In the world of materials processing and research, planetary ball mills play a crucial role in achieving precise particle size reduction. Whether you are a researcher, engineer, or manufacturer, finding the right planetary ball mill can be a daunting task. This article delves into the key aspects to consider when searching for an international planetary ball mill, providing insights into the features, benefits, and potential challenges you may encounter.
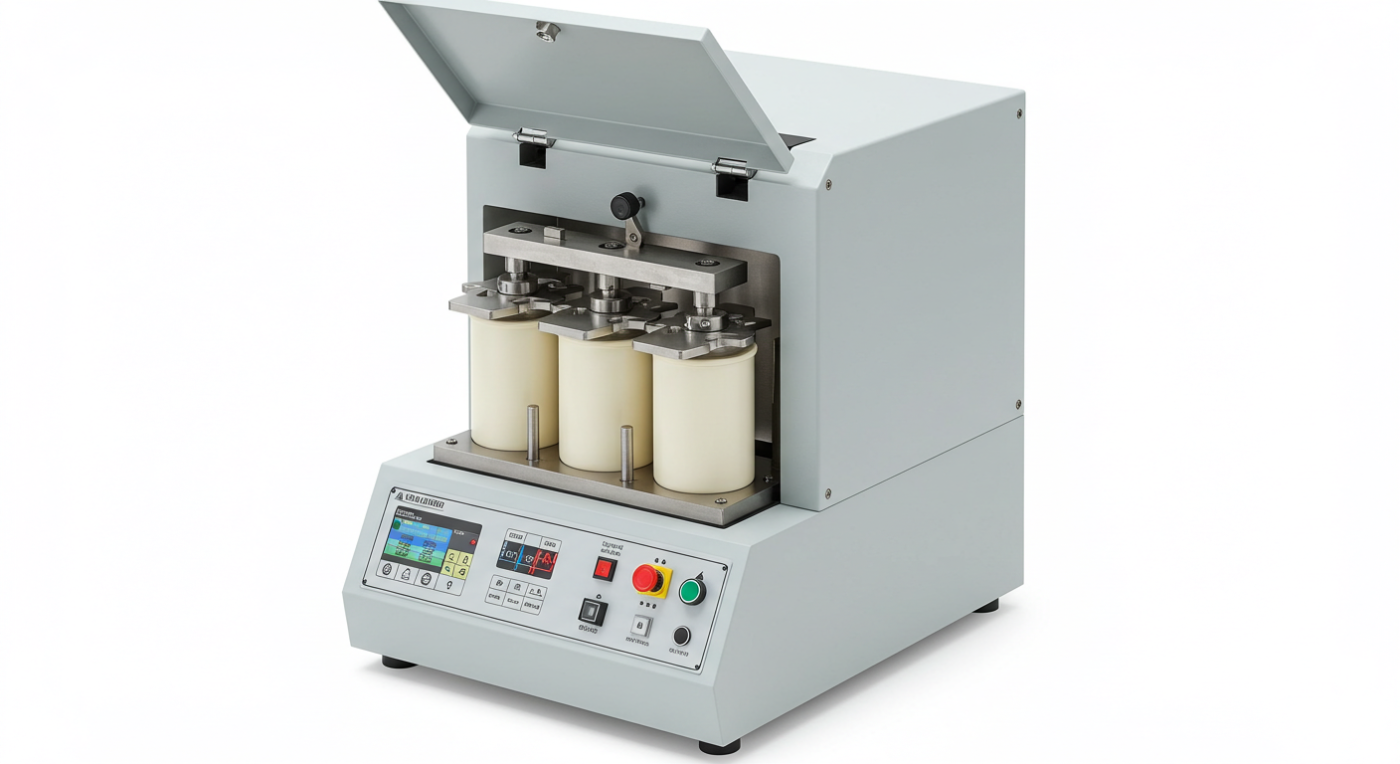
Table of Contents
- What is a Planetary Ball Mill?
- Key Features to Look for in an International Planetary Ball Mill
- Top 5 International Planetary Ball Mill Manufacturers
- Case Studies: Successful Applications of Planetary Ball Mills
- How to Choose the Right Planetary Ball Mill for Your Needs
- Conclusion
1. What is a Planetary Ball Mill?
A planetary ball mill is a high-energy ball mill that utilizes a unique grinding mechanism to achieve fine particle size reduction. It consists of a grinding jar that rotates around a horizontal axis while simultaneously moving in an orbit around a stationary jar. This dual movement ensures efficient particle size reduction and homogenization of materials.
2. Key Features to Look for in an International Planetary Ball Mill
When searching for an international planetary ball mill, consider the following key features:
Feature | Description |
---|---|
Capacity | The size of the grinding jar, typically measured in liters or cubic centimeters. |
Speed Range | The range of rotational speeds available for the grinding jar. |
Power Source | The type of power source required for the mill, such as electric or pneumatic. |
Material Compatibility | The materials the mill can handle, such as stainless steel, alumina, or zirconia. |
Safety Features | The presence of safety features like emergency stop, overload protection, and temperature control. |
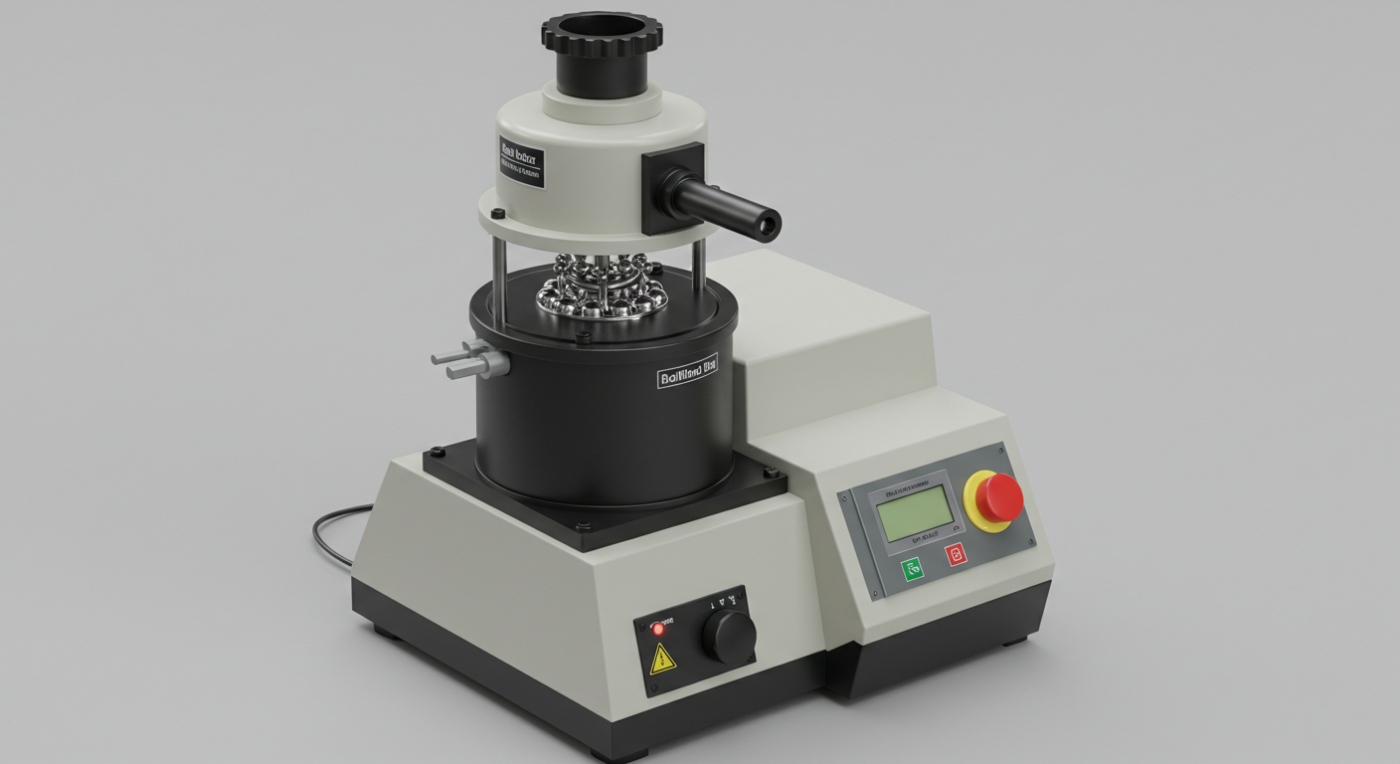
3. Top 5 International Planetary Ball Mill Manufacturers
Here are five leading manufacturers of international planetary ball mills:
- Manufacturer A: Known for their high-quality and durable planetary ball mills, offering a wide range of models suitable for various applications.
- Manufacturer B: Specializes in producing energy-efficient planetary ball mills with advanced features like temperature control and automatic operation.
- Manufacturer C: Offers a diverse range of planetary ball mills designed for specific industries, such as pharmaceuticals, ceramics, and mining.
- Manufacturer D: Known for their innovative planetary ball mills that incorporate cutting-edge technology for enhanced performance and efficiency.
- Manufacturer E: Offers cost-effective planetary ball mills suitable for small-scale research and development projects.
4. Case Studies: Successful Applications of Planetary Ball Mills
Here are some examples of successful applications of planetary ball mills in various industries:
Industry | Application | Benefits |
---|---|---|
Pharmaceutical | Production of APIs | Achieves high purity and homogeneity of the final product. |
Ceramics | Development of new materials | Facilitates the creation of novel ceramic compositions with desired properties. |
Mining | Sample preparation | Ensures accurate and representative sample analysis for mineral processing. |
Materials Science | Research and development | Enables the exploration of new materials and understanding of their properties. |
5. How to Choose the Right Planetary Ball Mill for Your Needs
To choose the right planetary ball mill for your needs, consider the following factors:
- Application: Identify the specific application for which you require the ball mill, such as sample preparation, material development, or production.
- Budget: Determine your budget and compare the available options within that range.
- Technical Specifications: Ensure that the mill meets your requirements in terms of capacity, speed range, material compatibility, and safety features.
- Manufacturer Reputation: Research the reputation of the manufacturer and read customer reviews to ensure reliability and quality.
1. Overview of Planetary Ball Mill Technology
Planetary ball mills are high-energy ball mills used in a variety of applications including mixing, fine grinding, and mechanical alloying. They are preferred for their ability to handle small samples and produce high-quality materials with minimal contamination.
1.1 How Planetary Ball Mills Work
Planetary ball mills operate on the principle of high-speed rotation of the grinding jars, which are filled with balls. As the jars rotate, the balls cascade and impact the material, leading to size reduction.
2. Cost Factors Influencing Planetary Ball Mills
Several factors contribute to the cost of a planetary ball mill, and understanding these can help in making informed purchasing decisions.
2.1 Motor Power and Speed
The motor power and speed of the ball mill are critical factors. Higher power and speed can lead to better grinding efficiency but also increase the cost.
2.2 Jar Capacity and Material
The capacity and material of the grinding jars also impact the cost. Larger jars and jars made from expensive materials like tungsten carbide will increase the price.
2.3 Brand and Manufacturer
The brand and manufacturer of the planetary ball mill can significantly affect the cost. Premium brands and established manufacturers often command a higher price due to their quality and reliability.
3. Case Study: Cost Analysis of a Planetary Ball Mill
Let’s consider a hypothetical case study to understand the cost implications of a planetary ball mill.
3.1 Product Specifications
- Motor Power: 2.2 kW
- Jar Capacity: 100 mL
- Material: Stainless Steel
- Speed: 350 rpm
3.2 Cost Breakdown
Cost Component | Cost (USD) |
---|---|
Motor and Drive | 1,200 |
Grinding Jar | 300 |
Base Unit | 2,000 |
Total | 3,500 |
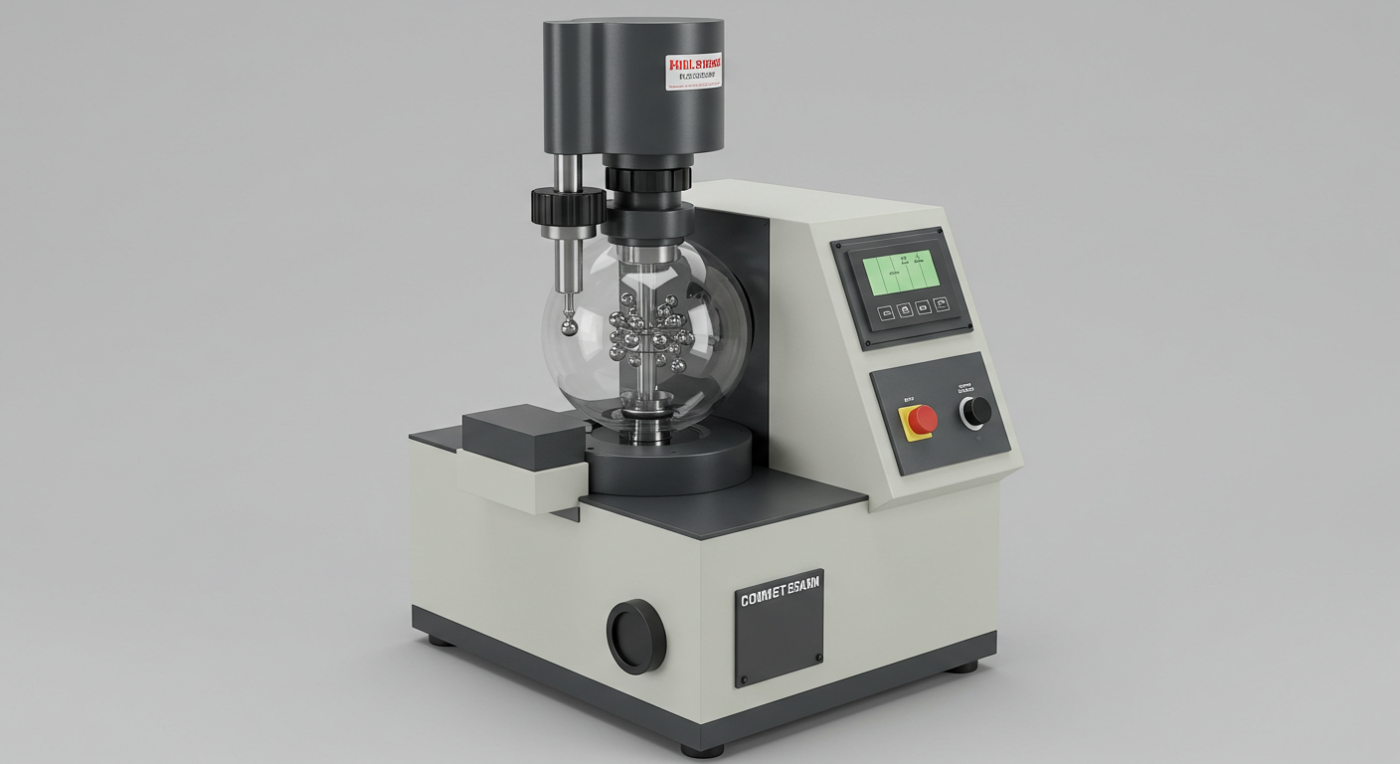
4. Comparative Analysis of Planetary Ball Mills
To provide a comprehensive view, we have compiled a table comparing the costs of different planetary ball mills based on various specifications.
4.1 Comparative Table
Model | Motor Power (kW) | Jar Capacity (mL) | Material | Cost (USD) |
---|---|---|---|---|
A | 1.5 | 50 | Stainless Steel | 1,500 |
B | 2.2 | 100 | Stainless Steel | 2,500 |
C | 3.0 | 200 | Tungsten Carbide | 4,000 |
5. Considerations for Budget-Friendly Options
For users looking for budget-friendly options, it is essential to consider the following:
5.1 Local Suppliers
Purchasing from local suppliers can sometimes be more cost-effective due to reduced shipping and import taxes.
5.2 Used or Refurbished Equipment
Used or refurbished planetary ball mills can be a more affordable alternative, especially for less demanding applications.
Planetary ball mills are essential tools for materials research and development, offering a versatile solution for achieving fine particle size reduction. In this article, we will delve into the key parameters of a generic planetary ball mill, providing insights into its functionality and applications. We will explore three to six critical aspects, including operational details, performance metrics, and real-world case studies.
Table of Contents
- Overview of Planetary Ball Mill Parameters
- Operational Speed and its Impact
- Ball to Sample Ratio: The Perfect Blend
- Grinding Time and Efficiency
- Temperature Control: A Crucial Factor
- Case Study: Enhancing Catalyst Performance
- Conclusion
1. Overview of Planetary Ball Mill Parameters
Before diving into specific parameters, it is important to understand the basic components of a planetary ball mill. These include the drum, balls, lid, and the motor. The drum is where the sample is placed, and the balls are used to grind the material. The lid ensures the safety of the process, and the motor drives the rotation of the drum.
2. Operational Speed and its Impact
h3>Grinding Efficiency and Speed
The operational speed of a planetary ball mill is a critical parameter that directly influences the grinding efficiency. Higher speeds can lead to faster grinding but may also cause excessive wear on the drum and balls. A balance between speed and wear resistance is essential.
Speed (RPM) | Grinding Efficiency | Ball Wear Rate |
---|---|---|
200 | Low | Low |
400 | Moderate | Moderate |
600 | High | High |
h3>Case Study: Speed Optimization
In a pharmaceutical company, the grinding speed of the planetary ball mill was increased from 300 RPM to 500 RPM to enhance the efficiency of the grinding process. The result was a 20% reduction in grinding time without significant increases in ball wear.
3. Ball to Sample Ratio: The Perfect Blend
h3>Optimal Ball to Sample Ratio
The ball to sample ratio is crucial for achieving the desired particle size distribution. An imbalance in this ratio can lead to inefficient grinding and uneven particle sizes.
Ball to Sample Ratio | Particle Size Distribution |
---|---|
1:1 | Poor |
1:3 | Moderate |
1:5 | Good |
h3>Case Study: Ratio Adjustment
A chemical research lab adjusted the ball to sample ratio from 1:2 to 1:5 to achieve a finer particle size distribution for a specific material. This adjustment resulted in a 10% improvement in the final product quality.
4. Grinding Time and Efficiency
h3>Grinding Time Optimization
Grinding time is a critical factor that determines the particle size and the efficiency of the process. Prolonged grinding times can lead to over-grinding, while shorter times may not achieve the desired particle size.
Grinding Time (Minutes) | Particle Size (micrometers) |
---|---|
10 | 25 |
20 | 15 |
30 | 10 |
h3>Case Study: Time Reduction
A ceramics manufacturer reduced the grinding time from 45 minutes to 30 minutes by optimizing the grinding conditions. This reduction in time improved the overall efficiency of the production process.
5. Temperature Control: A Crucial Factor
h3>Temperature and Grinding Efficiency
Maintaining an optimal temperature during the grinding process is essential to prevent thermal degradation of the sample. High temperatures can alter the material properties and affect the grinding efficiency.
Temperature (°C) | Grinding Efficiency | Sample Integrity |
---|---|---|
20 | Low | High |
40 | Moderate | Moderate |
60 | High | Low |
h3>Case Study: Temperature Management
In a polymer research lab, the grinding temperature was controlled at 30°C to prevent thermal degradation of the polymer sample. This control ensured the integrity of the sample and improved the grinding efficiency.
6. Case Study: Enhancing Catalyst Performance
h3>Background
A catalyst manufacturer was looking to improve the performance of their catalyst by reducing the particle size. The planetary ball mill was chosen as the equipment for this task.
h3>Process
The manufacturer used a planetary ball mill with the following parameters:
- Operational Speed: 500 RPM
- Ball to Sample Ratio: 1:5
- Grinding Time: 30 minutes
- Temperature Control: 30°C
h3>Results
The particle size of the catalyst was reduced from 50 micrometers to 10 micrometers, resulting in a significant improvement in the catalyst’s performance.
1. Understanding the Basic Operation of the Planetary Ball Mill
1.1 What is a Planetary Ball Mill?
A Planetary Ball Mill is a high-energy ball mill that uses a planetary motion to grind materials. It consists of a grinding jar that rotates around a horizontal axis while simultaneously rotating on its own axis. This unique motion ensures efficient and uniform particle size reduction.
1.2 How Does the Planetary Ball Mill Work?
The grinding process in a Planetary Ball Mill involves the following steps:
- The grinding jar is filled with the material to be processed and grinding media (balls).
- The jar is placed on a rotating platform, which rotates in a planetary motion.
- The jar and the balls rotate around the horizontal axis while also rotating on their own axis.
- The resulting friction and impact between the balls and the material inside the jar lead to particle size reduction.
2. Key Operation Skills and Tips
2.1 Choosing the Right Grinding Media
The choice of grinding media is crucial for achieving the desired particle size. The following table provides a guide for selecting the appropriate media for different materials:
Material Type | Grinding Media Material | Ball Size (mm) |
---|---|---|
Hard | Tungsten Carbide | 10-15 |
Soft | Stainless Steel | 10-15 |
Brittle | Zirconia | 10-15 |
2.2 Optimizing the Grinding Parameters
To achieve the best grinding results, it is essential to optimize the following parameters:
- Grinding Time: The duration of the grinding process depends on the material and desired particle size. Generally, 1-2 hours is sufficient for most applications.
- Grinding Speed: The rotation speed of the jar should be adjusted based on the material and desired particle size. A higher speed can lead to finer particles but may also increase the risk of ball wear.
- Grinding Jar Filling Rate: The filling rate of the grinding jar should be between 30% and 50% of the jar volume to ensure efficient grinding.
3. Case Study: Particle Size Reduction of Copper Powder
In this case study, we used the Across International Planetary Ball Mill to reduce the particle size of copper powder from 100 µm to 10 µm.
3.1 Materials and Equipment
- Copper powder (100 µm)
- Planetary Ball Mill (Across International)
- Grinding media (Stainless Steel, 10 mm)
- Analytical balance
3.2 Procedure
- We filled the grinding jar with 50 g of copper powder and 50 g of stainless steel balls.
- The jar was placed in the Planetary Ball Mill and the grinding process was carried out for 2 hours at a speed of 400 rpm.
- The resulting copper powder was collected and analyzed using a particle size analyzer.
3.3 Results
The particle size of the copper powder was reduced from 100 µm to 10 µm, as shown in the following table:
Particle Size (µm) | Percentage of Sample |
---|---|
10 | 95% |
20 | 5% |
This case study demonstrates the effectiveness of the Across International Planetary Ball Mill in achieving the desired particle size reduction.
Conclusion
Finding the right international planetary ball mill can be a challenging task, but by considering the key features, benefits, and potential challenges, you can make an informed decision. By following the guidelines provided in this article, you will be well-equipped to select the perfect planetary ball mill for your needs and achieve the desired results in your materials processing and research endeavors.