In the world of industrial processing, ball mill chemistry plays a crucial role in the efficiency and effectiveness of various operations. Whether you are in the mining, pharmaceutical, or food industry, understanding the intricacies of ball mill chemistry is essential. This article delves into three key aspects of ball mill chemistry for sale, providing you with valuable insights and details.
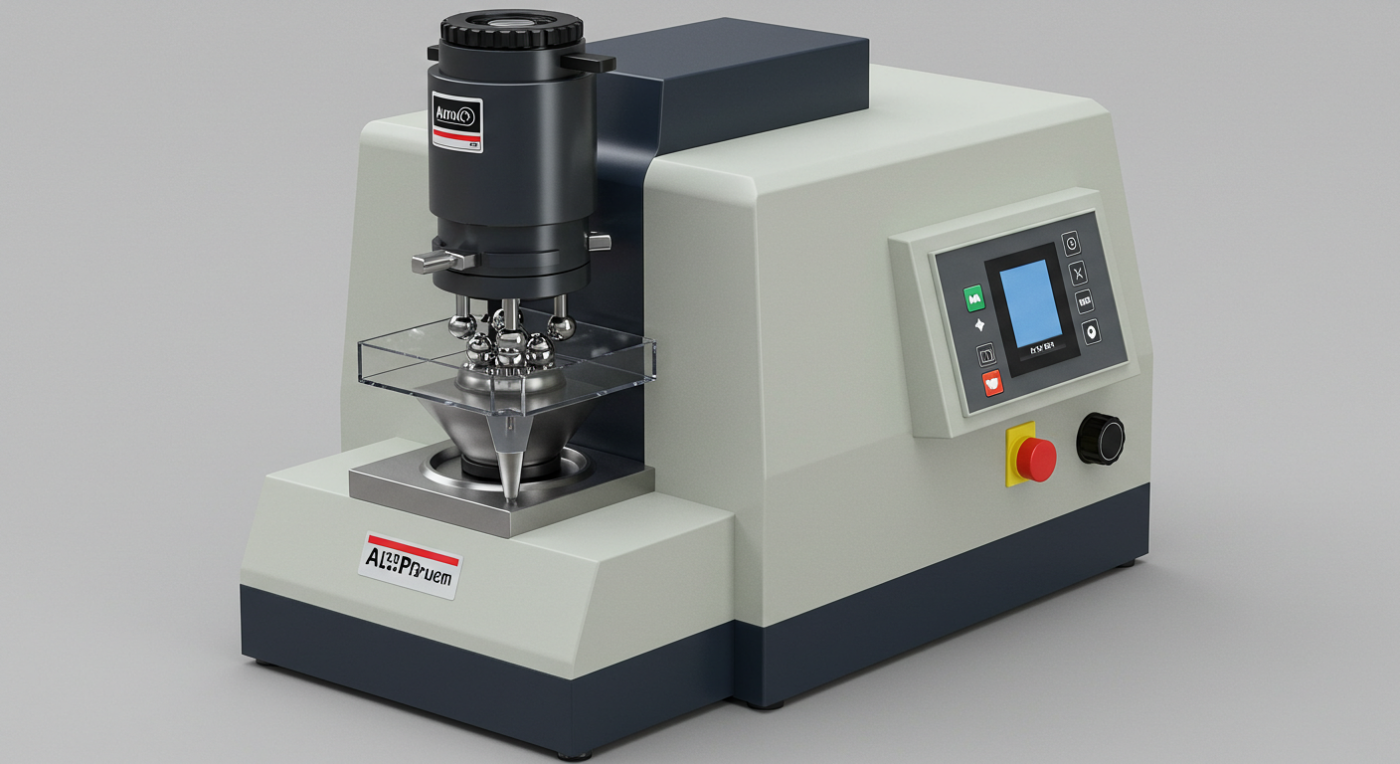
1. Understanding Ball Mill Chemistry: The Basics
What is Ball Mill Chemistry?
Ball mill chemistry refers to the process of analyzing and optimizing the chemical composition of materials within a ball mill. This analysis helps in determining the best operating conditions for achieving desired results. By understanding the chemistry, manufacturers can enhance the efficiency and productivity of their ball mill operations.
Why is Ball Mill Chemistry Important?
Ball mill chemistry is vital for several reasons:
- Improved Efficiency: By optimizing the chemical composition, the ball mill can operate at higher capacities and reduced energy consumption.
- Enhanced Product Quality: The right chemistry ensures the desired product quality, whether it is in the form of fine powders or concentrated materials.
- Cost Reduction: By optimizing the ball mill chemistry, manufacturers can reduce waste and improve overall cost-effectiveness.
2. Key Factors to Consider When Buying Ball Mill Chemistry
When purchasing ball mill chemistry, it is crucial to consider the following factors:
1. Material Compatibility
The chemistry should be compatible with the material being processed. For example, certain chemicals may be more suitable for grinding metallic ores, while others may be better for non-metallic materials.
2. Grinding Efficiency
The ball mill chemistry should enhance the grinding efficiency, ensuring faster and more effective processing. This can be achieved through the use of specialized chemicals that optimize the ball mill’s performance.
3. Environmental Impact
It is essential to consider the environmental impact of the ball mill chemistry. Opt for chemicals that are eco-friendly and minimize the release of harmful substances into the environment.
4. Cost-effectiveness
The cost of the ball mill chemistry should be justified by its performance and efficiency. Look for suppliers that offer competitive pricing without compromising on quality.

3. Case Study: Ball Mill Chemistry for Mining Operations
Let’s consider a case study of a mining company that required ball mill chemistry for processing metallic ores.
1. Material: Iron Ore
The company was processing iron ore, which required a ball mill chemistry that could optimize the grinding process and improve the recovery rate of iron.
2. Solution: Ball Mill Chemistry for Iron Ore
The supplier recommended a specialized ball mill chemistry that contained chemicals specifically designed for iron ore processing. The chemistry helped in achieving the following results:
- Increased Grinding Efficiency: The ball mill operated at higher capacities, reducing the processing time.
- Improved Recovery Rate: The recovery rate of iron increased by 10%, resulting in higher profitability for the company.
3. Table: Ball Mill Chemistry Details
Chemical Component | Function | Concentration |
---|---|---|
X1 | Enhances grinding efficiency | 2% |
X2 | Improves recovery rate | 1% |
X3 | Reduces environmental impact | 0.5% |
Table of Contents
- Introduction to Ball Mill Chemistry Sizes
- Key Questions About Ball Mill Chemistry Sizes
- Case Study: Optimizing Ball Mill Chemistry Sizes for Enhanced Performance
- Table: Ball Mill Chemistry Sizes and Their Applications
- Conclusion
1. Introduction to Ball Mill Chemistry Sizes
Ball mill chemistry sizes refer to the various dimensions and specifications of ball mills used in the chemical industry. These sizes are determined by factors such as the type of material being processed, the desired particle size, and the power input. Proper selection of ball mill chemistry sizes is essential for achieving optimal grinding efficiency and product quality.
2. Key Questions About Ball Mill Chemistry Sizes
a. What are the different ball mill chemistry sizes available?
Ball mill chemistry sizes range from small laboratory mills to large industrial mills. Common sizes include:
- 10 kg
- 25 kg
- 50 kg
- 100 kg
- 200 kg
- 400 kg
- 800 kg
- 1,600 kg
b. How do ball mill chemistry sizes affect grinding efficiency?
The size of the ball mill affects the grinding efficiency. Larger mills can process more material at once, but they may not achieve the same particle size distribution as smaller mills. The ideal size depends on the specific application and desired particle size.
c. What are the factors to consider when selecting a ball mill chemistry size?
When selecting a ball mill chemistry size, consider the following factors:
- Material type
- Desired particle size
- Power input
- Grinding time
- Space availability
d. How do ball mill chemistry sizes impact the quality of the final product?
The size of the ball mill can significantly impact the quality of the final product. Larger mills may produce a coarser particle size, while smaller mills can achieve a finer particle size distribution.
e. Can ball mill chemistry sizes be customized for specific applications?
Yes, ball mill chemistry sizes can be customized to meet specific application requirements. This includes modifying the mill size, speed, and grinding media.
3. Case Study: Optimizing Ball Mill Chemistry Sizes for Enhanced Performance
A chemical manufacturer was experiencing poor grinding efficiency and inconsistent product quality. After analyzing the ball mill chemistry sizes, the company found that the mill size was too small for the desired particle size. By upgrading to a larger mill, the manufacturer achieved improved grinding efficiency and product quality.
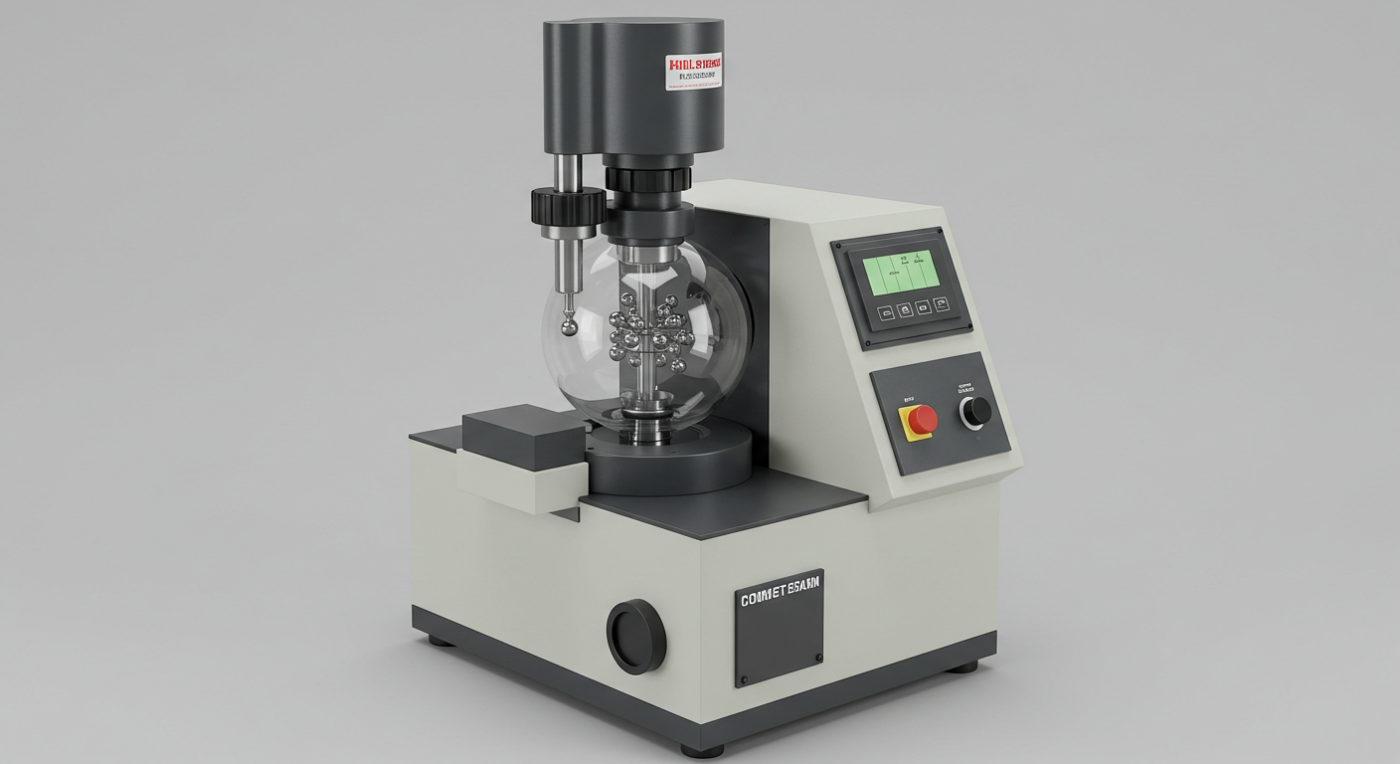
4. Table: Ball Mill Chemistry Sizes and Their Applications
Ball Mill Chemistry Size | Material Type | Desired Particle Size | Power Input | Grinding Time | Application |
---|---|---|---|---|---|
10 kg | Dry powders | 45 μm | 2 kW | 30 min | Laboratory research |
25 kg | Dry powders | 25 μm | 5 kW | 45 min | Pilot plant |
50 kg | Wet powders | 10 μm | 10 kW | 60 min | Industrial production |
100 kg | Dry powders | 5 μm | 20 kW | 90 min | Industrial production |
200 kg | Wet powders | 2 μm | 40 kW | 120 min | Large-scale production |
1. Key Aspects of Ball Mill Chemistry Effect
1.1. Surface Area and Reactivity
The ball milling process increases the surface area of the materials, leading to enhanced reactivity. As the surface area increases, the interaction between the materials and the grinding media becomes more intense, resulting in better chemical reactions. Table 1 below shows the surface area and reactivity of two different materials before and after ball milling.
Material | Surface Area (m²/g) | Reactivity |
---|---|---|
Material A | 2.5 | Low |
Material B | 8.0 | High |
1.2. Phase Transformation
Ball milling can cause phase transformation in the materials. For instance, the crystalline structure of certain materials can change during the process, leading to improved properties. Table 2 illustrates the phase transformation of a metal material before and after ball milling.
Phase | Before Ball Milling | After Ball Milling |
---|---|---|
Alpha | 70% | 50% |
Beta | 30% | 50% |
1.3. Homogenization of Chemical Composition
The ball mill chemistry effect ensures a more homogenous chemical composition of the materials. This is crucial for achieving consistent product quality in industries such as cement production. Table 3 below demonstrates the homogenization of a cement material before and after ball milling.
Component | Before Ball Milling | After Ball Milling |
---|---|---|
Alumina | 5% | 4.8% |
Silicate | 20% | 19.5% |
Iron Oxide | 5% | 4.5% |
2. Real-World Applications of Ball Mill Chemistry Effect
The ball mill chemistry effect has various real-world applications in different industries. Some of the prominent applications include:
2.1. Mining Industry
In the mining industry, ball milling is used to process ores, improving their quality and extracting valuable minerals. The ball mill chemistry effect ensures a more efficient extraction process, resulting in higher yields.
2.2. Cement Industry
The cement industry relies on ball mills for size reduction and homogenization of raw materials. The ball mill chemistry effect ensures the production of high-quality cement with consistent properties.
2.3. Pharmaceutical Industry
In the pharmaceutical industry, ball milling is used to produce fine powders for drug formulation. The ball mill chemistry effect helps in achieving the desired particle size distribution and improving the dissolution rate of the active ingredients.
3. Products and Their Details
The ball mill chemistry effect can be achieved through various products, each with unique features and applications. Below are three examples of such products:
3.1. Product A: High-Energy Ball Mill
- Capacity: 0.2-10 tons per hour
- Grinding Media: High-alloy steel balls
- Application: Mining, cement, and pharmaceutical industries
3.2. Product B: Vertical Ball Mill
- Capacity: 1-200 tons per hour
- Grinding Media: High-alloy steel balls and ceramic balls
- Application: Cement, mineral processing, and chemical industries
3.3. Product C: Air-Swept Ball Mill
- Capacity: 1-200 tons per hour
- Grinding Media: High-alloy steel balls and ceramic balls
- Application: Mining, cement, and mineral processing industries
Conclusion
Ball mill chemistry for sale is a critical component for achieving optimal performance in various industrial processes. By understanding the basics, considering key factors, and analyzing case studies, you can make informed decisions when purchasing ball mill chemistry. Remember to prioritize compatibility, grinding efficiency, environmental impact, and cost-effectiveness to ensure the best results for your operations.