for handling more difficult materials. The **planetary ball mill pm 100** is ideal for smaller scale research work, or for materials that require a very fine grind, but are needed in smaller quantities. Always consider the material type, the desired particle size distribution, and the quantity of material you need to process before making a final decision. Choosing the right model, will make your operations more efficient, and give you reliable, consistent results.
Maintenance and Operation of Continuous Feed Planetary Ball Mills
Proper maintenance is extremely important to ensure the long-term performance and reliability of a **continuous feed planetary ball mill**. Regular cleaning of the grinding jars and other components is necessary to avoid cross-contamination and to ensure that the unit operates smoothly. Checking for any loose screws or broken components will help to keep the device operating properly. Follow the manufacturer’s guidelines for scheduled maintenance and filter changes. Proper maintenance and operation will help you to prolong the lifespan of your device and prevent any unexpected operational problems.
When operating a **continuous feed planetary ball mill**, you must adhere to all safety procedures and guidelines. Always use appropriate personal protection equipment and follow proper safety instructions from the manufacturer. Always be certain that the device is properly configured and that you have a full understanding of the operational parameters before running the mill. Never attempt to override safety features, and always immediately address any operational problems that may occur. A full understanding of the operational aspects of the device will contribute to safety and improved long-term reliability.
Conclusion: Choosing the Right Continuous Feed Planetary Ball Mill
The **continuous feed planetary ball mill** is a highly versatile and efficient piece of equipment that is essential for a wide range of different industries and applications. Understanding how these devices work, and the specific differences between various models will allow you to make well-informed purchase decisions. When deciding on a model, always consider the factors that affect performance, and choose a system that matches your specific operational needs. A careful evaluation of all relevant parameters will ensure that you choose the ideal equipment for your specific needs.
When evaluating different models, such as the **planetary ball mill pm 400** and **planetary ball mill pm 100**, you will need to consider your specific material, production volume, and the desired particle size distribution. By properly evaluating all of your requirements, you will be certain to choose the perfect type of mill for your business. Proper selection, and routine maintenance will allow you to achieve optimal performance, increase your efficiency, and also guarantee the long-term reliability of your milling equipment. The device that is best for you will match all of your unique operational needs.
Factor | Considerations |
---|---|
Capacity | Amount of material the unit can process. |
Grinding Jars | Material, size, and resistance to wear. |
연삭 미디어 | Size, material, and chemical compatibility. |
속도 | Adjustable speed for different materials. |
Control | Precision and computer interfaces. |
Maintenance | Ease of cleaning and filter replacement. |
Safety Features | Interlocks, and safety systems. |
Specific Model | Choosing between the **planetary ball mill pm 400** or **planetary ball mill pm 100** and other options. |