A mini planetary ball mill is a smaller, laboratory-scale version of a standard planetary ball mill. It utilizes the same core principles of centrifugal and inertial forces to induce high-energy impacts and shearing forces on materials within grinding jars, leading to size reduction and efficient mixing. The term “mini” highlights their reduced size, making them suitable for laboratories and small-scale research operations where space and sample volumes are limited.
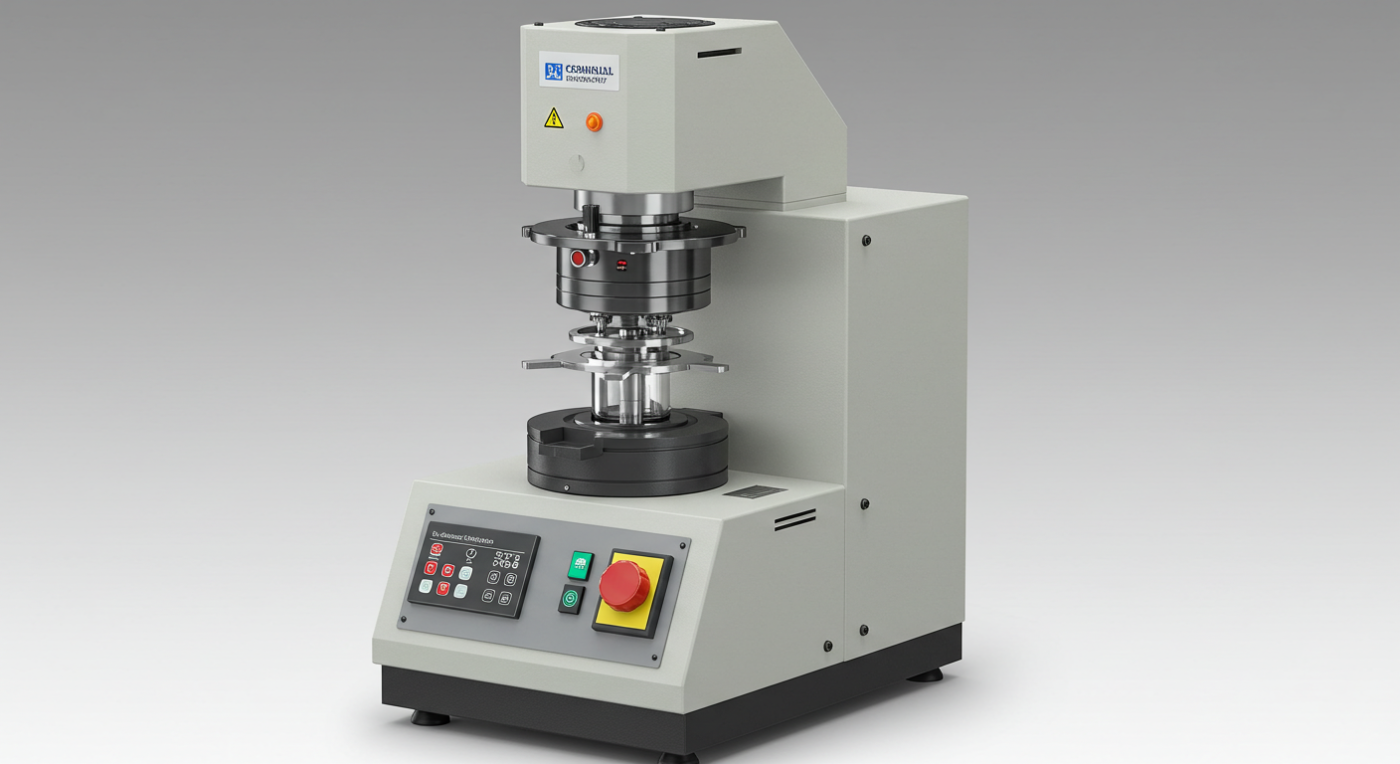
The fundamental mechanism of a mini planetary ball mill is identical to that of its larger counterparts, with a central support disk (the “sun” gear) that rotates, and grinding jars (the “planets”) mounted on this disk, rotating around their own axes in the opposite direction.
- Where Can I Buy a Planetary Ball Mill: A Comprehensive Guide
- Understanding Tabletop Ball Mills: An Overview of Important Parameters
- For Sale: Ceramic Ball Mill User Guide
- User Manual for the Lab Ball Mill Equipment
- Micro Ball Mill Specifications
This dual rotation results in a complex motion and a variety of forces acting on the milling media and the materials being processed.
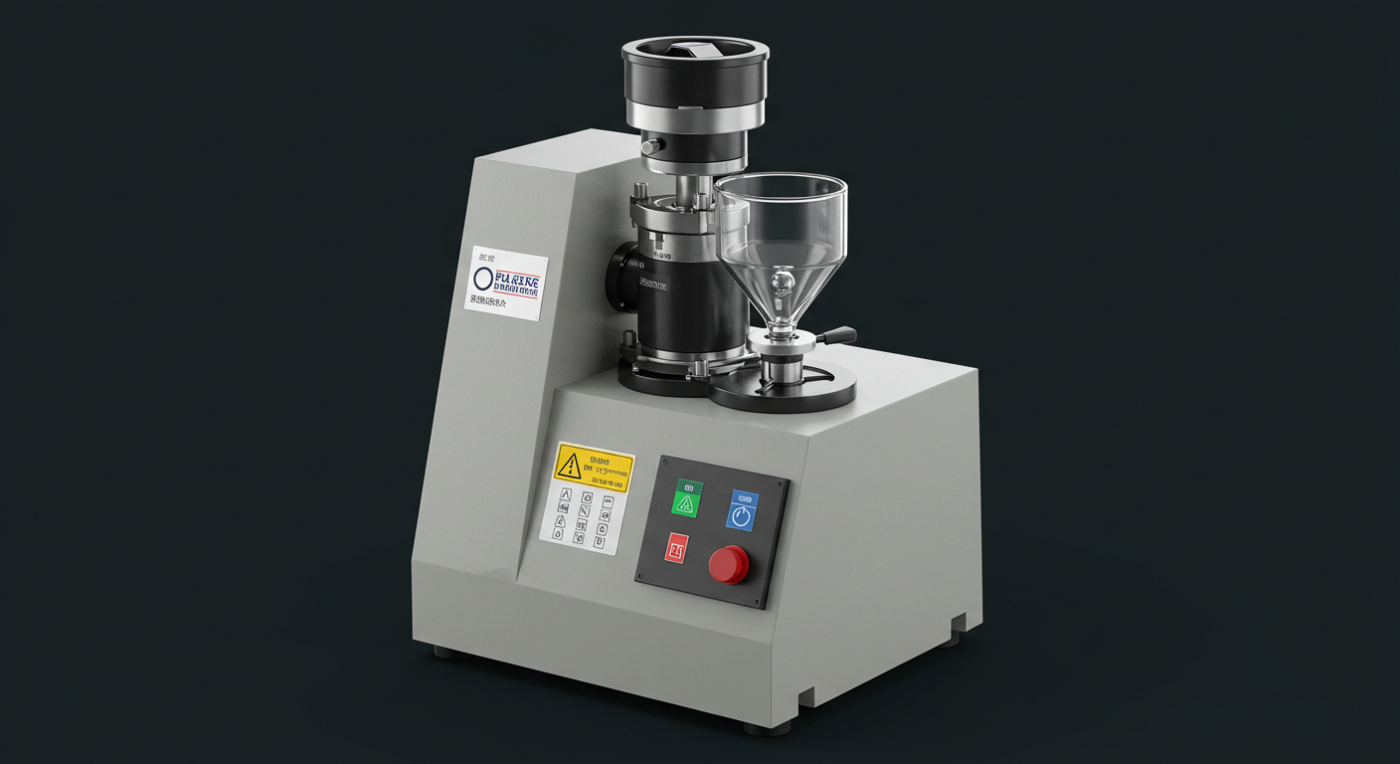
Key Features and Characteristics of Mini Planetary Ball Mills
Mini planetary ball mills are characterized by several distinct features:
- Compact Design: The most notable feature is their small size and benchtop design, making them ideal for laboratories with limited space.
- Small Capacity: They are designed to process smaller quantities of material, typically ranging from a few grams to a few hundred grams per jar.
- Precise Control: Mini planetary ball mills often offer highly precise control over parameters such as milling speed, time, and temperature, allowing for accurate and repeatable results.
- Versatility: They can be used to process a wide variety of materials, including metals, ceramics, polymers, and composites, much like larger planetary mills.
- Multiple Jars: Most mini planetary ball mills feature multiple grinding jars, allowing for parallel processing of several samples simultaneously.
- Various Jar Materials: These mills typically offer a range of jar materials, including stainless steel, tungsten carbide, zirconia, agate, and hardened steel, to meet the requirements of different materials and applications.
- Safety Features: Many models incorporate safety features such as automatic shut-off mechanisms to prevent accidents and damage.
- Easy Operation: Mini planetary ball mills are designed for ease of use and operation, with intuitive interfaces and controls.
- Low Maintenance: They generally require low maintenance, with easily replaceable components.
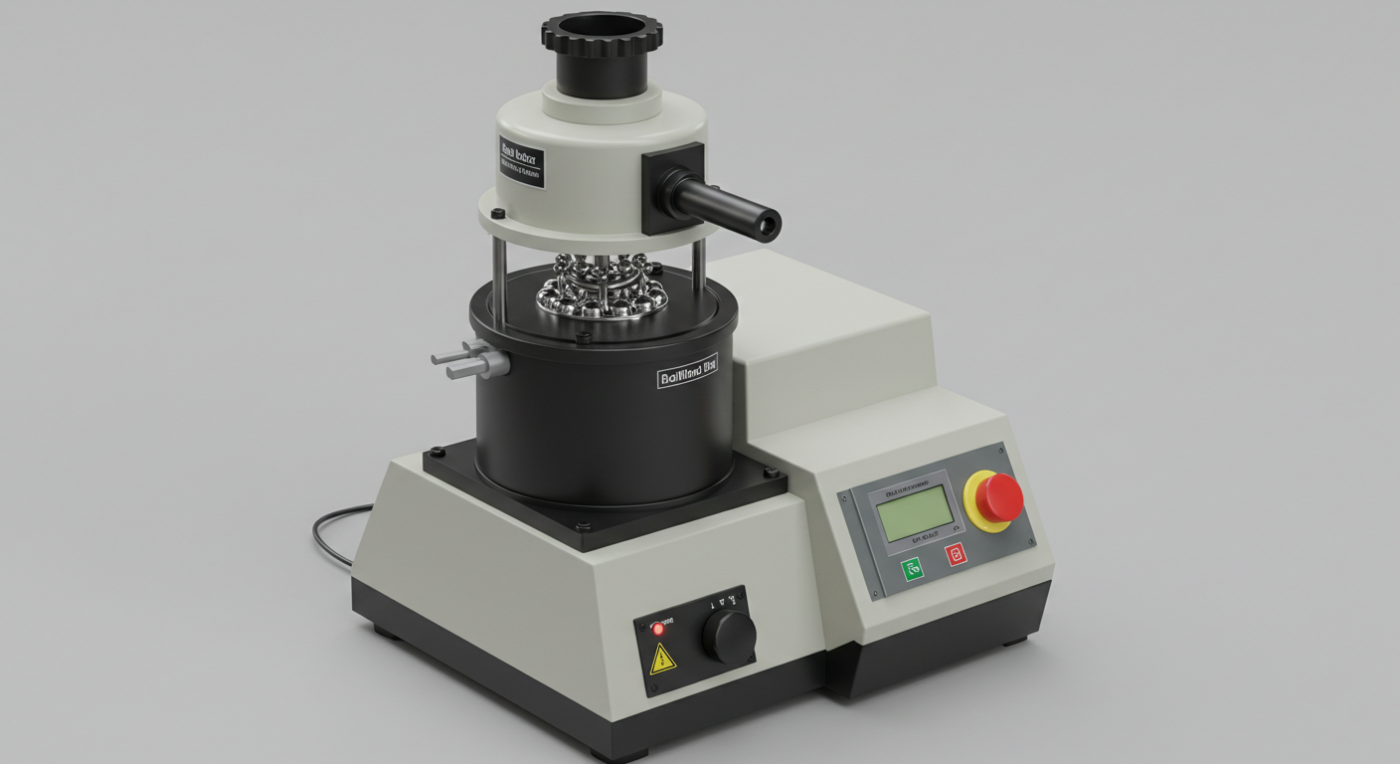
The Mechanics of Mini Planetary Ball Mills
Like their larger counterparts, mini planetary ball mills operate using the following mechanical principles:
- Dual Rotation: The support disk rotates around its center axis, while the grinding jars simultaneously rotate around their own axes.
- Centrifugal Force: The rotation of the support disk and the jars creates a centrifugal force, pushing the milling media (balls) and the material outwards towards the jar walls.
- Coriolis Force: The combined rotational motion generates a Coriolis force, which influences the motion of the particles within the jars.
- Impact Forces: The combined action of centrifugal and Coriolis forces causes the milling media to collide with the material and the jar walls, leading to size reduction and mixing.
- Shearing and Frictional Forces: The movement of the materials and the milling media within the jars leads to shearing and frictional forces, further assisting with milling.
The combined effect of these forces within the small jars of a mini planetary ball mill ensures effective and rapid size reduction, mixing, and mechanochemical reactions.
Advantages of Mini Planetary Ball Mills
Mini planetary ball mills offer a range of advantages, making them indispensable in research and development:
- Ideal for Small Sample Sizes: They are perfect for processing small material quantities that are typical in research and development labs.
- High Milling Efficiency: Mini planetary ball mills can achieve rapid size reduction and efficient mixing of materials due to the high-energy impacts they produce.
- Precise Parameter Control: Researchers can control parameters, such as speed and time, very precisely to obtain repeatable and accurate results.
- Versatility: They can be used to process a wide range of materials, including hard and brittle substances, soft polymers, and even liquids.
- Easy Handling and Operation: Their benchtop design, compact size, and user-friendly controls make them easy to operate and maintain.
- Reduced Material Waste: The small-scale nature of these mills minimizes material waste, which is particularly valuable when working with expensive or rare substances.
- Fast Milling Times: Due to their high milling efficiency, mini planetary mills can achieve the desired level of milling in shorter times compared to other methods, which saves valuable research time.
- Cost-Effectiveness: Compared to industrial-scale planetary mills, mini mills are more affordable, making them accessible to academic laboratories and small companies.
- Parallel Processing: With multiple milling jars, several different samples can be processed simultaneously.
- Controlled Atmosphere Milling: Some mini planetary mills are designed for controlled atmosphere milling, which can be important for processing reactive or temperature-sensitive materials.
Limitations and Disadvantages of Mini Planetary Ball Mills
Despite their advantages, mini planetary ball mills also have some limitations:
- Limited Throughput: The small capacity limits their throughput for larger-scale production runs.
- Heat Generation: High-energy milling can generate heat, which may be problematic for temperature-sensitive materials and can affect the properties of materials.
- Contamination Risk: Wear of milling jars and media can introduce trace amounts of impurities into the milled material if precautions are not taken, or incorrect materials are selected.
- Noise and Vibration: The high-speed rotation can produce noise and vibrations, which can be a concern in quiet lab environments.
- Batch Processing: These mills typically operate in batch processing mode, which is not ideal for continuous production runs.
- Potential for Agglomeration: Some materials can agglomerate during milling, particularly if the milling parameters are not correctly optimized.
- Jar and Media Selection: Selecting the correct jar and media materials is crucial to prevent contamination and to obtain optimal results.
- Scale-Up Challenges: Results obtained from mini planetary mills might not directly translate to larger-scale processes due to differences in energy input and other parameters.
- Limited Automation: Most mini planetary mills offer basic automation options, but full automation is limited compared to industrial milling machines.
- Maintenance: Regular maintenance, such as replacing milling jars and media, is necessary.
Types of Mini Planetary Ball Mills
Mini planetary ball mills come in different configurations and types, each with specific features for particular applications:
- Standard High-Energy Ball Mills: This is the most common type, offering versatile milling options for a wide variety of materials. They typically use steel, zirconia, or tungsten carbide balls as the milling media and are ideal for producing fine powders.
- High-Speed Ball Mills: These mills are designed for extremely fast milling, allowing for production of very fine particles in shorter times. They are often used for producing nano-powders or for mechanically alloying materials.
- Cryogenic Ball Mills: These mills are equipped with cooling systems to maintain low temperatures during milling, which is essential for processing temperature-sensitive materials, such as polymers or waxes.
- Vacuum Ball Mills: Operating under vacuum reduces oxidation or any unwanted chemical reactions between the milling material and the surrounding environment. These are commonly used for processing reactive or highly sensitive materials.
- Variable-Speed Ball Mills: These models offer a wide range of speed settings, which allow for precise control of the milling process and are useful for optimizing milling parameters.
- Single-Jar Ball Mills: These models are designed for single samples or very small quantities of material. This is common for high precision materials where cross contamination must be minimized.
- Multiple-Jar Ball Mills: The most common configuration of ball mills, these types allow for simultaneous processing of several different samples using a single machine.
- Automated Ball Mills: Equipped with more sophisticated automation capabilities and software control, they offer greater control and reproducibility of the milling process.
- Wet Grinding Ball Mills: These models can handle wet milling processes, for materials that need to be milled in a liquid medium. They have sealed jars and often additional mixing capabilities.
- Customizable Ball Mills: Some manufacturers offer customizable ball mills designed to meet specific research and material needs.
Operational Parameters of Mini Planetary Ball Mills
Several parameters influence the performance of mini planetary ball mills:
- Milling Speed: The rotation speed of the support disk and jars is the most important factor affecting milling energy. Faster speeds typically result in faster size reduction.
- Milling Time: The duration of milling influences the final particle size and the homogeneity of the material. Longer milling times lead to finer particles and a more thorough mixing of the ingredients.
- Ball Size and Material: The size and material of the milling balls have a significant impact on milling efficiency. Larger balls are useful for coarse grinding, while smaller balls produce finer particles. The ball material must be compatible with the milling material.
- Ball-to-Powder Ratio: The ratio of the ball volume to the powder volume has a large influence on the energy transfer to the milling material. An optimal ratio ensures effective milling and prevents agglomeration.
- Milling Jar Type and Material: The jar material and size should be compatible with the material and sample size. Common materials are hardened steel, zirconia, stainless steel, agate, or tungsten carbide.
- Milling Atmosphere: Milling under vacuum or in inert gas prevents oxidation or other unwanted reactions.
- Temperature Control: The use of cooling systems is necessary for processing temperature-sensitive materials.
- Pre-Treatment: Sample materials might need pre-treatment before milling to get optimal results, e.g. pre-crushing, mixing, etc.
- Post-Treatment: Milled samples might require post-treatment, such as sieving, drying, or further processing depending on the application requirements.
- Loading and Unloading Procedures: The best loading and unloading procedure needs to be established to minimize losses and the chance of contamination.
Maintenance of Mini Planetary Ball Mills
Regular maintenance is crucial to ensure the proper functioning and longevity of a mini planetary ball mill:
- Cleaning: The milling jars and milling media must be thoroughly cleaned after each milling process to avoid cross-contamination.
- Jar Inspection: Jars should be regularly inspected for wear or damage and replaced as needed.
- Media Replacement: Milling media should also be replaced periodically as they wear down and become less efficient.
- Lubrication: Check and lubricate rotating parts of the mill to prevent premature wear or damage.
- Calibration: Calibrate the speed and other controls of the mill to ensure consistent results.
- Software Updates: For models with software control, keep the software up to date.
- Safety Checks: Regularly check safety features, such as shut-off switches, and emergency stops.
- Proper Storage: When not in use, store the mill in a dry, clean, and safe environment.
- Professional Service: If any issues are found or if the mill requires extensive maintenance, it is recommended to contact a professional technician for assistance.
- Operating Manual: Always consult the operating manual of your specific mill for specific instructions.
Comparison with Other Milling Techniques
Mini planetary ball mills are distinct from other milling techniques. Here is a brief comparison:
- Vibratory Ball Mills: Vibratory mills use vibrating motion for milling, which leads to less energy impact and less efficient size reduction.
- Attritor Mills: Attritor mills use a rotating agitator and stationary media for milling. These machines are very good for wet milling and have a high throughput, but do not offer as much energy as planetary ball mills.
- Jet Mills: Jet mills use compressed gas to collide particles with each other for size reduction. While good for specific materials, they cannot produce as small of a particle size as planetary ball mills.
- Hammer Mills: Hammer mills use rotating hammers for coarse grinding, but do not offer the fine milling capabilities of planetary ball mills.
- Mortar and Pestle: Mortar and pestle grinding is a manual method for small scale sample preparation, but it is very time consuming, labor intensive, not as consistent and not good for hard materials.
- Rotary Mills: Rotary mills use rotating knives or blades for size reduction. While suitable for coarse grinding, they are not designed for fine milling.
Applications of Mini Planetary Ball Mills
Mini planetary ball mills are used across various fields:
- Materials Science: Synthesis of nanoparticles, nanocomposites, and mechanically alloyed materials.
- Nanotechnology: Preparation of nanomaterials and nano powders.
- Pharmaceuticals: Micronization of drugs, formulation of solid dispersions, and mixing of pharmaceutical ingredients.
- Chemistry: Preparation of catalysts, mixing of chemicals, and initiation of mechanochemical reactions.
- Geology: Grinding of geological samples for analysis and x-ray diffraction studies.
- Ceramics: Preparation of ceramic powders for sintering and milling of ceramic materials.
- Cosmetics: Preparation of fine cosmetic powders and mixing of ingredients.
- Food Science: Grinding and mixing of food samples and preparation of food powders.
- Battery Technology: Preparation of battery electrode materials and composites.
- Research and Development: Sample preparation, process development, and materials testing.
Future Developments in Mini Planetary Ball Mills
Ongoing research and development in this field focus on:
- Smart Controls: Integrating AI and machine learning for real-time monitoring and parameter adjustments.
- Advanced Jar Materials: Developing lighter and more durable jar materials with minimal contamination potential.
- Improved Cooling Systems: Developing more effective temperature control systems for sensitive materials.
- Automation: Advancing automation and robotic systems for greater throughput and reproducibility.
- Scale-Up Studies: Improving the transfer of results from mini-scale to larger-scale production processes.
Conclusion
Mini planetary ball mills are crucial tools for research and development in various fields due to their versatility, efficiency, and precise control. They allow researchers to process small amounts of material to create extremely fine particle sizes, create homogeneous mixtures, and conduct detailed material studies. By understanding their mechanics, advantages, limitations, operational parameters, maintenance, and applications, you can maximize their use and contribute to advances in materials science, nanotechnology, pharmaceuticals, and many other areas. Whether it is for a new pharmaceutical formulation, or new nanomaterial, a mini planetary ball mill will continue to be an important and relevant piece of scientific equipment.