Planetary Ball Mill for Materials Processing
Visão geral
The Planetary Ball Mill (PBM) is a high-energy ball mill that is used for the preparation of fine powder materials. It is designed for wet or dry grinding, mixing, and blending of materials. The mill can handle a variety of materials, including hard, brittle, and fibrous materials, as well as ceramics, minerals, and metals. It is particularly useful in research and development for new materials, in the preparation of samples for analysis, and in small-scale production.
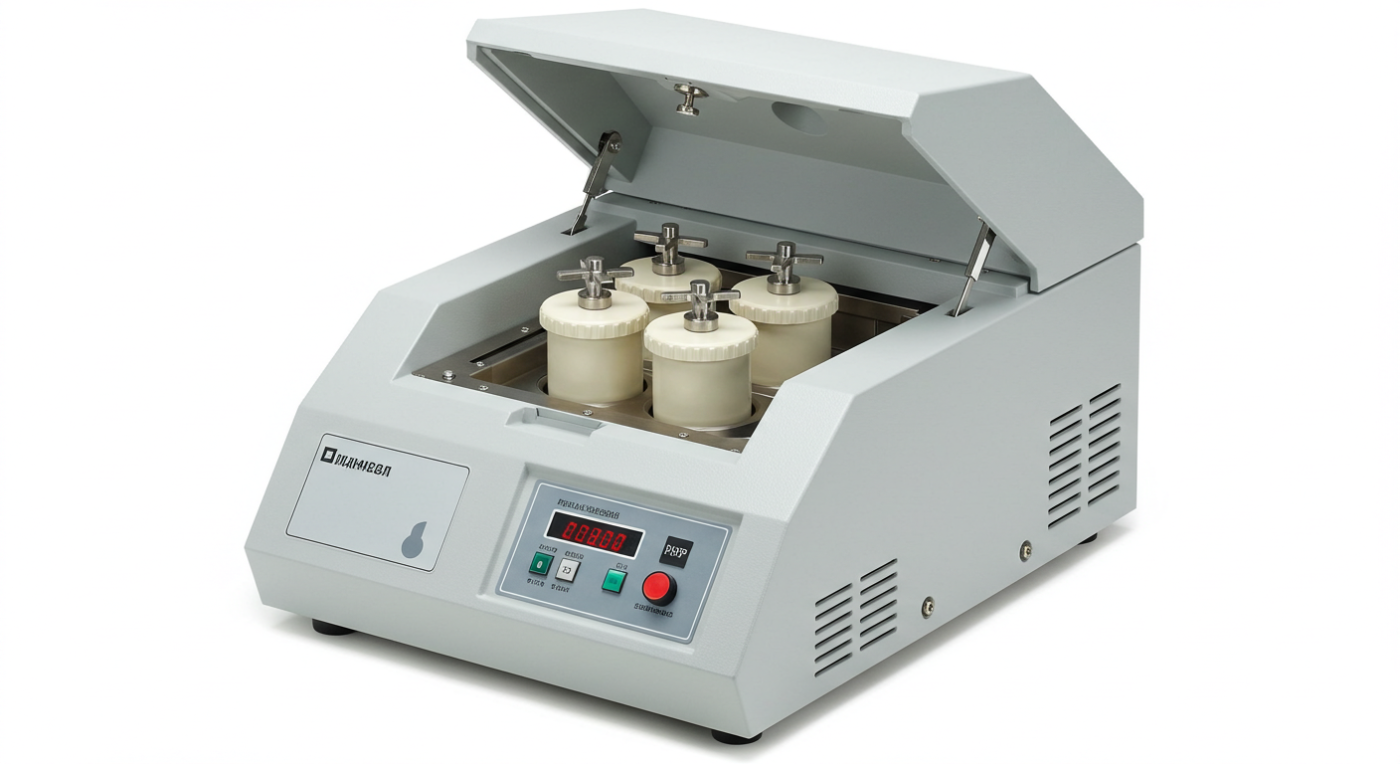
Características
- Planetary Action: The balls are subjected to a high-speed movement in a planetary orbit, which results in a high energy input and a very fine powder product.
- High Energy Input: This mill is capable of producing particles with a size of 0.1 to 5 micrometers.
- Flexible Design: It can be used for a variety of applications, including dry grinding, wet grinding, mixing, and blending.
- Temperature Control: Many models come with temperature control features to prevent overheating and to maintain the desired conditions for the materials being processed.
- Safety Features: Modern planetary ball mills often include safety features such as emergency stop buttons and automatic shutdown in case of malfunctions.
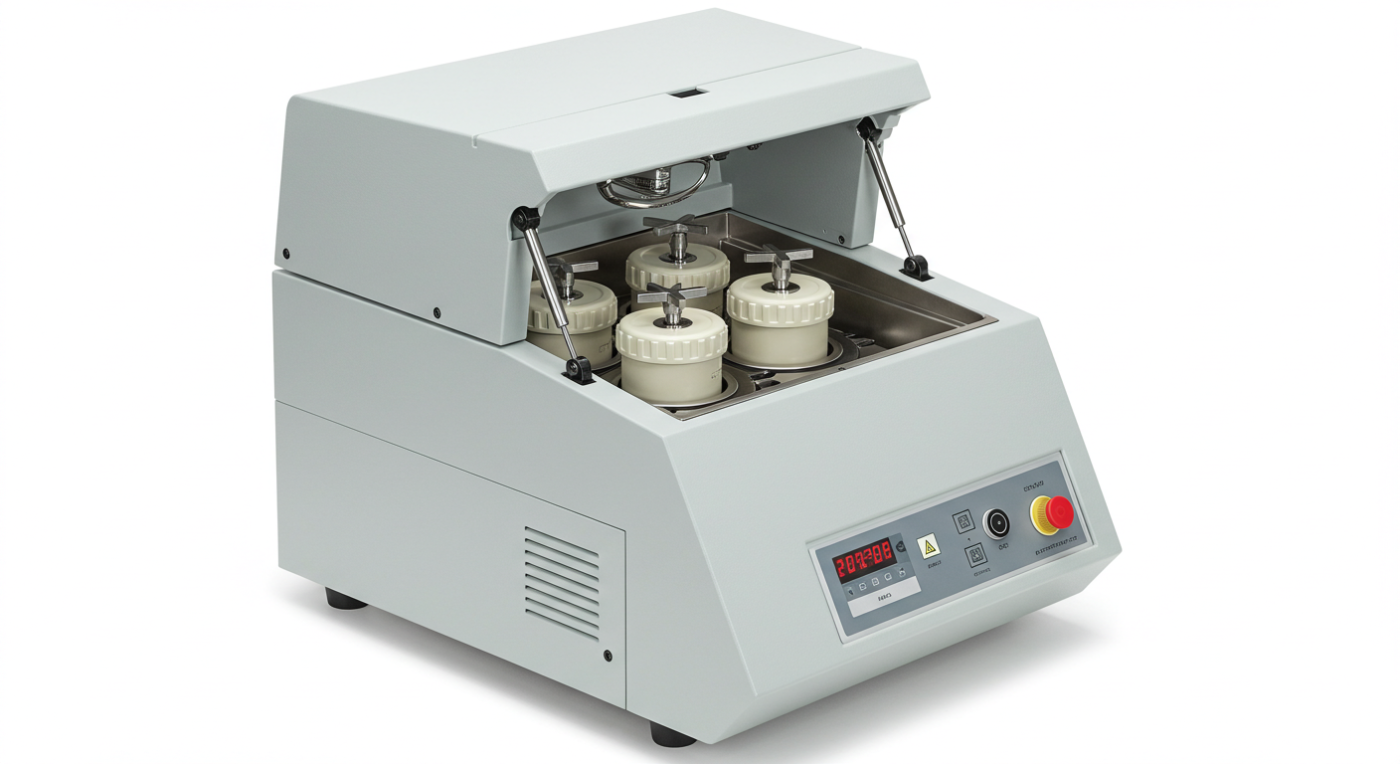
Components
- Mill Jars: These are the containers where the materials are placed for grinding. They are usually made of materials like stainless steel, quartz, or alumina, depending on the application and the material being processed.
- Ball Charge: The ball charge consists of balls made of materials such as steel, tungsten carbide, or ceramic. The size and composition of the balls can be selected based on the application.
- Drive System: The drive system includes the motor, gears, and other mechanical components that power the mill.
- Control Panel: This is where the operator can set the parameters for the grinding process, such as speed, time, and temperature.
- Cooling System: Optional cooling systems can be attached to the mill to dissipate heat generated during the grinding process.
Aplicações
- Material Preparation: For research and development of new materials, such as ceramics, polymers, and metals.
- Sample Preparation: For analysis of materials by techniques like X-ray diffraction, scanning electron microscopy, and differential thermal analysis.
- Production of Nanomaterials: The ability to produce particles with a size of 0.1 to 5 micrometers makes it suitable for the production of nanomaterials.
- Milling of Hard Materials: It can be used to mill hard materials like ceramics and minerals.
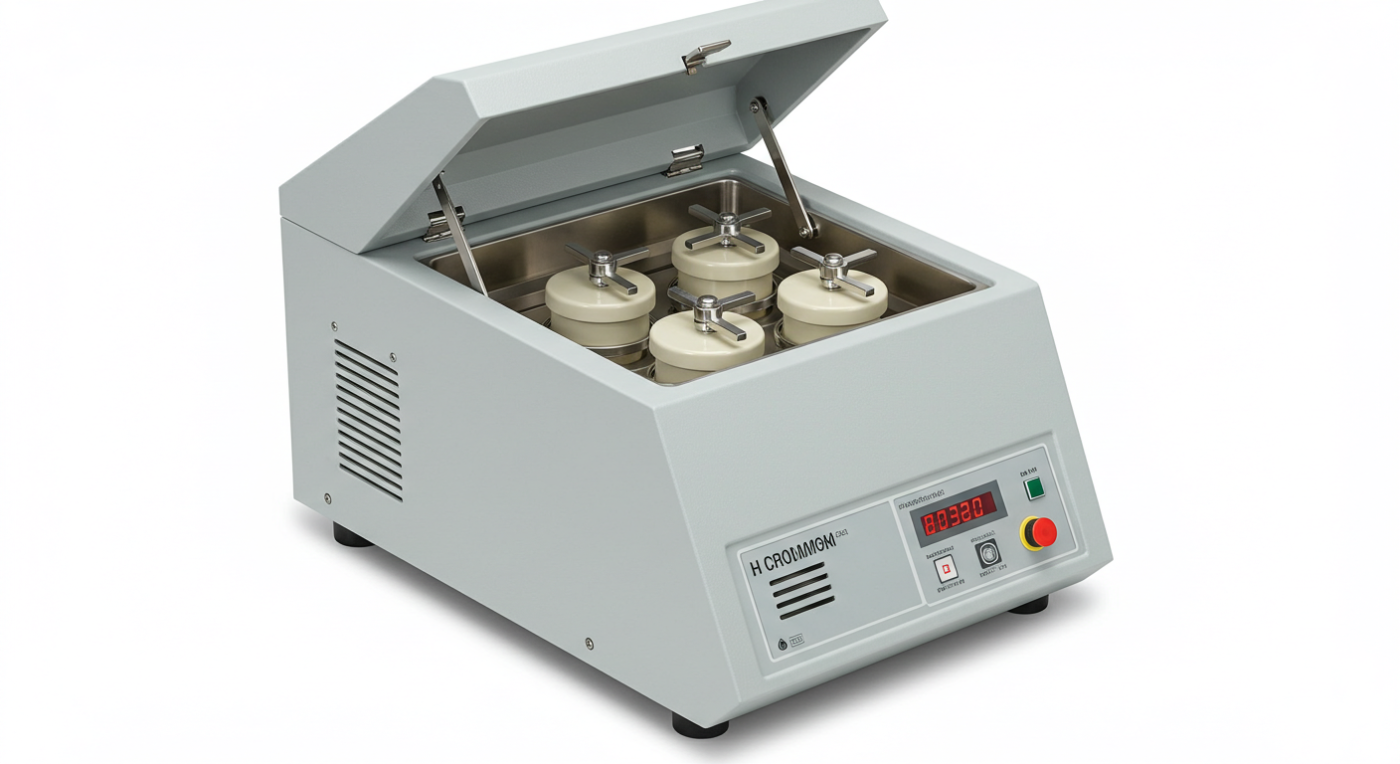
Operating Procedure
- Selection of Mill Jars and Balls: Choose the appropriate jars and balls based on the material being ground and the desired particle size.
- Loading the Mill: Load the jars with the material and the ball charge into the mill. The load factor should be adjusted based on the type of material and the desired particle size.
- Setting Parameters: Set the grinding parameters on the control panel, such as speed, time, and temperature.
- Starting the Mill: Start the mill and monitor the process. Adjust the parameters if necessary.
- Collecting the Sample: Once the grinding is complete, remove the mill jars and collect the sample.
Maintenance
- Regular Cleaning: Clean the mill jars and balls after each use to prevent contamination.
- Check Drive System: Regularly inspect the drive system for wear and tear.
- Cooling System: Ensure the cooling system is functioning properly to prevent overheating.
Safety
- Always wear appropriate personal protective equipment (PPE) such as safety glasses, gloves, and lab coats.
- Ensure that the mill is properly grounded to prevent electrical hazards.
- Never exceed the maximum speed or load factor of the mill.
The Planetary Ball Mill is a versatile piece of laboratory equipment that is essential for materials processing in many fields. Its ability to produce fine particles with high energy input makes it a valuable tool for researchers and manufacturers alike.
A laboratory scale planetary ball mill is a type of mechanical mill used for the grinding of small amounts of hard, brittle, or fibrous materials. The system is designed to mimic the planetary motion of larger industrial ball mills but on a smaller scale, making it suitable for research and development purposes. Below is a plan for a laboratory scale planetary ball mill system:
1. System Overview
Purpose: The system is designed to grind samples with a high degree of fineness for various applications in materials science, mining, geology, and other research fields.
Features:
- Planetary motion for efficient grinding
- Capacity for a few grams to a few tens of grams of material
- Easy-to-clean and disassemble parts
- Multiple jar sizes for different sample volumes
- Variable speed control
- Safety features like emergency stop and overload protection
2. System Components
a. Main Unit
- Base: Sturdy metal base with leveling feet.
- Motor: High-torque motor for planetary rotation.
- Gears: Planetary gear system to drive the grinding jars.
- Control Panel: Digital speed control, safety features, and power switch.
b. Grinding Jars and Balls
- Jars: Multiple jars of different sizes to accommodate various sample volumes.
- Balls: Various sizes of balls made from materials like stainless steel, hardened steel, or tungsten carbide.
c. Safety Features
- Emergency Stop: Instant shutdown of the mill in case of emergency.
- Overload Protection: Prevents motor damage from excessive loads.
- Noise and Vibration Dampers: Minimize noise and vibration during operation.
d. Accessory Items
- Sample Funnel: For easy loading of samples.
- Gloves: To protect the operator from sharp edges or chemicals.
- Cleaning Supplies: Brushes, detergents, and wipes for cleaning the mill.
3. Design and Construction
a. Main Unit
- Frame: Constructed from high-strength steel or aluminum to withstand the forces of grinding.
- Motor: A variable-speed motor capable of handling the torque requirements of the planetary gear system.
- Gears: Precision-machined gears that ensure smooth operation and minimal wear.
- Bearings: High-quality bearings to support the rotation and reduce friction.
b. Grinding Jars
- Material: Stainless steel or other non-reactive materials.
- Design: High-quality ceramic or metal jar with a tight-fitting lid to prevent material spillage.
- Sealing: O-rings or similar seals to ensure airtight operation.
c. Planetary Gear System
- Mechanism: A planetary gear system that drives the grinding jars to rotate in a unique elliptical path, providing intense and uniform grinding action.
- Alignment: Precise alignment of the gears to ensure smooth and efficient operation.
4. Operation
a. Sample Preparation
- Weigh the sample and place it in the appropriate size of the grinding jar.
- Add grinding balls that are appropriate for the material being milled and the desired fineness.
b. Loading the Mill
- Place the filled jar into the mill.
- Ensure the lid is securely fastened.
- Turn on the mill and adjust the speed to the desired setting.
c. Grinding Process
- The mill will operate for the duration specified, typically a few minutes to a few hours.
- The jars rotate in a planetary motion, grinding the material and balls against each other.
d. Unloading and Cleaning
- After the grinding process, turn off the mill and allow it to cool.
- Remove the jar and empty the contents.
- Clean the jar and balls using the appropriate cleaning supplies.
5. Safety and Maintenance
a. Safety
- Always wear appropriate personal protective equipment (PPE) such as gloves and safety glasses.
- Ensure the mill is properly grounded.
- Do not operate the mill without the lid securely fastened.
- Follow all safety instructions provided by the manufacturer.
b. Maintenance
- Regularly inspect the mill for wear and tear.
- Clean the mill after each use to prevent contamination.
- Replace worn-out parts as necessary.
6. Testing and Quality Assurance
a. Performance Testing
- Test the mill’s ability to grind various materials to a specified particle size.
- Evaluate the mill’s consistency and reproducibility in grinding samples.
b. Quality Assurance
- Establish quality control procedures for the mill’s operation.
- Ensure that the mill meets the requirements of the research or industrial application.
By following this plan, you can create a laboratory scale planetary ball mill system that is efficient, safe, and capable of producing high-quality grinding results for a wide range of materials.
A Planetary Ball Mill is a small-scale machine used in research and development, quality control, and small batch production to simulate the operation of a large-scale ball mill in a laboratory setting. The planetary ball mill operates on the principle of high-energy ball milling, where the materials are subjected to mechanical alloying, particle size reduction, or mixing. Below is a detailed plan for a Planetary Ball Mill:
1. Introduction
Objective: The primary purpose of the Planetary Ball Mill is to simulate the grinding process of a large-scale industrial ball mill for research and development in materials science, mining, ceramics, and other fields.
Features:
- Compact design for laboratory use.
- High-speed rotation of the grinding jar.
- Planetary motion of the grinding balls.
- Various jar sizes and ball materials available.
2. Design Specifications
Dimensions:
- Length: 300 mm
- Width: 300 mm
- Height: 500 mm
Weight:
- Approx. 20 kg
Grinding Jar Capacity:
- 50 mL to 500 mL
Power Supply:
- 220-240 V, 50/60 Hz, 1 Phase
Motor Power:
- 250-500 W
Grinding Jar Speed:
- 400-500 rpm
Ball Jar Rotation Speed:
- 120-150 rpm
3. Components
Main Components:
- Drive motor
- Main shaft
- Planetary gears
- Grinding jar holder
- Grinding jar
- Grinding balls
- Ball lifting mechanism
- Safety interlock switch
- Control panel
Additional Components:
- Dust collection system
- Temperature sensor
- Voltage and current monitor
4. Working Principle
Grinding Jar Rotation: The grinding jar is mounted on the main shaft and rotates at a high speed, causing the grinding balls to impact the materials within the jar.
Planetary Motion: The planetary gears cause the grinding balls to rotate around the jar’s axis, which enhances the impact force and ensures that all materials are exposed to the grinding action.
Ball Lifting Mechanism: A mechanical system raises and lowers the grinding jar, allowing for the loading and unloading of materials.
5. Operation
Preparation:
- Assemble the machine according to the manufacturer’s instructions.
- Clean the grinding jar and balls.
- Ensure that the power supply is stable and the safety interlock switch is working.
Loading:
- Load the grinding jar with the desired materials and grinding balls.
- Secure the jar in place.
Operation:
- Turn on the machine and set the desired rotation speeds for the grinding jar and ball jar.
- Start the grinding process and monitor the operation.
- Periodically check the temperature and voltage/current to ensure proper operation.
Maintenance:
- Clean the machine after use.
- Check the lubrication and alignment of the gears and bearings.
- Replace worn-out parts as necessary.
6. Safety Measures
- Wear appropriate personal protective equipment, such as safety goggles and gloves.
- Ensure that the machine is properly grounded.
- Do not exceed the recommended speeds or loading capacity.
- Do not leave the machine unattended during operation.
- Regularly inspect the machine for wear and tear.
7. Applications
- Material synthesis
- Nanomaterial preparation
- Sample preparation for X-ray diffraction, SEM, and TEM
- Alloys development
- Battery materials preparation
8. Conclusion
The Planetary Ball Mill is a versatile tool for simulating the grinding process of large-scale ball mills. It is ideal for research and development in various fields, including materials science, mining, and ceramics. Proper operation, maintenance, and safety measures are crucial for obtaining accurate and consistent results.