Ball grinder machines are essential tools in various industries, from metalworking to ceramics. To ensure safe and efficient operation, it is crucial to have a comprehensive user manual. This article delves into the key aspects of a across international ball mill user manual, addressing three to six pertinent questions and providing a detailed analysis of the product’s features and specifications. We will also include a case study and a table for easy reference.
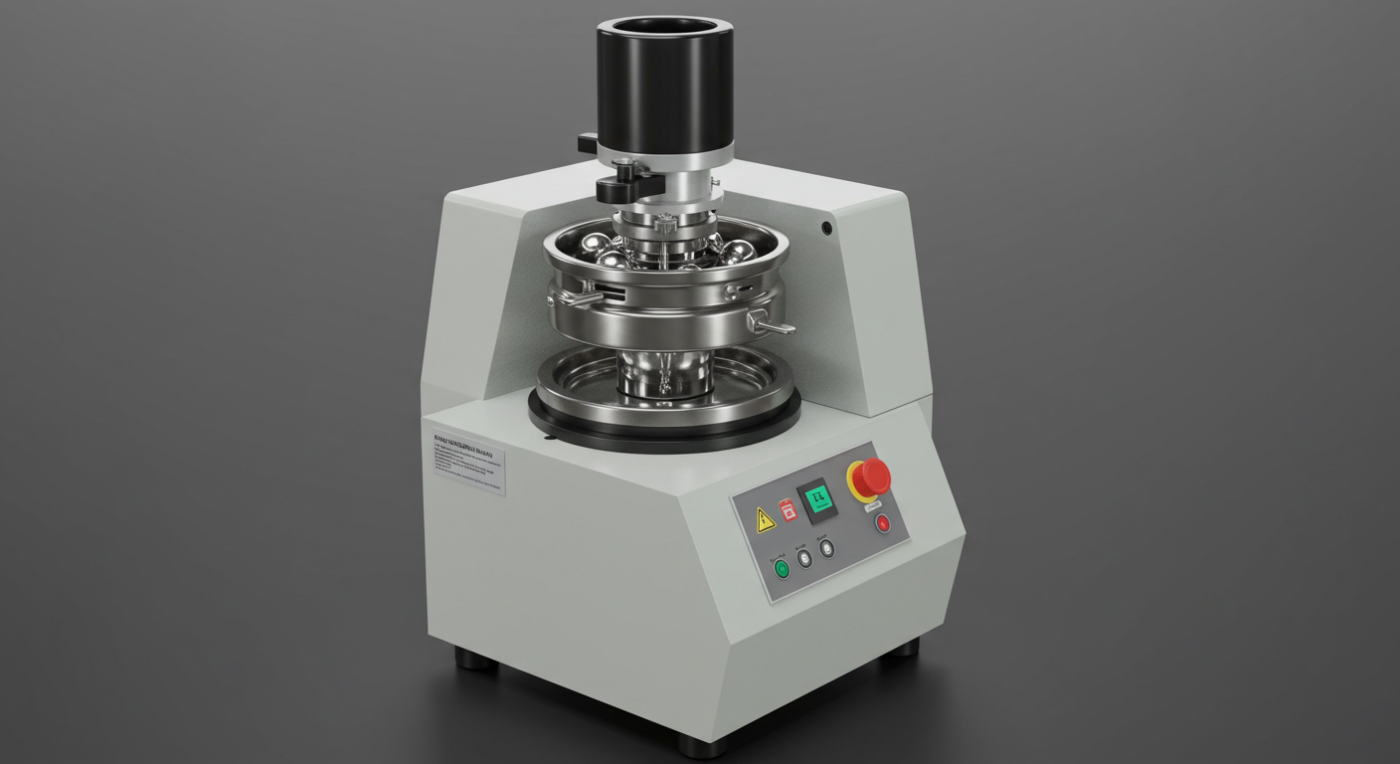
1. What is a Ball Grinder Machine, and How Does It Work?
A ball grinder machine, also known as a ball mill, is a type of grinder used to grind materials into fine powder. It utilizes steel balls as grinding media to achieve the desired particle size. The machine operates on the principle of impact and attrition, where the balls and materials are subjected to high-pressure grinding action inside the mill.
1.1 Key Components of a 3lb Ball Mill
The following table outlines the key components of a ball grinder machine:
Component | Description |
---|---|
Mill Shell | The cylindrical shell that houses the grinding media and materials. |
Meios de moagem | Steel balls used for grinding the materials. |
Feed Chute | The opening through which materials are fed into the mill. |
Discharge Chute | The opening through which the ground materials are discharged. |
Drive System | The mechanism that rotates the mill shell and drives the grinding process. |
Ball Charging Device | The device that charges the steel balls into the mill. |
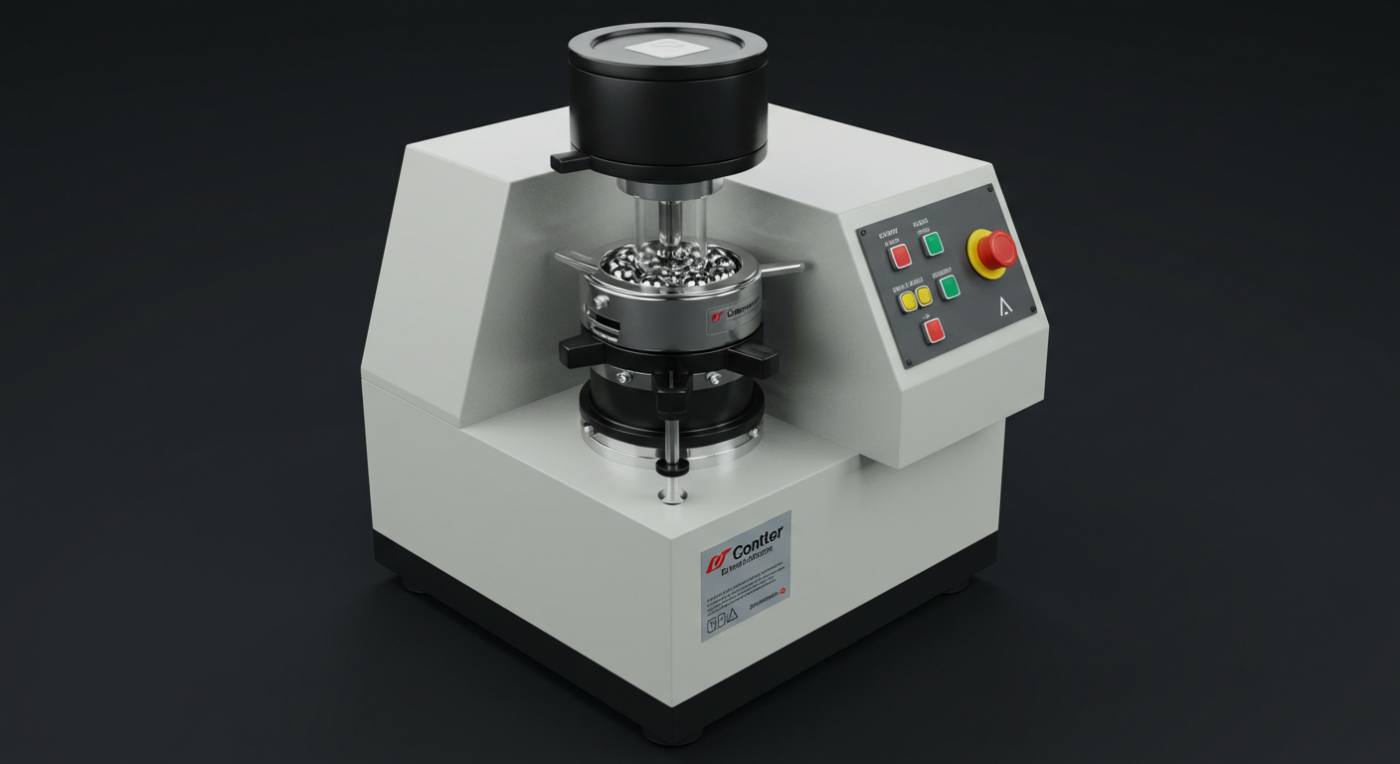
2. How to Safely Operate a Ball Grinder Machine?
Safety is paramount when operating a ball grinder machine. The following guidelines will help you ensure a safe working environment:
2.1 Pre-Operation Checks
Before starting the machine, perform the following checks:
- Ensure that the machine is properly grounded.
- Verify that all guards and safety devices are in place.
- Check for any loose bolts or nuts.
- Confirm that the grinding media is correctly charged.
2.2 Operating Procedures
When operating the ball grinder machine, follow these steps:
- Start the machine at low speed to allow the grinding media to settle.
- Gradually increase the speed to the desired operating level.
- Monitor the process and adjust the speed as necessary.
- Regularly inspect the machine for any signs of wear or damage.
- Stop the machine immediately if any abnormal noise or vibration is detected.
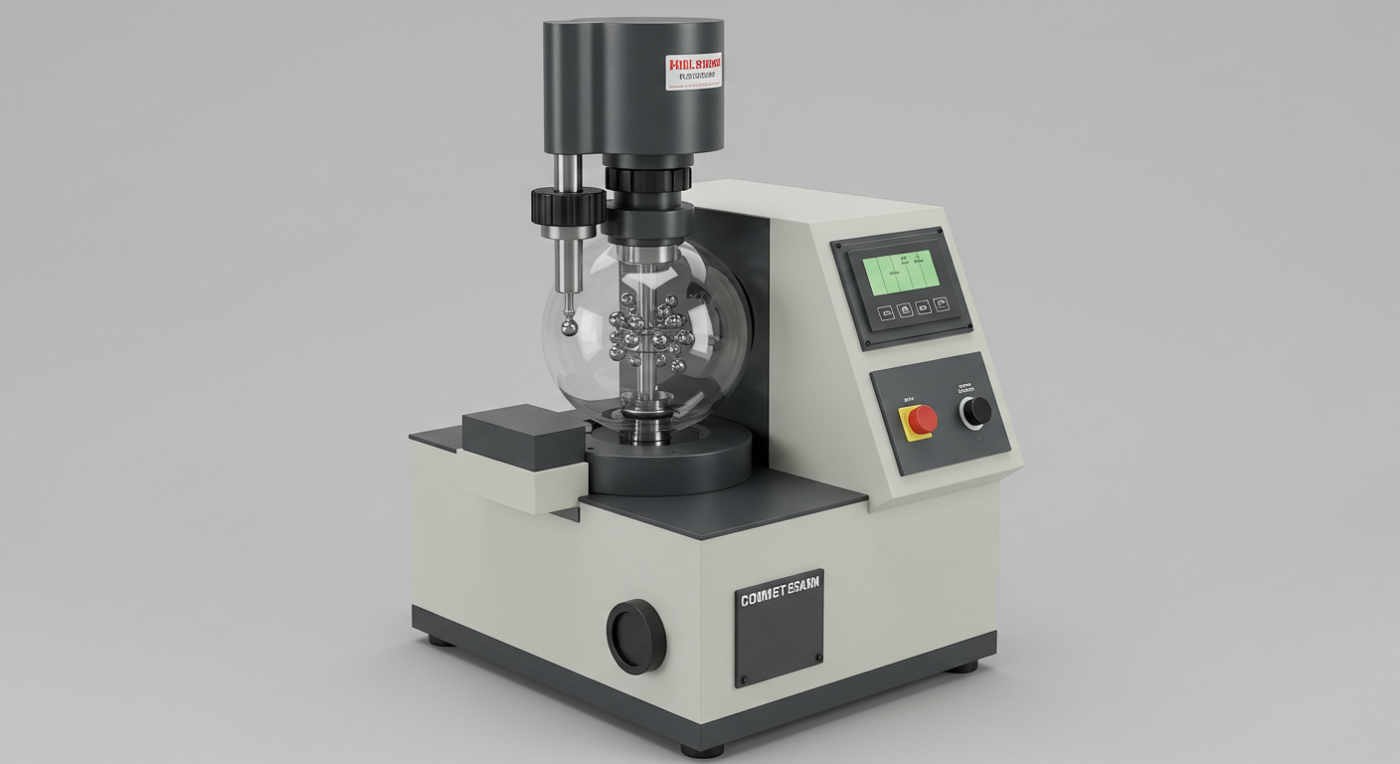
3. Maintenance and Troubleshooting
Regular maintenance is essential to ensure the longevity and efficiency of a ball grinder machine. Here are some key maintenance and troubleshooting tips:
3.1 Maintenance Schedule
The following table provides a general maintenance schedule for a ball grinder machine:
Task | Frequency |
---|---|
Inspection of guards and safety devices | Daily |
Check for loose bolts and nuts | Weekly |
Clean the mill shell and discharge chute | Monthly |
Replace worn-out grinding media | As required |
Overhaul the drive system | Annually |
3.2 Troubleshooting
If you encounter any issues with your ball grinder machine, refer to the following troubleshooting guide:
Problem | Possible Cause(s) | Solution |
---|---|---|
Abnormal noise or vibration | Worn-out grinding media, loose bolts, or unbalanced mill shell | Check and replace worn-out grinding media, tighten loose bolts, and balance the mill shell |
Low grinding efficiency | Incorrect grinding media size, inadequate ball charging, or improper feed rate | Adjust the grinding media size, ensure proper ball charging, and optimize the feed rate |
Excessive dust emission | Inadequate ventilation or clogged dust filter | Improve ventilation and clean the dust filter |
4. Case Study: Improving Grinding Efficiency in a Ceramics Plant
A ceramics plant was experiencing low grinding efficiency with their existing ball grinder machine. After analyzing the situation, the plant manager decided to follow the user manual’s guidelines for maintenance and troubleshooting. They replaced the worn-out grinding media, optimized the feed rate, and improved the ventilation system. As a result, the plant’s grinding efficiency increased by 20%, significantly reducing production costs.
Ball grinder machines are essential tools in various industries, including metalworking, mining, and ceramics. These machines are designed to grind and polish materials with precision. With a wide range of sizes available, selecting the right ball grinder machine is crucial for optimal performance. In this article, we will explore three key questions related to ball grinder machine sizes and provide a detailed analysis of product details, including a case study and a table of specifications.
1. What Are the Different Sizes of Ball Grinder Machines?
Ball grinder machines come in various sizes, each designed to cater to specific applications. The size of a ball grinder machine is typically determined by its grinding wheel diameter, length, and the maximum workpiece size it can accommodate. Here are some common sizes:
1.1 Small Ball Grinder Machines
- Grinding Wheel Diameter: 100mm – 200mm
- Length: 300mm – 500mm
- Maximum Workpiece Size: 150mm x 150mm
1.2 Medium Ball Grinder Machines
- Grinding Wheel Diameter: 250mm – 400mm
- Length: 500mm – 700mm
- Maximum Workpiece Size: 300mm x 300mm
1.3 Large Ball Grinder Machines
- Grinding Wheel Diameter: 500mm – 800mm
- Length: 800mm – 1200mm
- Maximum Workpiece Size: 500mm x 500mm
2. How to Choose the Right Size for Your Application?
Selecting the right ball grinder machine size depends on several factors, including the type of material, the desired finish, and the production volume. Here are some tips to help you make the right choice:
2.1 Material Type
Different materials require different grinding wheel sizes and speeds. For example, harder materials like stainless steel may require a larger grinding wheel and higher speed.
2.2 Desired Finish
A finer finish requires a slower grinding speed and a smaller grinding wheel. Conversely, a coarser finish can be achieved with a higher speed and larger grinding wheel.
2.3 Production Volume
For high-volume production, a larger ball grinder machine may be more suitable. This will help you save time and reduce labor costs.
3. Case Study: Ball Grinder Machine Size Selection
3.1 Project Overview
A metalworking company specializing in the production of precision parts for aerospace applications needed a ball grinder machine to achieve a fine finish on small, intricate parts.
3.2 Solution
After analyzing the company’s requirements, we recommended a medium-sized ball grinder machine with a grinding wheel diameter of 250mm and a maximum workpiece size of 300mm x 300mm.
3.3 Results
The company experienced improved productivity and a significant reduction in labor costs. The ball grinder machine was able to achieve the desired finish on the small, intricate parts with minimal operator intervention.
Table of Ball Grinder Machine Specifications
Machine Size | Grinding Wheel Diameter (mm) | Length (mm) | Maximum Workpiece Size (mm) | Speed (RPM) | Power (kW) |
---|---|---|---|---|---|
Small | 100 – 200 | 300 – 500 | 150 x 150 | 1500 – 3000 | 0.75 – 1.5 |
Medium | 250 – 400 | 500 – 700 | 300 x 300 | 1500 – 3000 | 2 – 3 |
Large | 500 – 800 | 800 – 1200 | 500 x 500 | 1000 – 2000 | 3 – 5 |
The ball grinder machine process is a crucial aspect of metalworking and material processing industries. This article delves into the intricacies of the ball grinder machine process, analyzing key questions and providing a detailed breakdown of product specifications. We will also present a case study and organize the information in a tabular format for easy reference.
Table of Contents
- Introduction to Ball Grinder Machine Process
- Key Questions about Ball Grinder Machine Process
- Case Study: Ball Grinder Machine in Automotive Industry
- Product Specifications of Ball Grinder Machines
- Conclusion
1. Introduction to Ball Grinder Machine Process
The ball grinder machine process is a type of abrasive machining process used to finish, deburr, and improve the surface quality of metal components. It involves rotating balls in a container filled with abrasive material, which in turn grinds the workpiece. This process is widely used in various industries, including automotive, aerospace, and medical.
2. Key Questions about Ball Grinder Machine Process
a. What is the purpose of the ball grinder machine process?
The primary purpose of the ball grinder machine process is to achieve a smooth and precise surface finish on metal components. It also helps in removing burrs, sharp edges, and other surface imperfections.
b. How does the ball grinder machine process work?
The ball grinder machine process works by rotating balls made of abrasive materials, such as silicon carbide or aluminum oxide, in a container filled with abrasive material. The workpiece is placed in the container, and the balls and abrasive material grind the workpiece to achieve the desired surface finish.
c. What are the advantages of the ball grinder machine process?
The ball grinder machine process offers several advantages, including:
- Improved surface finish
- Reduced material removal rate
- Reduced tool wear
- Enhanced dimensional accuracy
d. What are the limitations of the ball grinder machine process?
The limitations of the ball grinder machine process include:
- High initial investment cost
- Limited applicability to certain materials
- Requirement for skilled operators
3. Case Study: Ball Grinder Machine in Automotive Industry
The automotive industry heavily relies on the ball grinder machine process for finishing various components, such as engine parts, gears, and camshafts. Here’s a case study highlighting the use of ball grinder machines in the automotive industry:
a. Case Study: Gear Finishing
In this case study, a ball grinder machine is used to finish gears for an automotive transmission. The machine is equipped with silicon carbide balls and abrasive material. The process involves the following steps:
- Load the gears into the ball grinder machine.
- Add the abrasive material and silicon carbide balls.
- Set the appropriate grinding parameters, such as speed and time.
- Start the machine and monitor the process.
- Remove the gears after the grinding process is complete.
The ball grinder machine process provides a smooth and precise surface finish on the gears, which is essential for their performance and longevity.
4. Product Specifications of Ball Grinder Machines
Below is a table showcasing the product specifications of ball grinder machines:
Especificação | Description |
---|---|
Modelo | Ball Grinder Machine Model X |
Grinding Capacity | 50 kg to 500 kg |
Grinding Material | Silicon Carbide, Aluminum Oxide, etc. |
Fonte de alimentação | 3-phase, 380V, 50/60 Hz |
Velocidade | 600 to 1500 rpm |
Dimensions (LxWxH) | 1500 x 800 x 1200 mm |
Weight | 1000 kg to 3000 kg |
Conclusion
A ball grinder machine user manual is a valuable resource for understanding the operation, maintenance, and troubleshooting of these essential tools. By following the guidelines outlined in this article, you can ensure safe and efficient operation of your ball grinder machine, ultimately leading to improved productivity and reduced downtime.