At its core, planetary milling is a type of mechanical milling process that uses centrifugal and inertial forces to induce high-energy impacts on materials, resulting in their size reduction and efficient mixing. The term “planetary” refers to the system’s design, in which multiple grinding containers (also known as milling jars or bowls) are mounted on a rotating support disk, each with its own axis of rotation. This arrangement creates a complex motion akin to planets orbiting a sun, leading to a combination of rotational and centrifugal forces that drive the milling process.
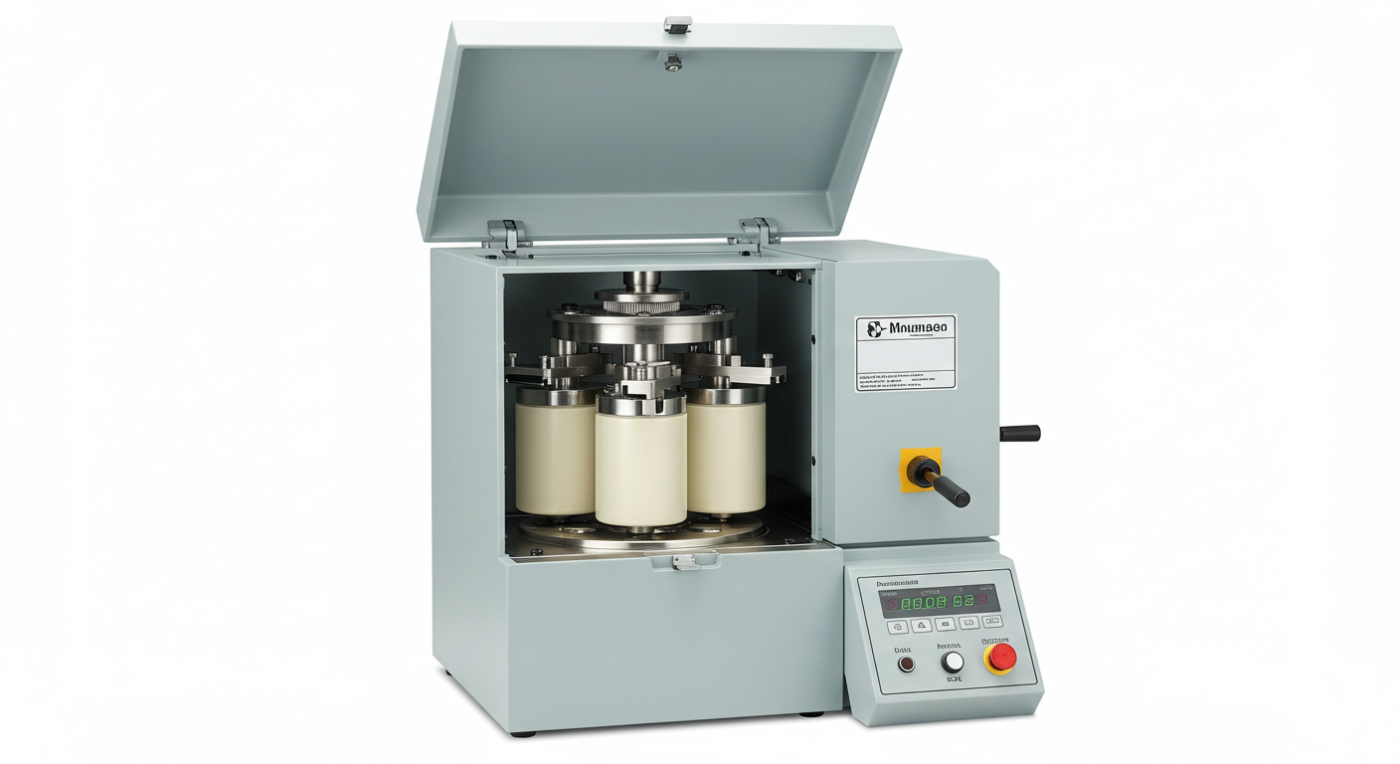
Unlike other milling methods that rely on single-axis rotation or vibration, planetary milling offers a unique and powerful combination of forces, leading to several distinct advantages. Let’s break down the mechanism and understand the underlying physics.
The Mechanics of Planetary Milling: A Deep Dive
The planetary mill typically consists of a central support disk (the “sun” gear) that rotates around its axis. Grinding jars or containers (the “planets”) are mounted on this support disk and rotate around their own axes in the opposite direction of the support disk. This dual rotation generates a complex motion and a range of forces that act upon the milling media (balls, rods, or other grinding elements) and the material being milled.
- Where Can I Buy a Planetary Ball Mill: A Comprehensive Guide
- Understanding Tabletop Ball Mills: An Overview of Important Parameters
- For Sale: Ceramic Ball Mill User Guide
- User Manual for the Lab Ball Mill Equipment
- Micro Ball Mill Specifications
Let’s examine the forces involved:
- Centrifugal Force: As the support disk rotates, each jar experiences a strong centrifugal force that pushes its contents (milling media and the material) outwards. This force is directly proportional to the square of the rotational speed and the distance from the center of rotation.
- Coriolis Force: Due to the combined rotational motion of the support disk and the jars, particles inside the jars experience a Coriolis force. This inertial force acts perpendicular to the direction of motion and influences the path and velocity of the particles within the jars, further enhancing the collision energy.
- Impact Force: The combined action of centrifugal and Coriolis forces causes the milling media to collide with each other and the jar walls with significant energy. These collisions are responsible for fracturing, grinding, and mixing the material.
- Frictional Force: The continuous motion of the material within the grinding jars and the rubbing and sliding action of the milling media also leads to shear forces that contribute to the particle size reduction and mixing.
The precise interplay of these forces within a planetary mill results in a highly efficient and rapid milling process. The combination of high-energy impacts, shearing, and frictional forces is responsible for the effectiveness of planetary milling in reducing particle sizes into the nano-meter range and promoting efficient blending.
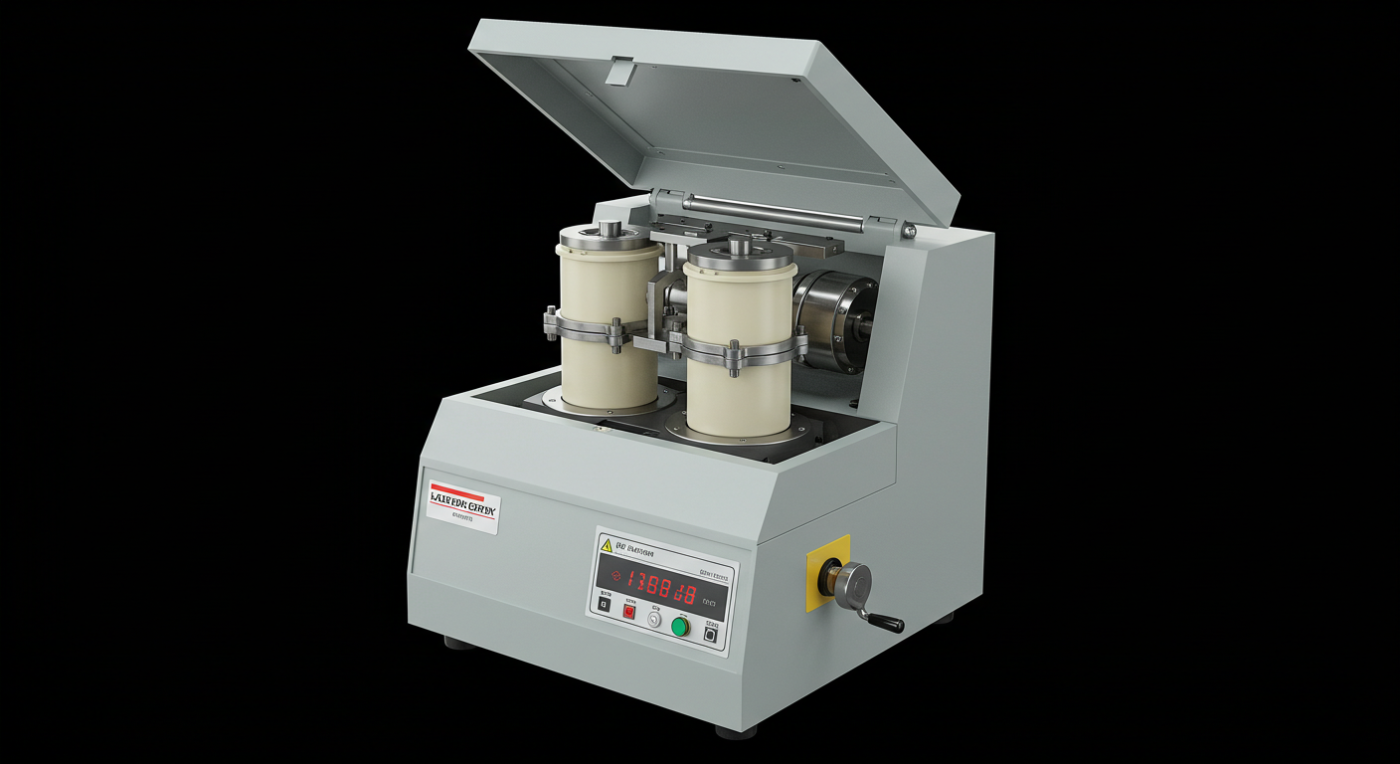
Key Advantages of Planetary Milling
Planetary milling offers several advantages over other milling techniques, making it a popular choice for various applications:
- High-Energy Milling: The combined action of centrifugal and Coriolis forces results in high-energy impacts and efficient milling. The high-energy nature allows the milling process to be performed more quickly, efficiently and effectively compared to other systems.
- Fine Particle Size Reduction: Planetary milling is particularly effective at producing very fine powders and even nanoparticles. It can achieve particle sizes down to the nanometer range in some cases, depending on the material and operating parameters.
- Versatility: This method can be used to mill various materials, including metals, ceramics, polymers, minerals, and composites.
- Efficient Mixing: The intense mixing action of planetary mills allows for excellent blending of materials in addition to size reduction. This makes them very useful for the preparation of homogenous composite powders, nanoparticles and other mixtures.
- Controlled Milling: Planetary mills can be operated under precise control parameters (rotational speeds, milling times, media sizes, etc.), allowing for repeatable and tailored results.
- Wide Range of Applications: Planetary milling is employed in various fields, from materials science and nanotechnology to pharmaceuticals and geology.
- Relatively Small Footprint: Planetary mills are typically compact and have a relatively small footprint, making them suitable for laboratory and small-scale production environments.
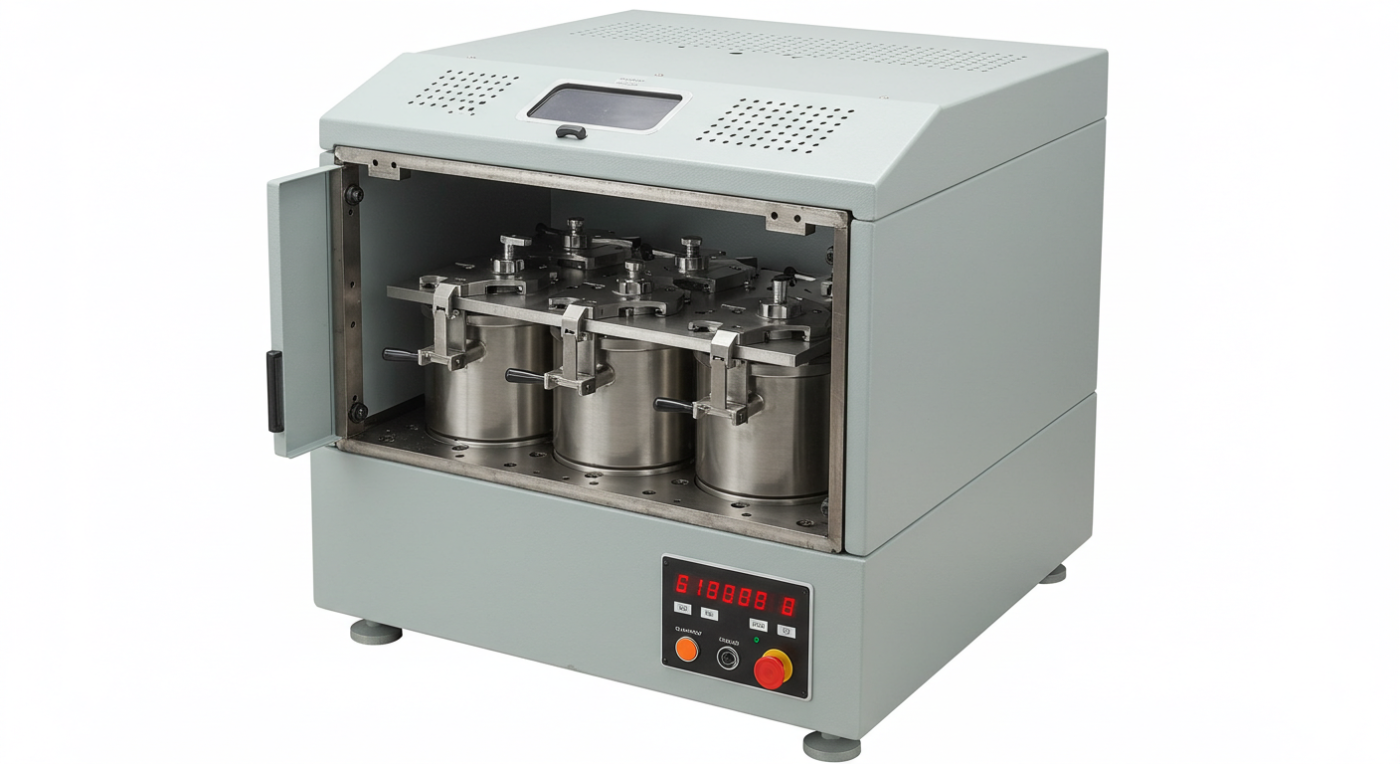
Disadvantages and Limitations of Planetary Milling
While planetary milling offers numerous advantages, it also comes with some limitations:
- Heat Generation: The high-energy milling process can generate a significant amount of heat, which may be problematic for heat-sensitive materials. It can affect the properties of some materials and can even induce phase changes or other unwanted chemical reactions.
- Potential for Contamination: The milling process can cause wear on the grinding jars and milling media, potentially leading to contamination of the milled material, particularly if the wrong material for the media is selected.
- Limited Material Throughput: While planetary mills are effective for fine milling, their processing volume is limited compared to larger industrial mills, making them less suitable for large-scale production.
- Noise and Vibration: The high-speed rotational motion of the planetary mills can create noise and vibration, which must be managed appropriately within the lab or manufacturing area.
- Cost: Planetary mills can be expensive to purchase, and the need for specialized jars and media can also contribute to operating costs.
- Batch Processing: Most planetary mills operate in batch processing mode, which can sometimes be inefficient for continuous production runs.
Different Types of Planetary Mills
Planetary mills come in various configurations, each designed for specific applications and materials. Here’s a breakdown of the most common types:
- High-Energy Ball Mills: These are the most common type of planetary mills. They use milling media (balls) made of materials such as steel, tungsten carbide, zirconia, or agate to perform milling of the materials. These mills are versatile and suitable for both size reduction and mixing of a wide range of materials.
- High-Speed Ball Mills: Designed for even higher milling speeds, these mills are capable of achieving extremely fine particle sizes in relatively short times, with a higher degree of milling energy. They are ideal for producing nano-sized powders, and are generally the most versatile.
- Vibration Planetary Mills: These mills combine the action of planetary rotation with superimposed vibrations. The added vibration can enhance the milling efficiency and promote more uniform milling. This is very useful when processing materials that tend to stick to the milling jars and can also reduce milling times.
- Vertical Planetary Mills: In this configuration, the milling jars are arranged vertically, which can be advantageous for specific materials and applications, especially when processing viscous or heavy materials.
- Horizontal Planetary Mills: In these mills, the milling jars are oriented horizontally, which can be ideal for certain materials and powder blending processes.
- Cryogenic Planetary Mills: These mills are equipped with cooling systems to maintain a low temperature during milling. This is crucial for heat-sensitive materials or for milling materials with low melting points.
- Vacuum Planetary Mills: These mills operate under vacuum to minimize the risk of oxidation or reactions between the milled material and the environment. They are commonly used for the processing of reactive materials.
- Planetary Mixers: While not strictly milling machines, planetary mixers are similar in design and are often used for mixing pastes, slurries, and viscous substances. They typically use paddle-like impellers instead of balls as milling media and often do not have as high an energy impact on the materials.
- Laboratory-Scale Planetary Mills: Small-scale planetary mills are designed for research and development work, typically having smaller milling capacities and precise speed and parameter control. These units are typically designed for small production runs, or for process development.
- Industrial-Scale Planetary Mills: Larger industrial mills are designed for high throughput manufacturing and production. They have greater capacity, power and are more robustly constructed. They may also contain specialized sensors and controls.
Factors Affecting the Performance of Planetary Milling
Several factors influence the effectiveness and efficiency of planetary milling. Understanding and controlling these parameters is essential for achieving the desired results:
- Milling Speed: The speed of rotation of the support disk and jars directly impacts the energy of the milling process. Higher speeds result in greater impact forces and faster milling but can also generate more heat.
- Milling Time: The duration of milling affects the final particle size and mixing uniformity. Longer milling times can lead to finer particles but may also increase the risk of contamination and excessive heat generation.
- Ball Size: The size of the milling media (balls) affects the impact forces and the efficiency of the grinding process. Larger balls exert higher impact forces for coarse grinding, while smaller balls are more effective at achieving finer particle sizes. Using a mix of ball sizes can be more effective for achieving a more consistent size reduction.
- Ball Material: The material of the milling media must be compatible with the material being milled. For example, stainless steel balls are useful for general-purpose milling, whereas zirconia balls are useful for applications where the introduction of iron impurities must be avoided. Some materials are also more wear resistant than others, which means a lower chance of cross contamination and longer lifespans.
- Ball-to-Powder Ratio: The ratio of milling media to material being milled can affect the milling efficiency. An optimal ratio ensures adequate energy transfer to the powder without causing excessive wear or agglomeration. This ratio is usually based on a volume, where the volume of media is between 20 to 50% of the volume of the milling jar.
- Milling Atmosphere: Milling under an inert gas or vacuum can prevent oxidation and reactions with the environment, especially with highly reactive materials.
- Milling Jar Material: The material of the milling jar must be compatible with the materials being milled and should be able to withstand the mechanical forces. The common materials are hardened steel, stainless steel, hardened zirconia, or silicon nitride.
- Milling Jar Volume: The volume of the milling jar should match the amount of material that is being processed. Overfilling or underfilling can impact the effectiveness of the milling process.
- Type of Mill: The type of planetary mill used will affect the amount of energy that is applied to the material. Some specialized mills (for example, high-speed planetary mills) will be able to produce finer material faster.
- Loading and Unloading: The efficiency of the milling process depends on the method used to load and unload material. The milling jars need to be cleaned thoroughly after each milling process to prevent cross contamination.
Applications of Planetary Milling Across Various Industries
Planetary milling is widely used in various industries due to its versatility, efficiency, and ability to produce fine powders and homogeneous mixtures. Some key applications include:
- Materials Science and Nanotechnology:
- Synthesis of nanoparticles, nanocrystals, and nanocomposites.
- Preparation of high-performance ceramics and metal alloys.
- Mechanical alloying and formation of amorphous materials.
- Surface modification of materials.
- Pharmaceuticals:
- Micronization of drug substances to improve bioavailability.
- Preparation of solid dispersions and co-crystals.
- Mixing of active pharmaceutical ingredients (APIs) and excipients.
- Ceramics:
- Preparation of ceramic powders for sintering.
- Homogenization of ceramic compositions.
- Grinding of ceramics into fine powders.
- Geology and Mineralogy:
- Sample preparation for geological analysis.
- Grinding of mineral samples.
- Preparation of fine powder for x-ray diffraction analysis.
- Chemical and Catalyst Production:
- Grinding and activation of catalysts.
- Preparation of fine powders for chemical synthesis.
- Mixing of chemical precursors and reagents.
- Cosmetics and Pigments:
- Grinding of pigments to desired particle sizes.
- Mixing and blending of cosmetic ingredients.
- Preparation of powders for various cosmetic applications.
- Food and Agriculture:
- Grinding of grains, spices, and herbs.
- Mixing of food products and additives.
- Preparation of food powders.
- Battery Technology:
- Preparation of electrode materials for batteries.
- Mixing of battery components.
- Formation of high-performance battery composites.
- Research and Development:
- Material testing and analysis.
- Process development and optimization.
- Preparation of sample materials.
The Future of Planetary Milling
The field of planetary milling is continuously evolving with new technological advancements that seek to improve efficiency, versatility, and control. Some promising areas of future development include:
- Smart Milling Systems: Integration of advanced sensors and control systems to monitor and optimize milling processes in real time.
- Advanced Jar Materials: Development of new jar materials with improved wear resistance and inertness to minimize contamination and improve product purity.
- Continuous Milling Processes: Advancement from batch processing towards continuous planetary milling methods to improve efficiency and throughput.
- Integration with AI and Machine Learning: Using artificial intelligence to predict the results of milling parameters and to automatically optimize milling processes for better results.
- Cryo-Milling Advancements: Improved cryo-milling systems will allow processing for an even wider range of temperature-sensitive materials.
Conclusion
Planetary milling is a powerful and versatile technique that is essential for modern materials processing. Its ability to produce extremely fine powders, create homogeneous mixtures, and enable controlled particle size reduction makes it a cornerstone in various industrial and research fields. By understanding the mechanics, advantages, disadvantages, types, and influencing factors of planetary milling, you can make more informed decisions about its application and optimize milling processes for desired outcomes. With ongoing research and technological advancements, planetary milling will continue to play a vital role in materials science, nanotechnology, and a variety of other industries. Whether it’s for research, small scale production or for larger manufacturing runs, planetary milling is very useful and necessary technique.