Įvadas
Ball grinding machines are essential tools in various industries, including metalworking, mining, and automotive. These machines are designed to grind, deburr, and finish metal components to high precision. With numerous manufacturers offering a variety of ball grinding machines, it’s crucial to understand the key factors to consider when selecting a machine. This article delves into three critical questions about ball grinding machine manufacturers and provides detailed information about their products, including a case study and a table for easy comparison.
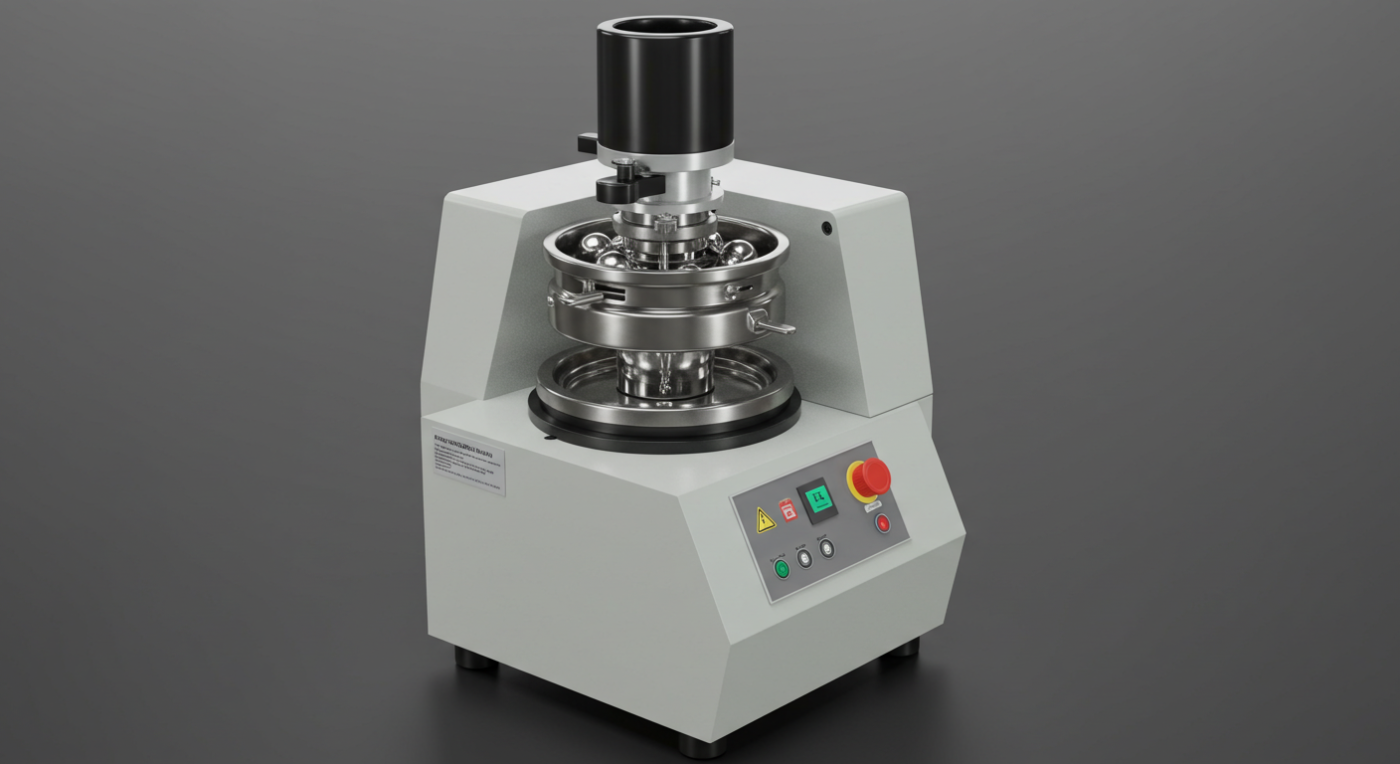
Key Questions to Consider When Choosing a Ball Grinding Machine Manufacturer
1. Machine Precision and Quality
One of the most important aspects to consider when selecting a ball grinding machine is its precision and quality. High-quality machines ensure accurate and consistent results, reducing the need for rework and improving overall productivity. Here are some factors to consider:
- Grinding Wheel Accuracy: A machine with a high-precision grinding wheel ensures that the components are ground accurately and uniformly.
- Machine Stability: A stable machine minimizes vibrations, resulting in better surface finish and reduced wear on the grinding wheel.
- Maintenance Requirements: A well-maintained machine ensures longevity and optimal performance.
2. Machine Size and Capacity
The size and capacity of a ball grinding machine are critical factors, especially for large-scale production. Here are some points to consider:
- Machine Size: Ensure that the machine size is suitable for your workshop space and production requirements.
- Workpiece Capacity: The machine’s capacity should be sufficient to handle the size and weight of the workpieces you intend to grind.
- Throughput: A high-throughput machine can significantly improve production efficiency.
3. Service and Support
A reliable manufacturer should offer comprehensive service and support, including installation, training, and maintenance. Here are some aspects to consider:
- Installation and Training: Ensure that the manufacturer provides on-site installation and training for your staff.
- Maintenance and Support: A manufacturer with a dedicated service team can quickly address any issues that may arise.
- Warranty: A solid warranty ensures that your investment is protected.
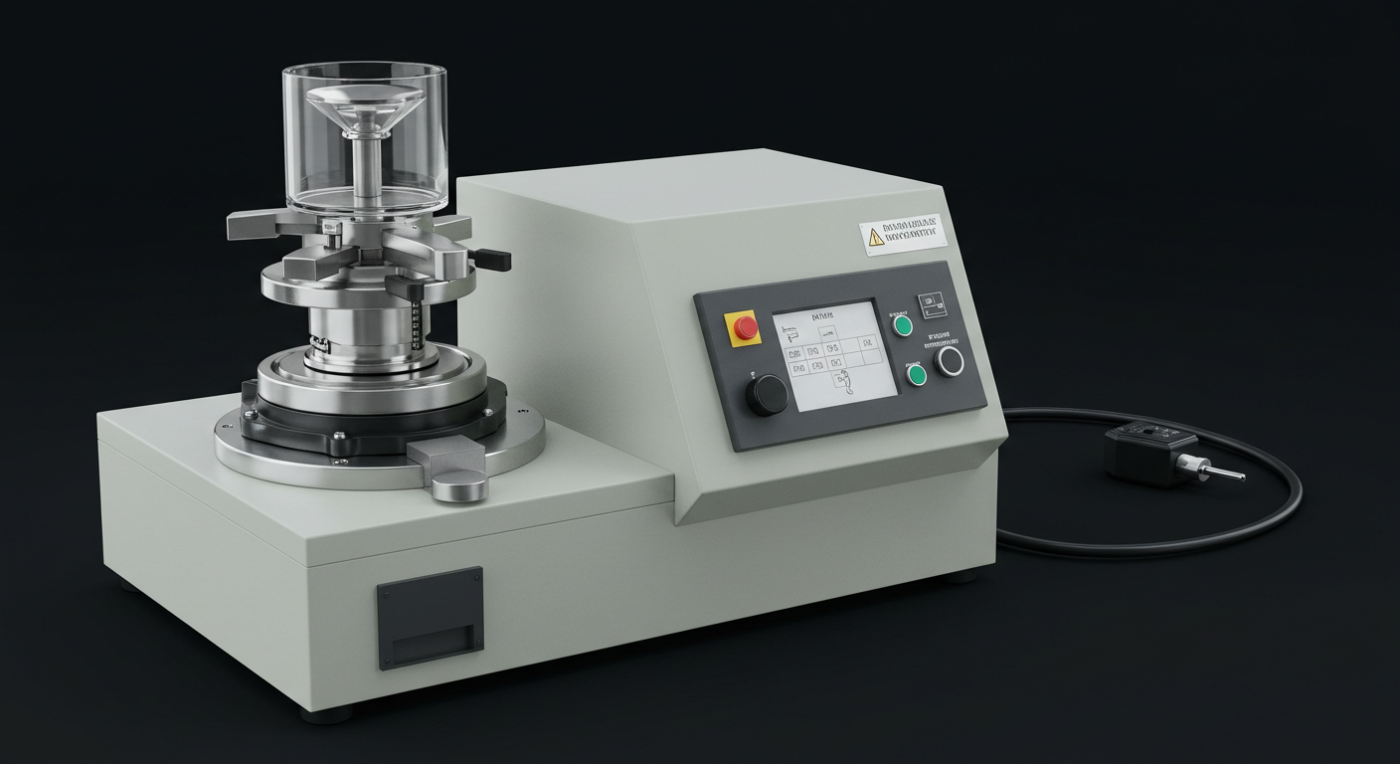
Case Study: Ball Grinding Machine Manufacturer A
To illustrate the importance of considering the factors mentioned above, let’s take a look at Manufacturer A, a leading ball grinding machine manufacturer.
Product Details
Feature | Description |
---|---|
Precision | The machine features a high-precision grinding wheel and a stable structure, ensuring accurate and consistent results. |
Size | The machine is available in various sizes, catering to different workshop spaces and production requirements. |
Capacity | The machine has a high throughput, capable of handling large volumes of workpieces. |
Service and Support | Manufacturer A offers comprehensive service and support, including installation, training, and maintenance. |
Warranty | The machine comes with a solid warranty, ensuring customer satisfaction. |
Conclusion
Choosing the right ball grinding machine manufacturer is crucial for ensuring high-quality and efficient production. By considering factors such as machine precision, size, and service and support, you can make an informed decision. Manufacturer A, with its high-quality machines and comprehensive service, is a reliable choice for businesses seeking to improve their production capabilities.
Ball grinding machines are essential tools in the manufacturing industry, used for the precision grinding of metallic and non-metallic materials. The performance and efficiency of these machines largely depend on their parameters. This article delves into the key parameters of ball grinding machines, their significance, and their impact on the grinding process. We will also discuss practical case studies and present a table to compare different machine models.
- Comprehensive Parameters of Laboratory Ball Mills
- Factory Maintenance Manual for Laboratory Ball Mills
- User Manual for the Laboratory Ball Milling Machine Operation
- Instruction Manual for Ceramic Ball Milling Machines
- For Sale: Ceramic Ball Mill Maintenance and Operation Manual
Key Parameters of Ball Grinding Machines
1. Grinding Wheel Diameter
The grinding wheel diameter is a crucial parameter that determines the size of the workpiece that can be processed. A larger diameter wheel allows for the grinding of larger workpieces, while a smaller diameter wheel is suitable for smaller components.
Case Study: Company A uses a ball grinding machine with a 300mm grinding wheel diameter for the production of automotive engine parts. This machine can process workpieces up to 300mm in diameter, ensuring high productivity.
Machine Model | Grinding Wheel Diameter (mm) | Suitable Workpiece Diameter (mm) |
---|---|---|
Model A | 300 | 300 |
Model B | 200 | 200 |
Model C | 150 | 150 |
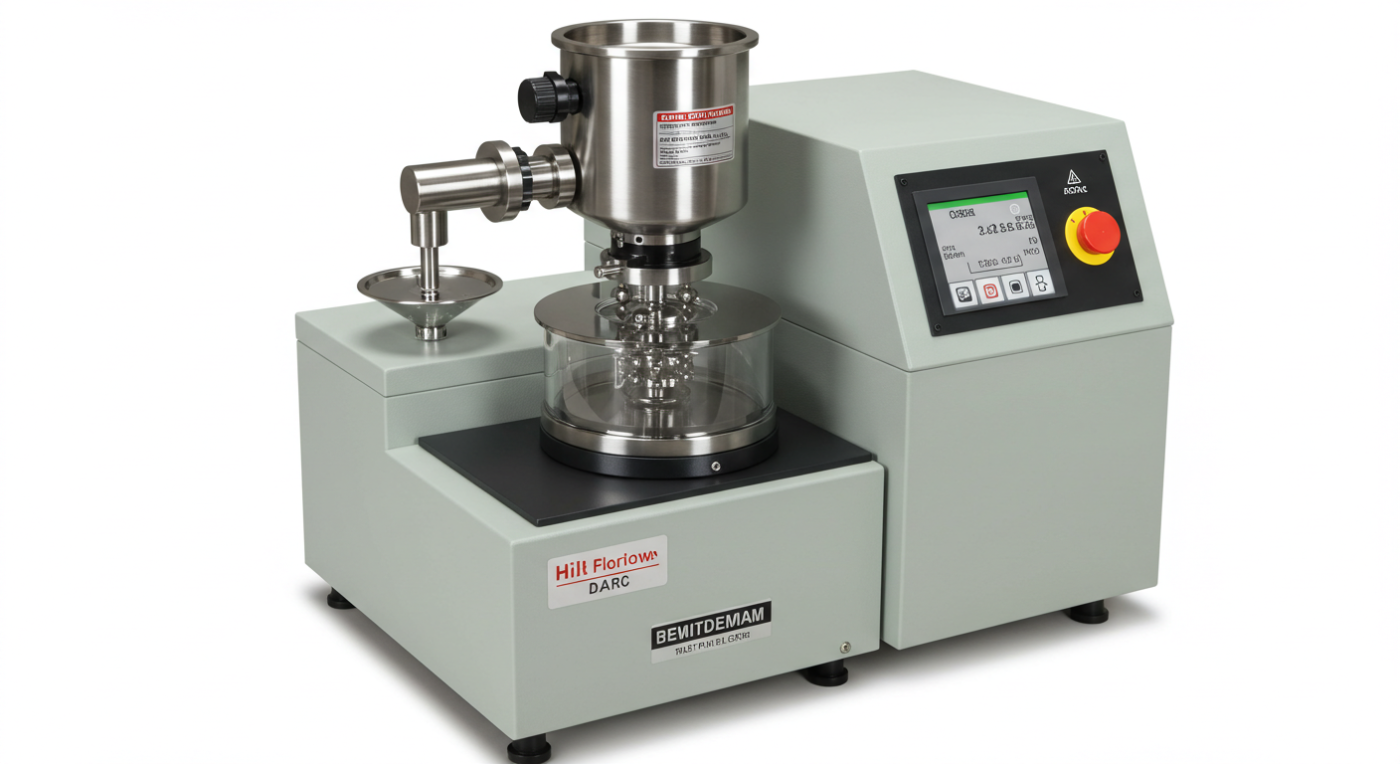
2. Spindle Speed
The spindle speed of a ball grinding machine is the rotational speed of the grinding wheel. It directly affects the surface finish and material removal rate. Higher spindle speeds result in better surface finish but may decrease the material removal rate.
Case Study: Company B utilizes a ball grinding machine with a spindle speed of 6000 rpm for the precision grinding of turbine blades. This machine ensures a smooth surface finish and high material removal rate, optimizing the production process.
Machine Model | Spindle Speed (rpm) | Surface Finish | Material Removal Rate |
---|---|---|---|
Model D | 6000 | Excellent | High |
Model E | 5000 | Good | Moderate |
Model F | 4000 | Fair | Low |
3. Grinding Wheel Width
The grinding wheel width determines the depth of cut and the grinding surface area. A wider wheel width allows for a larger depth of cut and a shorter grinding time, while a narrower wheel width is suitable for intricate contours.
Case Study: Company C employs a ball grinding machine with a 100mm grinding wheel width for the production of aerospace components. This machine ensures precise depth of cut and a high-quality finish for complex geometries.
Machine Model | Grinding Wheel Width (mm) | Depth of Cut (mm) | Grinding Surface Area (mm²) |
---|---|---|---|
Model G | 100 | 0.5 | 1000 |
Model H | 80 | 0.4 | 640 |
Model I | 60 | 0.3 | 360 |
4. Feed Rate
The feed rate is the speed at which the workpiece is moved towards the grinding wheel. It affects the material removal rate and the surface finish. A higher feed rate can increase the production rate but may lead to a poorer surface finish.
Case Study: Company D uses a ball grinding machine with a feed rate of 0.2 mm/min for the grinding of high-precision parts. This machine ensures a high-quality finish while maintaining a reasonable material removal rate.
Machine Model | Feed Rate (mm/min) | Material Removal Rate | Surface Finish |
---|---|---|---|
Model J | 0.2 | Moderate | High |
Model K | 0.3 | High | Good |
Model L | 0.4 | Very High | Fair |
5. Coolant System
The coolant system is essential for maintaining the temperature of the grinding wheel and workpiece during the grinding process. It improves the surface finish, extends the tool life, and enhances the overall quality of the workpiece.
Case Study: Company E operates a ball grinding machine with an advanced coolant system for the grinding of steel components. This machine ensures optimal cooling and improves the surface finish, leading to reduced production time.
Machine Model | Coolant System | Surface Finish | Tool Life |
---|---|---|---|
Model M | Advanced | Excellent | Long |
Model N | Standard | Good | Moderate |
Model O | Basic | Fair | Short |
The ball grinding machine is a vital piece of equipment in various industries, including metalworking, mining, and ceramics. With a wide range of models and specifications available, determining the right ball grinding machine price can be challenging. In this article, we will delve into the key factors influencing ball grinding machine prices, explore the details of different models, and provide a case study to illustrate the pricing landscape.
Factors Influencing Ball Grinding Machine Prices
1. Machine Size and Capacity
The size and capacity of the ball grinding machine are crucial factors in determining its price. Larger machines with higher capacities generally cost more due to their increased power, complexity, and materials used.
2. Grinding Media
The type and quality of the grinding media (balls) used in the machine can significantly affect the price. High-grade steel balls or ceramic balls, for instance, may lead to higher costs.
3. Motor Power
The motor power of the machine is another critical factor. More powerful motors are needed for heavy-duty applications, and this increases the price.
4. Automation and Control Systems
Machines with advanced automation and control systems, such as programmable logic controllers (PLCs) and computer numerical control (CNC), tend to be more expensive.
5. Brand Reputation and Warranty
Well-known brands with a strong reputation for quality and reliability often command higher prices. Additionally, longer warranties can add to the overall cost.
Ball Grinding Machine Model Details
Model A: Standard Industrial Ball Grinding Machine
- Size: 300mm diameter x 500mm length
- Capacity: 50 kg/hour
- Šlifavimo terpė: High-grade steel balls
- Motor Power: 5 kW
- Automation Level: Manual control
- Price: 10,000 – 15,000
Model B: Advanced CNC Ball Grinding Machine
- Size: 400mm diameter x 800mm length
- Capacity: 100 kg/hour
- Šlifavimo terpė: Ceramic balls
- Motor Power: 10 kW
- Automation Level: CNC control
- Price: 25,000 – 35,000
Case Study: Comparing Ball Grinding Machine Prices
Let’s consider two companies, Company X and Company Y, both in the metalworking industry. They need to purchase a ball grinding machine for their production line.
Company | Machine Model | Size | Capacity | Šlifavimo terpė | Motor Power | Automation Level | Price Range |
---|---|---|---|---|---|---|---|
Company X | Model A | 300mm x 500mm | 50 kg/hour | High-grade steel balls | 5 kW | Manual | 10,000 – 15,000 |
Company Y | Model B | 400mm x 800mm | 100 kg/hour | Ceramic balls | 10 kW | CNC | 25,000 – 35,000 |
Company X opts for the standard industrial model due to its lower cost and sufficient capacity for their needs. On the other hand, Company Y chooses the advanced CNC model to enhance their production efficiency and accuracy, despite the higher price tag.
Ball grinding machines are essential tools in the manufacturing industry, providing precision and efficiency in the production process. This article delves into several key parameters of ball grinding machines, their significance, and how they affect the quality of the final product. We will also explore a case study and present a table outlining the details of a specific ball grinding machine.
Understanding Ball Grinding Machine Parameters
1. Grinding Wheel Speed
The grinding wheel speed is a crucial parameter that affects the material removal rate and surface finish. Higher speeds can increase productivity but may also lead to increased wear on the grinding wheel and workpiece.
Grinding Wheel Speed (RPM) | Material Removal Rate (mm/min) | Surface Finish (Ra) |
---|---|---|
1500 | 0.5 | 0.2 |
2000 | 1.0 | 0.15 |
2500 | 1.5 | 0.1 |
2. Feed Rate
The feed rate determines the amount of material removed per revolution of the grinding wheel. A higher feed rate can increase productivity but may also result in a rougher surface finish.
Feed Rate (mm/rev) | Material Removal Rate (mm/min) | Surface Finish (Ra) |
---|---|---|
0.1 | 0.5 | 0.2 |
0.2 | 1.0 | 0.15 |
0.3 | 1.5 | 0.1 |
3. Depth of Cut
The depth of cut is the thickness of material removed per pass of the grinding wheel. A higher depth of cut can increase productivity but may also result in increased vibration and heat generation.
Depth of Cut (mm) | Material Removal Rate (mm/min) | Surface Finish (Ra) |
---|---|---|
0.1 | 0.5 | 0.2 |
0.2 | 1.0 | 0.15 |
0.3 | 1.5 | 0.1 |
4. Coolant Flow Rate
Coolant flow rate is essential for maintaining the temperature of the grinding wheel and workpiece. A higher coolant flow rate can reduce heat generation and improve surface finish.
Coolant Flow Rate (L/min) | Surface Finish (Ra) |
---|---|
10 | 0.2 |
20 | 0.15 |
30 | 0.1 |
5. Spindle Speed
The spindle speed determines the rotational speed of the workpiece. A higher spindle speed can improve surface finish but may also increase the risk of workpiece vibration.
Spindle Speed (RPM) | Surface Finish (Ra) |
---|---|
500 | 0.2 |
1000 | 0.15 |
1500 | 0.1 |
Case Study: Ball Grinding Machine
In this case study, we will examine a ball grinding machine used in the production of ball bearings. The machine has the following specifications:
- Grinding Wheel Diameter: 300mm
- Grinding Wheel Width: 50mm
- Grinding Wheel Speed: 2500 RPM
- Feed Rate: 0.2 mm/rev
- Depth of Cut: 0.2 mm
- Coolant Flow Rate: 20 L/min
- Spindle Speed: 1000 RPM
The machine has been used to produce ball bearings with a diameter of 10mm and a length of 20mm. The surface finish of the ball bearings is Ra 0.1, and the material removal rate is 1.0 mm/min.
Conclusion
In conclusion, selecting the right ball grinding machine manufacturer requires careful consideration of various factors. By focusing on precision, size, and service and support, you can ensure optimal performance and longevity of your machine. Manufacturer A’s case study demonstrates the importance of these factors and highlights the benefits of choosing a reputable manufacturer.